Articles
Name | Author | |
---|---|---|
Case Study: Achieving productivity gains through an Integrated M&E System | Julien Lebeau, Project Manager, Air Tahiti | View article |
Case Study: Managing and synchronizing devices of all types at Air Canada | Keith Dugas, Director, Maintenance AI & Connected Operations, Air Canada | View article |
Case Study: Digital transformation and mobile apps for paperless maintenance | Juan Miguel Sánchez García & Francisco De Borja Mas Boned, Air Europa | View article |
Case Study: Enabling continuous data exchange between Lufthansa and Rolls-Royce Digital Services | Lena Duken, Airworthiness Engineer, Deutsche Lufthansa AG Jeff Winter, Senior Consultant, Deutsche Lufthansa AG | View article |
Case Study: Digital transformation and mobile apps for paperless maintenance
Author: Juan Miguel Sánchez García & Francisco De Borja Mas Boned, Air Europa
SubscribeJuan Miguel Sánchez García and Francisco De Borja Mas Boned, both of Air Europa, share the selection and implementation of a suite of mobile apps
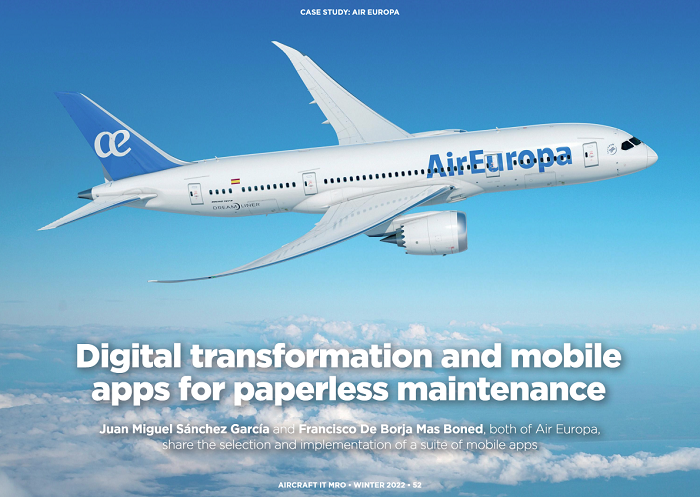
We are writing this article to share with industry colleagues our experience because sharing successful experience benefits everybody. As with any case study, in order to fully understand the story, it’s useful to know something about the subject of the study, in this case, Air Europa. So, we’ll begin with an introduction to the airline.
AIR EUROPA
With more than 60 destinations served in Europe and the Americas, Air Europa is Spain’s third largest airline with a fleet of Boeing 787-8 and -9, Boeing 737, Embraer E195 and ATR 72 aircraft. There are more than 3,000 employees across the three organizations within the business. But what were the reasons for undertaking this challenging project in the worst possible economic situation due to the Covid pandemic?
THE REASONING BEHIND THE PROJECT
In 2017, Air Europa came to the realization that we needed to upgrade the maintenance and engineering IT solution used by the airline. There was an internal analysis carried out to establish the basis for the project and what we realized from that was that, the maintenance department had a different management eco-system that had been developed in-house with separate solutions for each department and their users; every one of those systems had their own database which meant that not all users could share information so were not working with the same information. This made engineering, logistics and planning very difficult. Furthermore, these systems were based on obsolete technology which did not allow improvement to the systems or the development of mobility tools. And, without mobility tools, it was going to be difficult to apply the paperless policies that we wanted or to improve the efficiency of processes, or work in real time.
THE MAINSTAYS OF THE PROJECT
The conclusion was that we needed a new IT tool; we needed to change but that change needed to be aligned with Air Europa’s broader digital transformation plan, the vision for that plan and its mainstays (figure 1). Based on that, we defined our goals and the requirements for the new system.
