Articles
Name | Author | |
---|---|---|
CASE STUDY: Elevating efficiency at King Aerospace | Chris Ranno, IT Manager, King Aerospace | View article |
CASE STUDY: Elevating AirAsia’s Fleet Management | Mohd Solleh Mustafar, Engineer, Maintenance Operation Control, AirAsia and Mahendran Doriasamy, Transformation Manager, Asia Digital Engineering (ADE) | View article |
CASE STUDY: Faster and better document comparison at SunExpress | Mehmet Dinç, Documentation Specialist, SunExpress | View article |
CASE STUDY: Condor leaves the paper behind | Holger Barth, Head of AMOS Competence Center and Technical Documentation, Condor Airline | View article |
CASE STUDY: Condor leaves the paper behind
Author: Holger Barth, Head of AMOS Competence Center and Technical Documentation, Condor Airline
Subscribe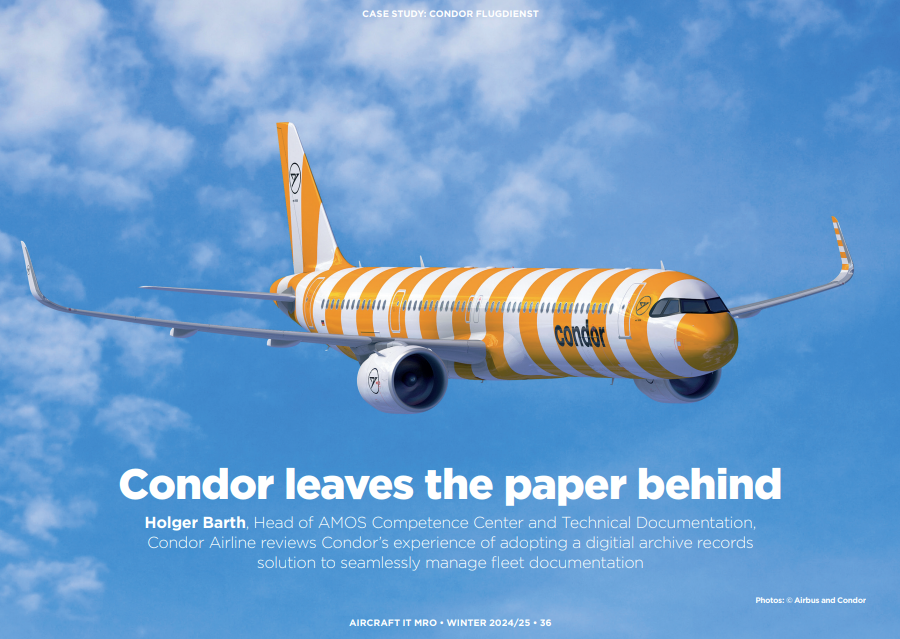
Holger Barth, Head of AMOS Competence Center and Technical Documentation, Condor Airline reviews Condor’s experience of adopting a digitial archive records solution to seamlessly manage fleet documentation
I want to use this article to share with readers our project to effect a digital transformation at Condor and, specifically our adoption of a digital tech records system as one of the steps along our way to a more digital organization. But first, to provide the context in which this is all taking place, let me introduce you to the airline at the heart of the case study.
CONDOR AIRLINE
We’re very proud of the fact that, as our slogan says, “Condor is vacation”: we are a leisure carrier which is now taking more and more, for example, North Atlantic routes. The airline’s history started in 1955 (figure 1).
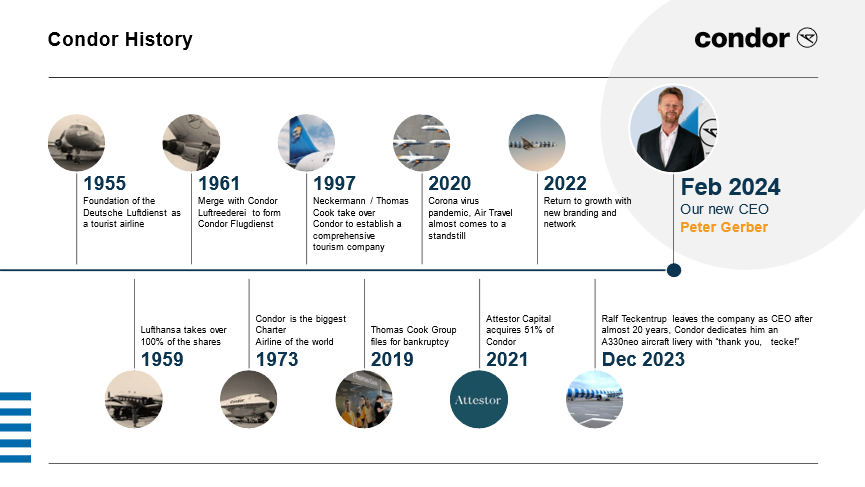
Figure 1
Soon after Condor started, it was taken over in 1961 by Lufthansa and was part of the Lufthansa group for many years until 1997 when the airline became part of the Thomas Cook Group. However, since the Thomas Cook Group collapse in 2019, Condor has had a very challenging time. The company had to be rebuilt in a new way and had to re-invent Condor as a new business. An investing company acquired 51% of the business in 2021 and invested in a new fleet of more modern aircraft: since 2022, we have been ‘the striped airline’ with a new eye-catching livery and we also have a new CEO who joined this year.
The company profile is that Condor has been flying since 1956 and currently serves about 90 vacation destinations; it is Germany’s most popular vacation airline with a new striped livery inspired by beach towels and parasols. At the end of 2022, we inducted the first aircraft for the planned fleet transformation, an Airbus A330neo. The future fleet will include 62 aircraft, all Airbus and all with neo engines: all fuel efficient, low emissions and low noise which will soon make us the greenest airline in Europe (figure 2).
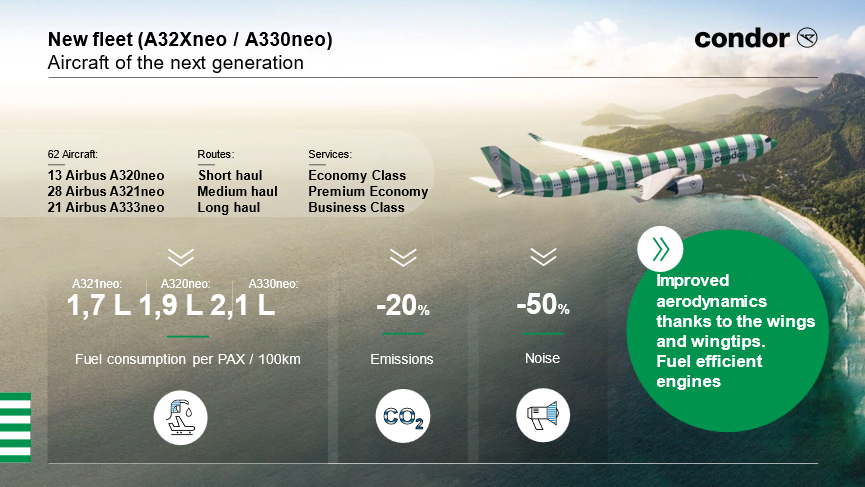
Figure 2
However, changing to a new fleet takes a lot of effort and energy. Since November 2021 when we started the re-fleeting process and up until the time of writing, we had phased out 16 long-haul Boeing 767s, two 757s, four Airbus A330ceo and four A320ceo. At the same time, we phased in 16 Airbus A330neo, four A330ceo, which were interim aircraft for the transition, as well as one A320neo and one A321neo. Our average fleet age, will fall from nearly 20 years to less than half of that by the end of 2024, eight and a half years (figure 3).