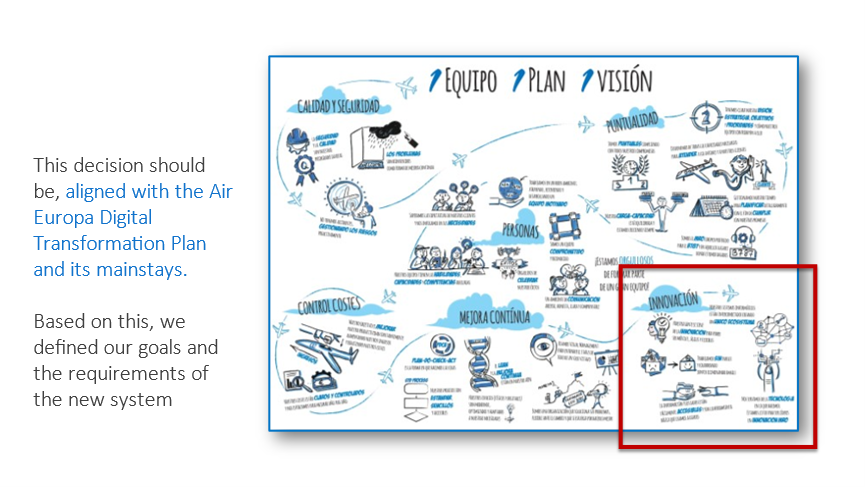
The vision is built on six mainstays: safety and quality assurance, cost control, continuous improvement, innovation, punctuality and, in the middle, people. Also, the decision to undertake a project like this must be aligned with the vision for Air Europa. Based on this, we defined our own goals (figure 2)
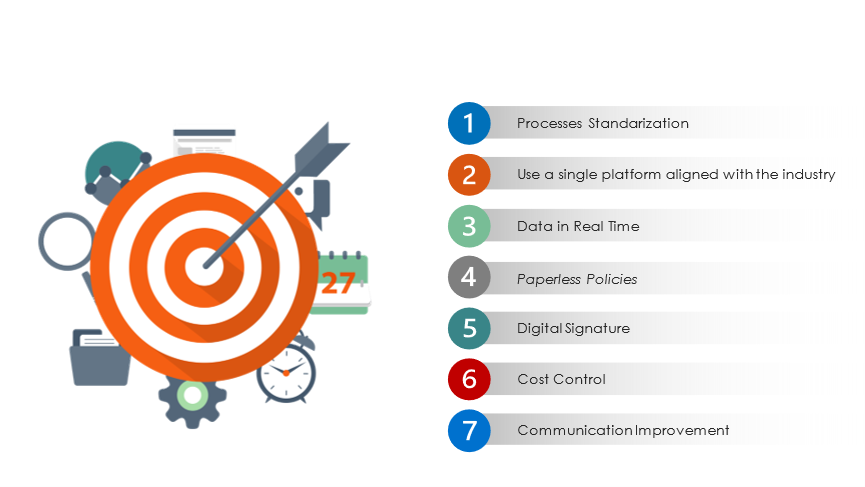
We wanted to standardize Air Europa’s internal processes and align them with the vision as well as industry standards, and we wanted to work with a single platform accessing the same information at the same time, very important. We wanted to be able to work in real time and to remove as much paper as possible from all processes. In a similar vein, we wanted to apply a digital signature capability while maintaining cost control and with improved internal communication using the same language – where there are different products or tools in use, they don’t always talk the same language.
After benchmarking, analyzing different proposal, and the pros and cons of each one, we determined that Trax was the solution that best met our requirements, not only because the tool met eighty or ninety percent of Air Europa’s digitalization requirements but also, they were open to the idea of modifying or adding new functionalities in order to cover the rest of our requirements.
To make things clearer, we’ve broken this article into two sections. First, before the GoLive, the planification of the project and how we arrived at that and then, what happened after the GoLive.
PLANNING, IMPLEMENTATION AND HIGHLIGHTS
At the outset, we implemented the eMRO platform from Trax for the back office, and we deployed the Air Mobility platform. We wanted to deploy a maintenance application to help us to better control defects management as well as task planning and manuals. We also wanted the plan to focus operations on the pilots and cabin crew.
At the top of figure 3, we can see the initial plan.