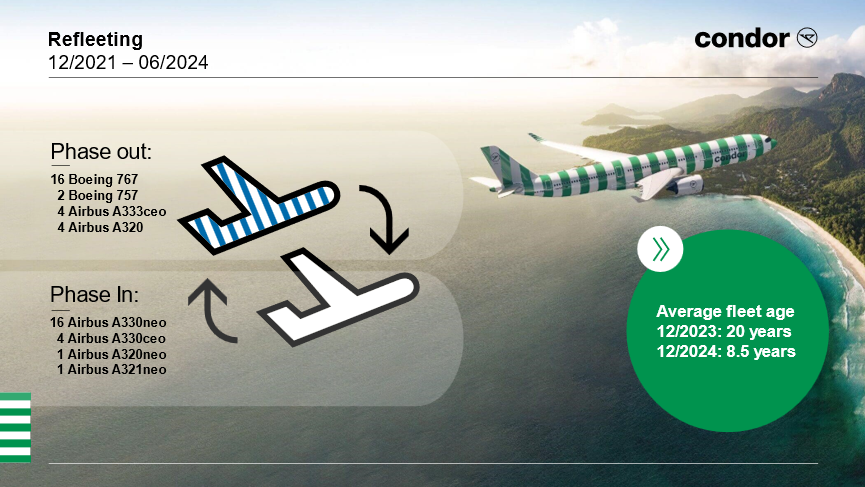
Figure 3
This is all good but it leads to a challenge.
THE CHALLENGE
As readers will know, in terms of paperwork, aircraft do not travel light (figure 4).
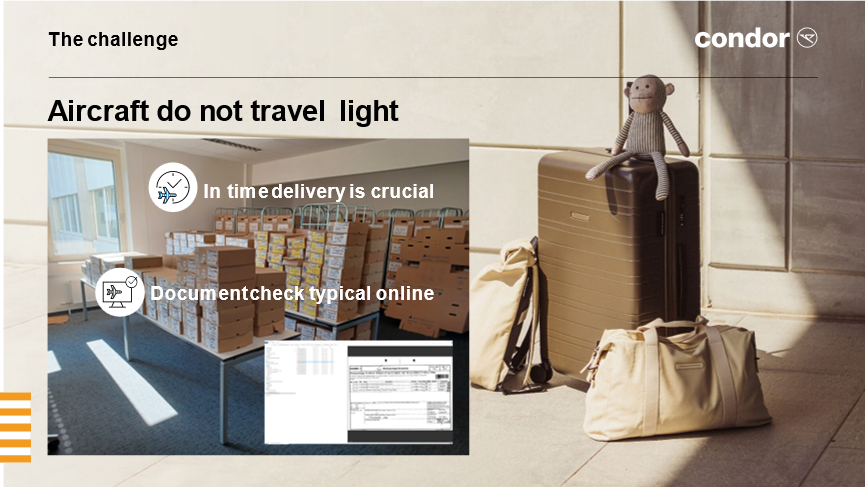
Figure 4
They carry with them lots of documents which have, traditionally, been recorded and saved on paper. The delivery of the paperwork and the records is crucial for keeping contracts. The good thing is that most of the document checks are performed online today, based on scans and digital systems, making it a little bit easier. In keeping with that, we have developed a vision for Condor and the vision is to have a digital CAMO. It’s not just one project but rather it’s a jigsaw (figure 5).
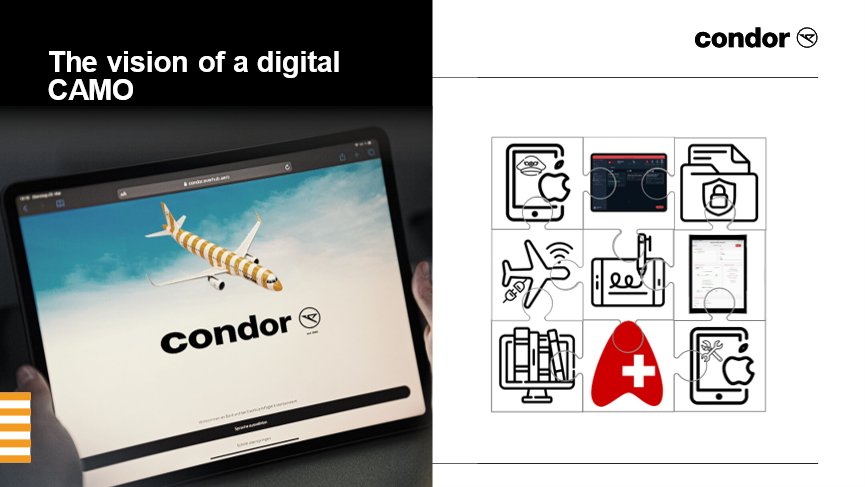
Figure 5
The main part of this jigsaw in our airline community is AMOS, the main M&E system and, as part of that, we’ve already started to issue iPads for the maintenance team. We have added a technical library to it and have started using AMOSmobile. That might seem like just one step but, anyone with experience of this will know that, if you want to have an eSignature approved, getting authority approval takes a little bit longer; so, the next step was that we were waiting for that approval by summer 2024.