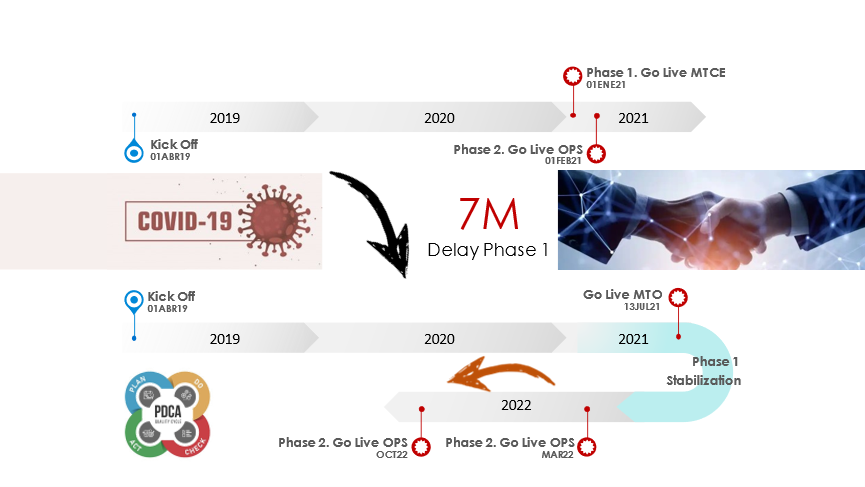
Starting on 1 April 2019 the expectation was that, in two years, we could have completed two phases of the plan; the first phase for Maintenance and the second phase for Operations, deploying the electronic Cabin Log App and electronic Technical Log Book with the Pilot App. Unfortunately, we encountered two problems during this process and that caused us to re-define the project.
The first was that we needed to re-define the elements in the project. Initially we had included not just the airlines in the group, Air Europa and Air Europa Express, but also included the MRO as part of Globalia Holdings. However, the process, currently underway, for selling the airlines to IAG does not include the heavy maintenance business. We had to re-define the project leaving out the MRO. The second problem probably needs no further explanation; we’ve all suffered the consequences of Covid and, unfortunately, many companies went out of business.
These problems together made re-defining the project necessary. One of our main visions at Air Europa is continuous improvement and we applied this philosophy in order to continually adapt the project and the planning. The result was, as can be seen on figure 3, after the seven months of delay proposed for phase 1, we went to GoLive.
THE GOLIVE AND AFTER – THE REAL LIFE
We gave ourselves just seven months but, in the end, we did it. One of the most important things with this project and the reason we succeeded was the Team. We had to identify experts in order to train them on the new platform which is eMRO, redefine all of the processes in the company and help employees to understand the new processes that the company would be implementing (figure 4).
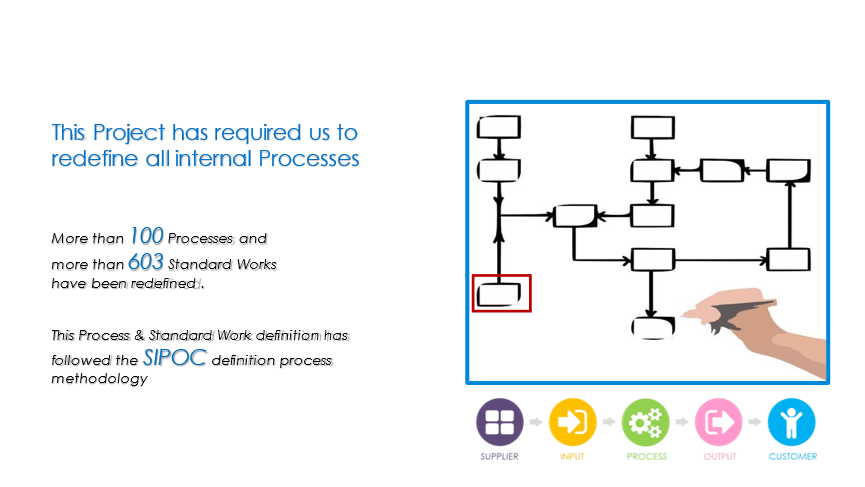
When there were, in the past, systems that were not connected, people just thought about the area in which they worked, they didn’t think globally. We needed to train them, in order to understand these new and connected processes, to think globally.
This kind of project, as you can imagine, meant that the people in the company were out of their comfort zone, needing to re-define all the processes. If you have this kind of stress, as we faced it, in the middle of the pandemic, then you can imagine the impact and the consequences was a record of temporary employment regulation, an unfamiliar situation and all at the same time. It was very hard but the aptitude and attitude of the workforce, with hours of hard work, ensured that we got through the project.
During this project, we had to redefine more than one hundred internal processes at Air Europa, as well as more than 600 standard work procedures, all based on the SIPOC (Suppliers, Inputs, Process, Outputs and Customers) methodology for definition in order to ensure that all processes in the company were part of a big chain and compatible with one another. Another key task for this project was the migration of more than thirty years of data with some 576 million records across seven systems (figure 5).