Our new fleet gives Condor a good framework with connected aircraft and they all have the full FOMAX connectivity package, our pilots are also already equipped with EFBs. As a logical consequence, we are part of the AMOS Swiss-AS ETL project as a founding group customer and, after all the paperwork has been done, it needs to become part of a digital archiving solution. This was one of the things that we started to source and found it a good solution. It’s what I want to talk about in this article.
THE SOLUTION
For the first step we started to directly scan our maintenance records into the MRO system, we had scanned previously but not directly into the MRO system, but it did mean that we had lots of scans already available (figure 6).
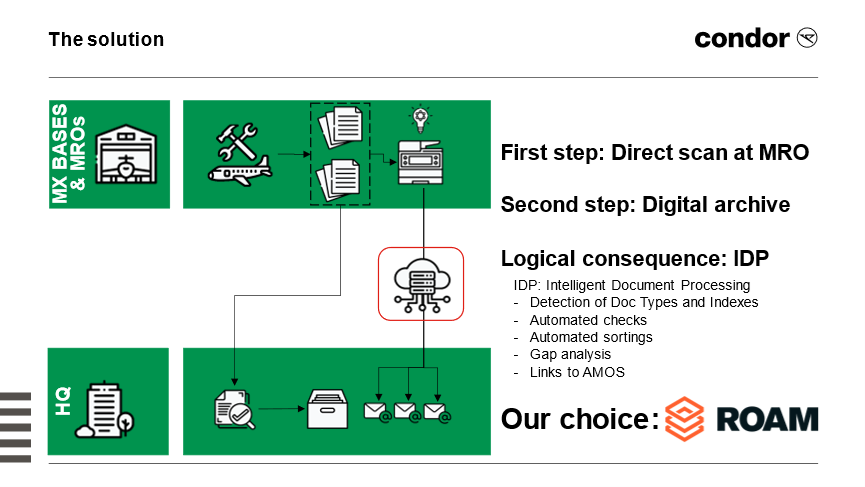
Figure 6
The second step was to put those scans into a digital archive. However, if you simply scan your paper documents and put them into a digital archive and do digitally what was done on a shelf before, that is not digitalization, it’s just print but in a PDF format. The logical solution is Intelligent Document Processing (IDP), let the scans go through a system, detect the document type and what it is, perform automatic checks, sort it automatically, perform a gap analysis, count pages, check stamps… all things that consume a lot of time and people unless we can make it a more automated process. Finally, of course, we want it to link back to AMOS so that our staff can be looking at AMOS, see a work order and, if they want to see the dirty fingerprints, there should be a link where the user can click and see the scan of the original document.
With all this, we conducted a selection process and looked at many solutions from big providers for document processing, including AI providers; but finally, and considering our needs and future ambitions, our choice was ROAM from Gamit.
Here is a brief description of the ROAM ecosystem.
THE ROAM ECOSYSTEM FROM GAMIT
Anthony Wilkinson, Business Development Manager from Gamit in the UK
ROAM is a piece of software for which there was a need. Gamit actually operates an airline, Tailwind, an ACMI based in Türkiye and we were facing many problems, specifically with aircraft records.
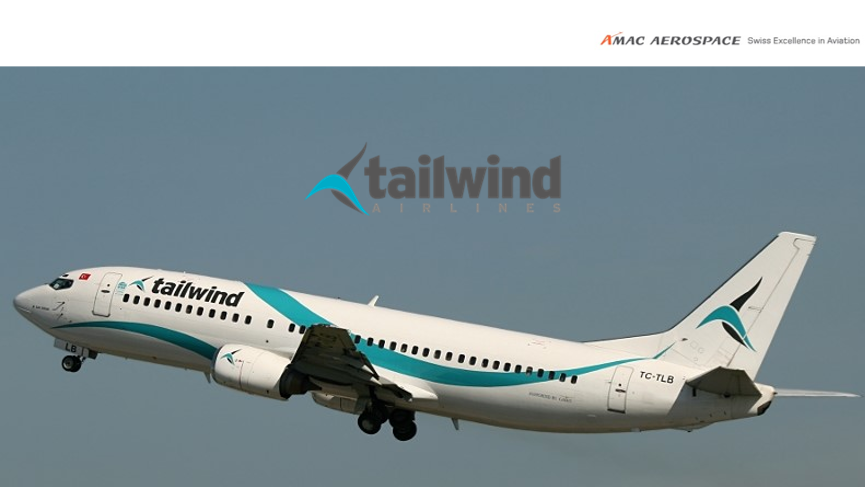
So, we decided to see whether we could solve those problems and, in doing that, we started developing software and situations that can help us better manage our costs and everything.
ROAM itself, can take a paper document or a digital document, layer it with OCR and it will then extract metadata from that information to enable the system to push everything into a very indexed and searchable situation. Figure 7 shows the range of capabilities in ROAM.
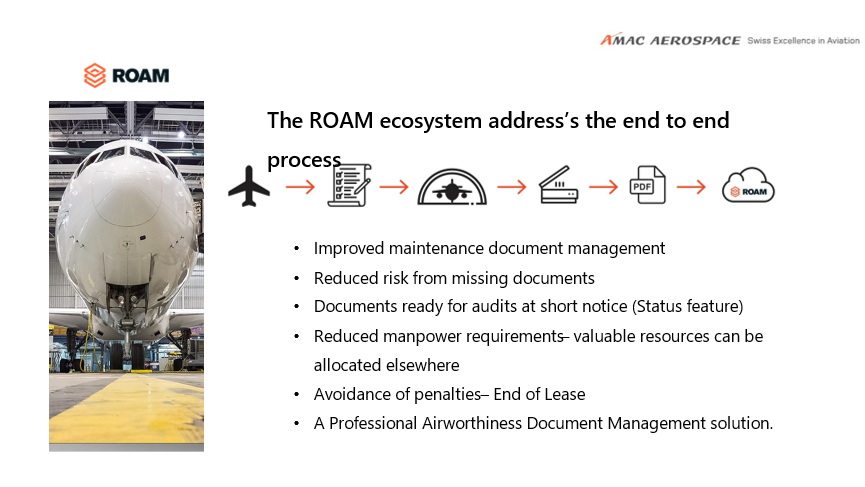
Figure 7
My way of describing it would be to say that ‘ROAM turns your documents into a Google because, for everything you need to find, you can type in the OCR search bar and it is right there for you. it can highlight all of the search terms that you’re looking for on the page, so that you can see that happening, and it does everything that you need. ROAM is particularly good when it comes to aircraft transitions and is able to do things with end-of-lease binders very quickly.
INTELLIGENT DOCUMENT PROCESSING
I’ve tried to describe this concept in figure 8.1.