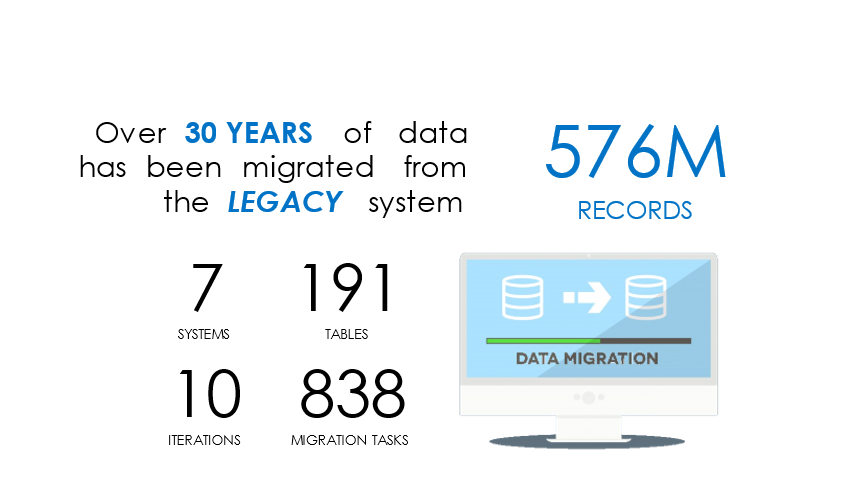
It required more than ten iterations until the data could be confirmed as accurate. The data was also cleaned before we were able to operate with it. There were different sources such as logistics from CAMO and tools that had to be separated and all put into the same system. Then, when all of that was in place, in July 2021 we completed the GoLive which took 36 hours; but that wasn’t the whole thing. It’s easy to think that, when you have completed a GoLive, everything has been done but that is not the case.
Just before GoLive the on-site Trax consultant shared a video called ‘Life after GoLive’. It’s an interesting video because it shows the most important challenges and problems that are faced after deployment of a project. Although the video refers to an Office 365 deployment, the main problems that we faced in Air Europa were the same (figure 6.1).
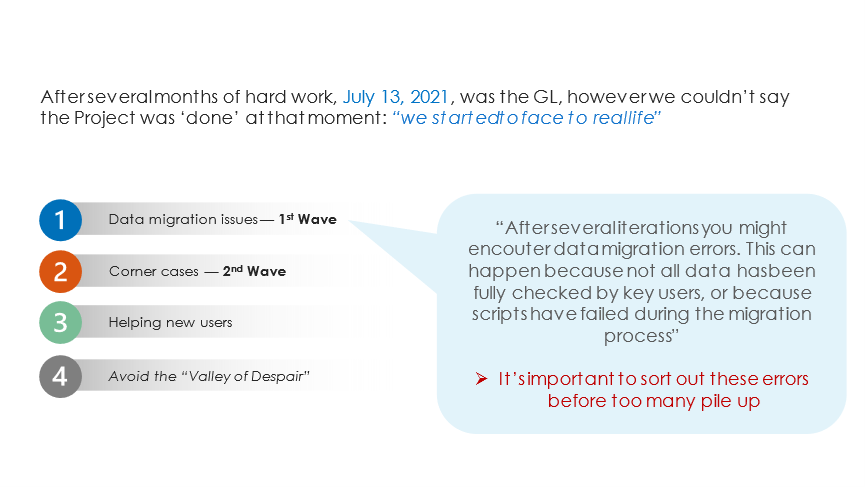
We faced for key issues.
The first one was data migration. We had completed several iterations and thought that all was now clear but it was impossible to be sure that all the information was ready. Some errors became apparent after the GoLive and it’s important to sort out any such issues because, if you don’t do it, they will pile up.
The second issue (figure 6.2) was the corner cases.