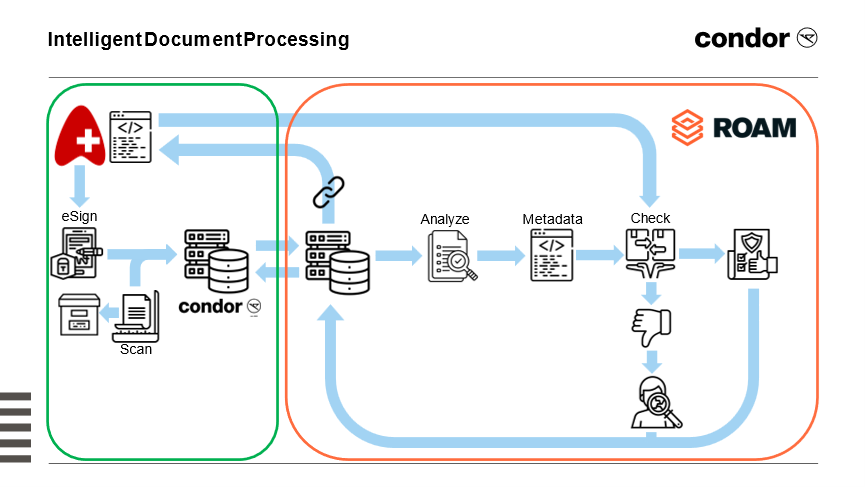
Figure 8.1
The area bounded by the green line is the Condor area and on the red side is thee ROAM environment. At the start, it is hybrid; there are papers, scans and digital documents. There is nothing unusual in this but we have to try to merge them all into one common process to have one common outcome. This is what we developed with ROAM. At the time of writing, we had to manually enter the scans into the system as our eSignature was not yet fully approved; but we put the data into the system very directly and push it into the ROAM environment. We do the same with our AMOS metadata: AMOS can generate lots of reports triggered by starting execution of maintenance, time base whatever you want and we also push those metadata to ROAM which then analyzes the documents but not just adding an OCR layer; it really generates structure data: document type, document number and other data. And the most important thing, because we are phasing out old aircraft, there are different types of scans and different types of documents in the history, the system needs to be trainable to manage scans and paperwork the same way to support the process for the new aircraft. For those new ones, it’s easy, we have control, we can include QR codes and barcodes, we can do everything to make it easy for the IT system. But the backlog is a headache.
With the analysis, we can generate the metadata and can compare those metadata in the GAP analysis directly with the data from AMOS (figure 8.2).
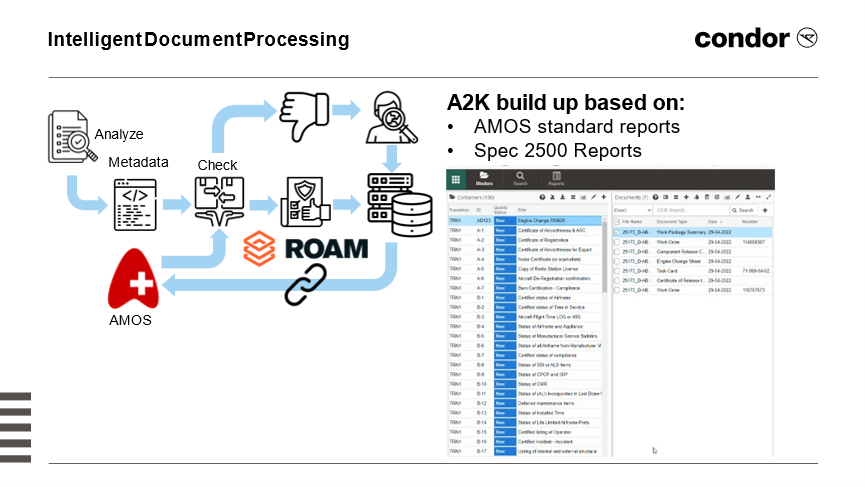
Figure 8.2
Nobody has to count pages because AMOS sends all the information about the content to the system and the system checks that all work orders are there and all task cards are there; so there is nothing to do anymore.
If there’s a gap, then someone has to go to Maintenance and look for paperwork. If all of those checks are performed, the documents are in the system and sorted, the link is pushed back to the scan and into our MRO system because, typically, if someone is looking for the history he won’t go through pages of dirty fingerprints (figure 8.3).
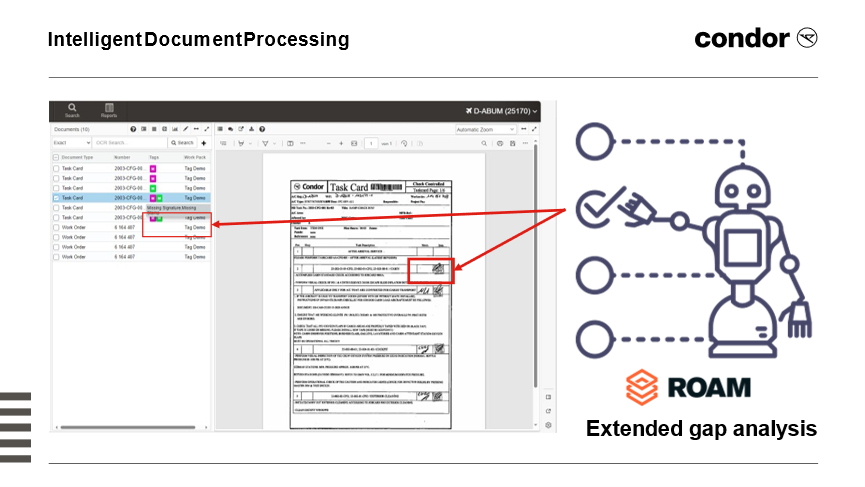
Figure 8.3
He used to have to look to see whether his AD has been performed with the work order, find it, and he might find that somebody asked for the dirty fingerprint, the old way, which workpackage is it in, where is it stored and where to go to find it. Now and in the future, all he needs to know is that there’s a link, click on it and he’ll be fine.’
This is what we built for the basic maintenance records but that’s not everything. Delivering an aircraft back to a lessor or providing audit paperwork, there is a structure called A2K and we want to build it up automatically. Readers will know about SPEC2500 Aircraft Transition Records, they have a structure, the A2K binder has a structure, lessors have structures also. Sometimes they like how we do it, sometimes they want done it in a different way; the basic content is usually the same. So, it’s, build a folder structure or a template, how to put the paperwork together so that the system knows ‘this is an AD (Airworthiness Directives) note, to the AD note I add a service bulletin, I have a dirty fingerprint, I put it into a folder, set it up there and I can present this to the airline, to the lessor, to the authority.’
By building up those folders automatically, on the fly, while the system is running, we are gaining a daily audit compliance. My dream is that, when anybody calls me to report that they are phasing out an aircraft, I can simply say, ‘send me an email’ and then I can send them the A2K binder. ROAM enables us to build the A2K binder for each aircraft to the template that the particular lessor wants. Each aircraft has its lessor, each owner has access to the records for their aircraft and they will be organized in the way that lessor requires. We always try to encourage lessors to accept the A2K which is an international standard because we want to avoid having too many templates to manage or folders to move but whatever they want will be possible with ROAM.
The next thing and a very important point for us working in a multi-center system, having many base maintenance events outside another company so that we don’t always have full control of the paperwork, is that we want to have an automatic check of the task cards. maybe it’s not necessarily a need for a part CAMO organization to have the task card and details but if you do get it, you can be sure that your records are fine; and if the lessor or the auditor finds it, it always starts having discussions.
Our idea was to scan the document, detect the stamp areas and show that it is stamped; at least a logical check. This automated extended GAP analysis was also provided by ROAM and, as I said, it was a really important issue for us, especially with the 30 years old records that we have.
We have digitized that process and we now scan in our receiving documents plus we have Euro-pallets full of the old filing folders. When we return an aircraft, all the aircraft documentation is easy to take out of storage and send with the aircraft. Then we come to our receiving. We were, at the time of writing, in the process of digitalizing them to put them directly into ROAM. Also, as I have already mentioned, all of the important information comes from AMOS. If we have a closed workpackage, we have the labor bookings, with the labor booking we have a link to the certificate and then we can sort those into the workpackage. One idea is to throw away the form 1 after it has been scanned because after installation, it’s obsolete anyway. However, the materials department disagree with that because we might want to sell the part so keep the form with the part. But we do have it scanned. How we handle this with the paperwork was not yet decided at the time of writing.