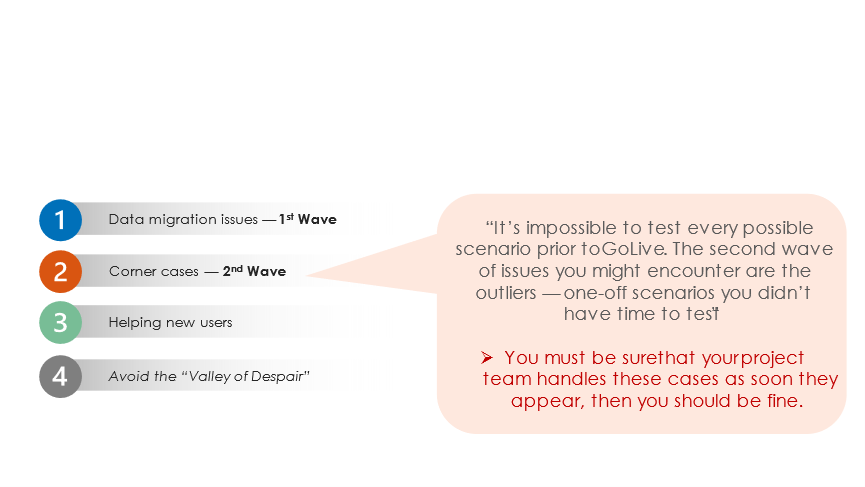
We performed a lot of simulations, defined a lot of processes and tested them but it is quite impossible to test all the system and all possible cases that might arise. Therefore, it is important to prepare to face the processes and cases that might not have been tested because additionally, maybe, we might have created data in the wrong way which will lead you back to the first problem.
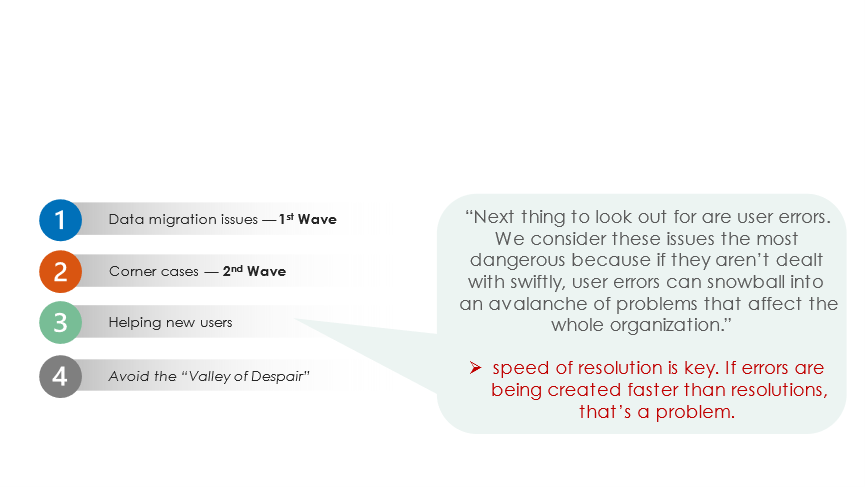
Air Europa spent a lot of time training users but needed to GoLive with just sixty percent of users fully trained. That means that the forty percent who had yet to complete their training could cause errors in the system that needed to be corrected as soon as possible because, if left unsorted, small errors can generate large problems.
Nowadays, we are facing the fourth issue which is trying to avoid the ‘Valley of Despair’ (figure 6.4).
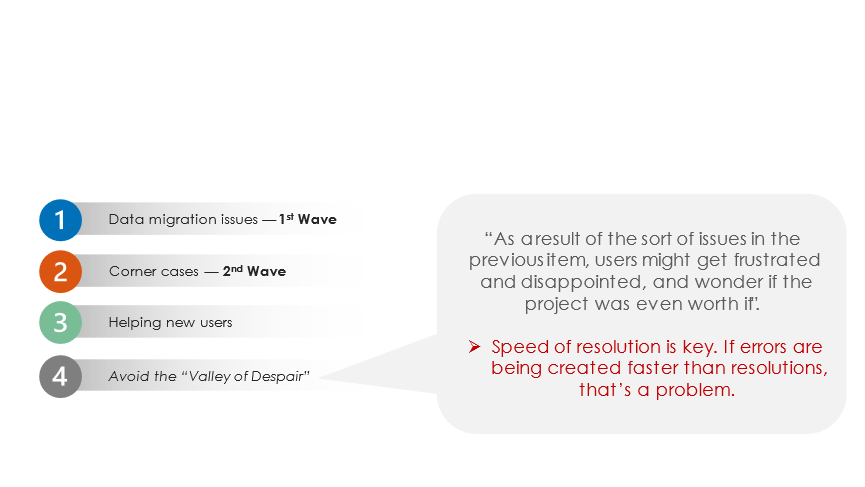
Not all systems are perfect and it’s true that not all users were fully trained which did cause some issues and led to people complaining. But, as a manager, you need to manage them in order to put them on the right path, to understand that the system is not perfect and needs an assimilation process until it is working. However, after that period of assimilation, today, we have succeeded and have started to work with the new standardized processes. All parts of the organization are working on a single platform which has delivered some great benefits.
All employees are able to access the system to get information in real time and at the same time while all the engineers are also working in digital formats so most of the paper has been removed from Air Europa’s operations. How was this achieved? Using ‘an App for every task approach (figure 7).
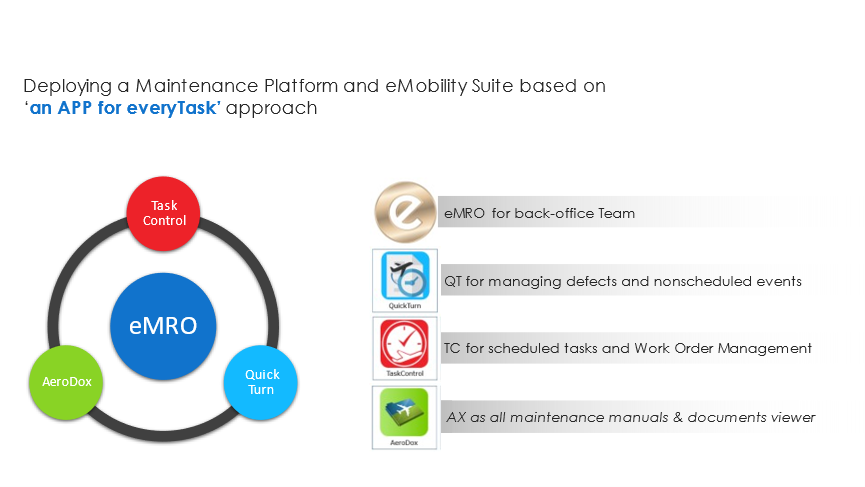
We deployed a maintenance platform, eMRO from Trax, the heart of the system, for the back-office plus every task has its own application. All of the applications were connected/integrated with the system.
LESSONS LEARNED
If we have to summarize what lessons have been learned from this project, there are five that stand out (figure 8).
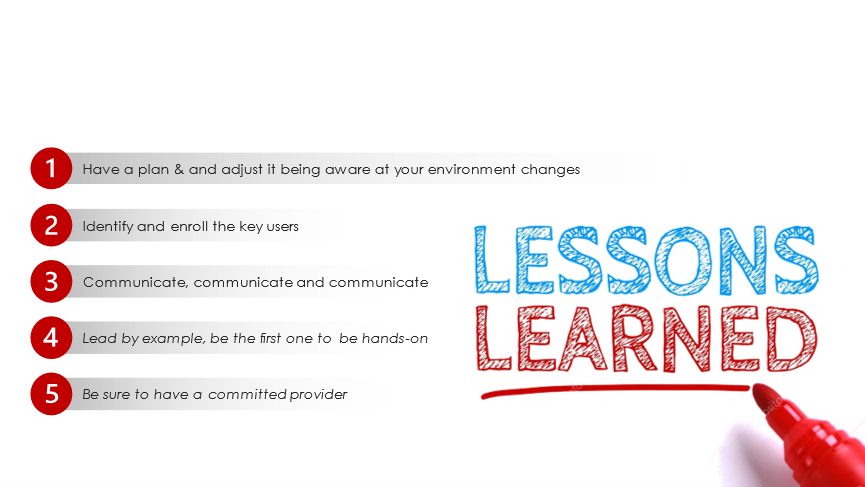
The first one is to have a plan, to be clear where you are going: the plan will need to be adjusted as the environment changes – for instance, Covid was not planned. It is important to identify and enroll the key users. It’s a challenging project and you won’t have all the knowledge necessary to carry it out: you’ll need to involve people in the company with the right experience. Communication is vital and we worked hard on this at Air Europa but we feel we could always further improve. For me, one of the most important lessons has been the need to lead by example, to be the first to be hands on with the new system. And, of course, be sure to have a committed provider; Air Europa had that committed provider in Trax.
PROJECTS RUN IN PARALLEL
During the project, we came across different situations that required us to create or perform side projects that had to be carried out in parallel with the main project. The first one was that Air Europa needed to replace the document management system plus integrate it with the new platform. We were able to migrate nearly 500 gigabytes of records related information and have created more than 200,000 linked documents to the eMRO platform.