THE PROJECT AND TIMELINE
Now, let’s look at the project and the timeline. It did not take years even though there were some hiccoughs along the way. We started the project officially in November2023 and, as already mentioned, we are going through a phase of returning many aircraft so our resources are very much bound into lease returns. The first three months, we put all of our resources together with Gamit and ROAM in delivering aircraft Specs and starting to work with the system and learn to know the system better. Since March, we have set up the interfaces between AMOS, the first ones, and also transferred data on a business basis. That wasn’t for all the aircraft, we started with the new ones which was easier because we had control of all the documents and there was not too much of a backlog (figure 9).
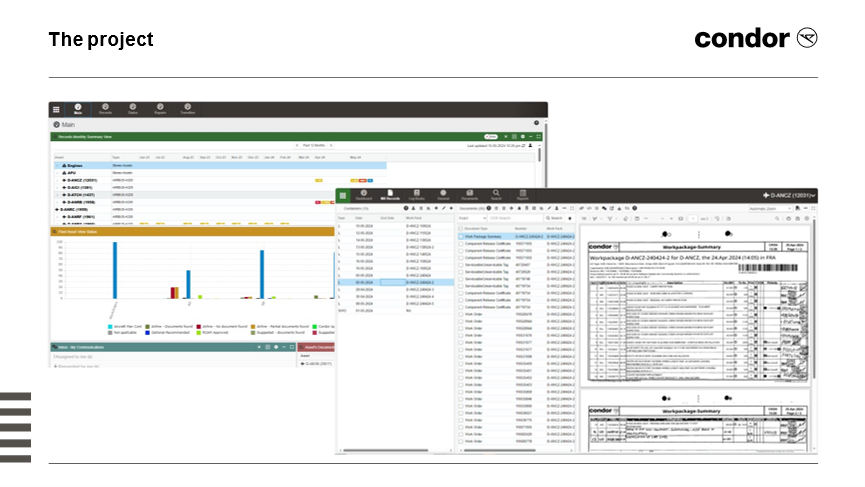
Figure 9
In figure 9 you can see one of our new aircraft set up directly in ROAM, you can see the structure of the fleet with the engines installed as they are installed. You can select the workpackage and then you see the content of the workpackage indicating what document type it is, what index number. And then you have Google; look for a work order number and you find the work order whose number you typed in. This makes all of the automated searches, it’s much more efficient and powerful; it also has a good UI and usability that makes it very easy to flip through the pages.
The implementation so far
Since May 2024, we have started to upload more data and to train the system and, step by step, we will also start uploading more historical records; our realistic goal was that, by October 2024, we would have a full live system for our workpackages, direct records, archiving system (figure 10).
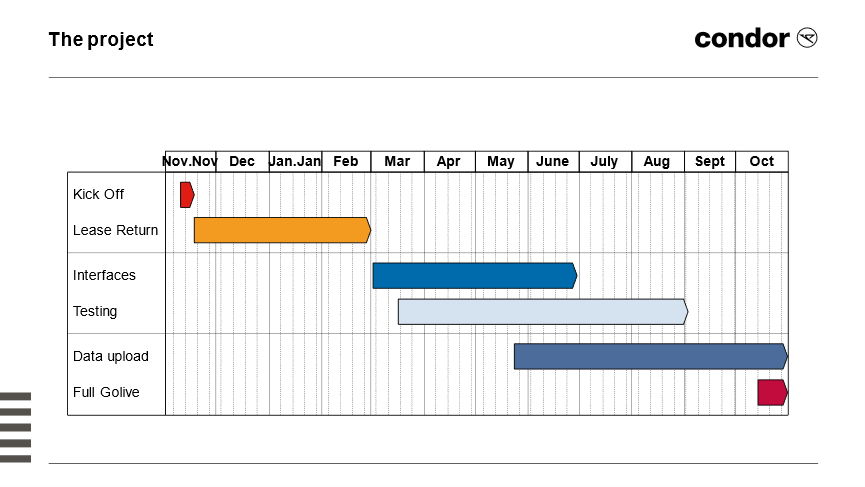
Figure 10
That has been our story at Condor: it has been a pretty straightforward project made better by the quality of IT partner we selected. If you are embarking on or even considering embarking on a similar project, then I hope that this case study will make useful reading for you.
Comments (0)
There are currently no comments about this article.
To post a comment, please login or subscribe.