Another project of which we are very proud, has been the deployment of a mobility system and application for mechanics and all of this system had to be deployed generating the need to manage a large quantity of devices. We needed control of the devices, application deployments and content updates with smart delivery. Having looked around the market for a solution that would meet our requirements, in the end and in the circumstances of the pandemic, it was decided to create it internally.
We designed and built our own Smart Locker for Air Europa for use at our main bases in Madrid, Barcelona, Gran Canaria, Tenerife and Palma de Mallorca (figure 9).
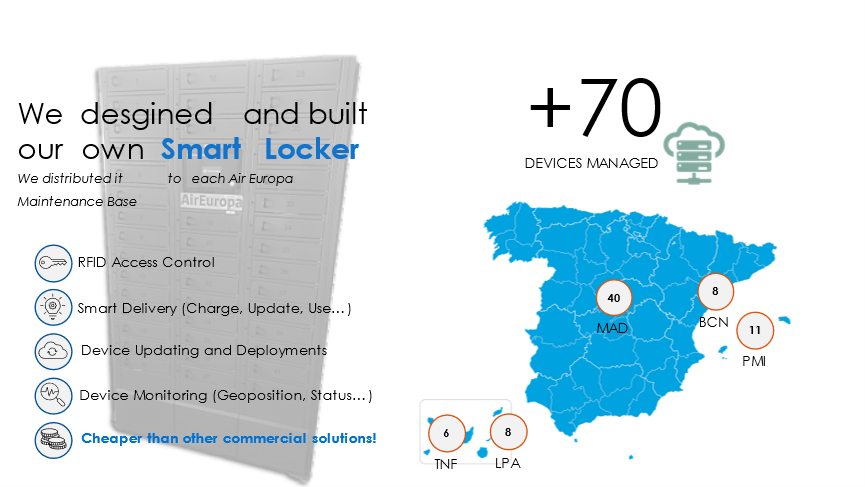
This Smart Locker is able to manage and update the system, identify who has access to the device, prove a smart delivery system, to know whether or not it needs updating, to update while charging and to know time of use. We are also able to quickly update and deploy the content for applications. That is quite important because, if a mechanic is working when a new version of a publication needs to be deployed, that means that, if the mechanic doesn’t have the correct application, he’ll be unable to do the work. We are able to deploy all new versions in less than twenty minutes for all devices in all of our facilities and we are able to monitor all devices; where they are, their status, their charge, the updating; all of which can be transferred into the platform. Plus, the cost has been less that solutions that we found in the market.
Also, we realized the benefit of sharing experiences. At the start of the article, we said that one reason for the article is that we are here to share. We have realized the benefit of sharing experience, problems and doubts not only with providers but also with other customers, like ourselves, that are working with the same system. We share the decisions that help us to solve problems because we have the same restrictions, the same problems, authority requirements… all of us, in the end, work more or less in the same way. So, we decided to create a collaboration group initially to discuss the problems, experiences and solutions; but now there is a collaboration workspace in which members can share their different points of view and understand how each one thinks and solves problems.
It started with Trax customers in Spain but nowadays it is a bigger group (figure 10).
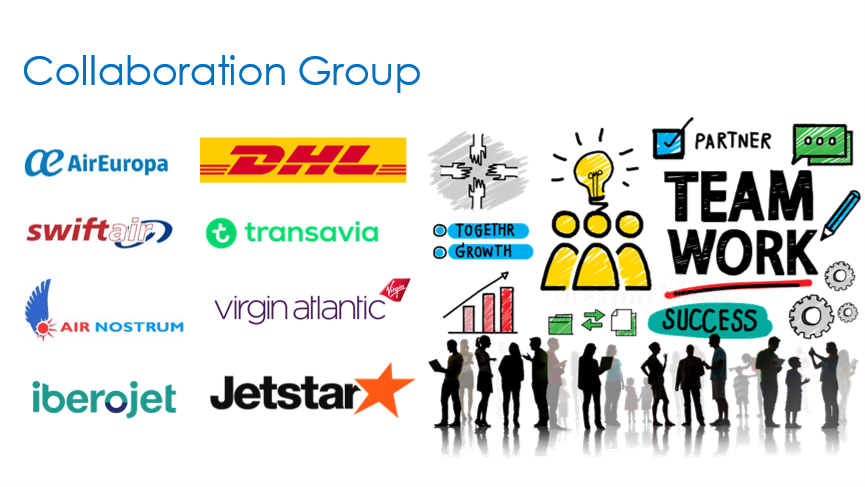
We are very proud of this because we have all learned a lot from other airlines which is to the benefit of us all.
LOOKING TO THE FUTURE – NEXT STEPS
Let’s look at what Air Europa will be doing during the last mile of the digitization process. This is not just a project for maintenance, but also affects the whole organization; many will benefit from it. This last mile has the highest visibility and impact on real daily flight operations. It doesn’t mean that this is the end of the project; it’s just another milestone and, once it has been passed, there will be a new lifecycle. Many scenarios are being considered and Air Europa is performing a lot of testing, but facing new problems in real life operation is a certainty and is part of the cycle. Of course, this was not the priority but even working with the first phase of the project, the focus was already on this last mile
During this phase, we introduced two new apps, one for the Flight Crew and one for the Cabin Crew: even though they were only two applications, it was not an easy task. These two apps will be to complete the whole process of this transformation project. Although new challenges will arise during this last mile, there is the opportunity to co-operate and collaborate with customers, and to share experiences and problems and common solutions. Also, there is strong support from Air Europa’s partner and, at the end, we’ll need to fulfil all the Authority’s requirements that we come across. These working groups generate useful added value.
But, for the project to continue, there will need to be new working groups and that’s not an easy task. We need employees that are eager to share new ideas, to be able to collaborate with each other and sometimes undertake some testing because it can be hard to nail down what’s going on in the Apps or in the integration with the systems. A lot of this has been done during the pandemic having to overcome physical separation distances but we are proud of what has been achieved. Happily, we managed with a great team that delivered good results and are one hundred percent committed to the project.
The digitization process is mind blowing for which we had to be ready to prepare because sometimes these kinds of transformations are not welcome and sometimes they are a bit frustrating when things don’t go as expected.
There are some interesting benefits (figure 11) from which we want to highlight the speeding up of the operation and reducing maintenance transit times, always with safety standards in mind.
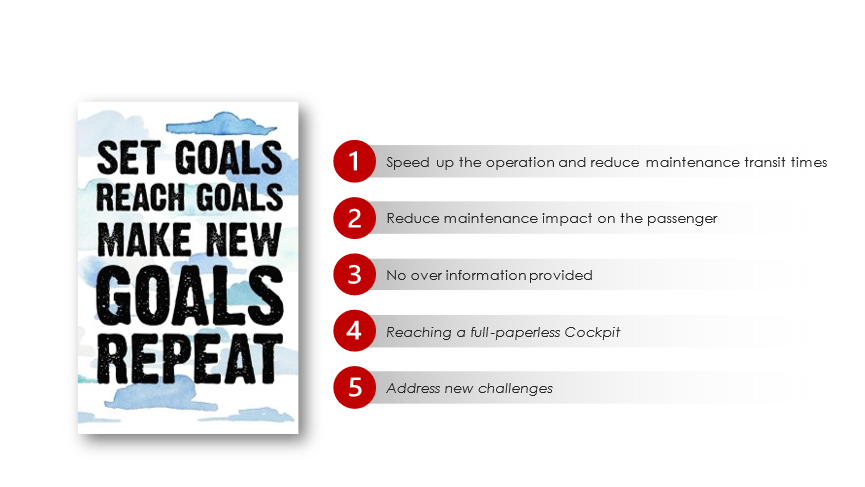
There is also reduced maintenance impact on passengers and no over information is provided. We did share some legacy information on the paper techlog which doesn’t make sense. What does make sense is for information to be updated in a real time platform with access to it as required. Addressing new challenges is also a benefit; it helps to improve processes and offers value to the whole project. And we are getting closer to the idea of a paperless cockpit.
One goal that we have in mind is to keep going and keep focusing on the passengers. For this, we are thinking about how to deliver real-time reports from the systems in the company and take advantage of this information to take action as soon as possible.
As we said before, we have faced new challenges during this project, and some of them have created work on side projects. Sometimes we uncover shortcomings which need to be faced – how to deal with a system failure or a lack of connectivity during an operation. So, it was necessary to build new procedures to deal with those sorts of contingencies that might happen during an operation. In case of a contingency, it is necessary to go back to basics and use the paper system but Air Europa wants to give support to these back-up procedures. For this reason, the IT department with Flight Operations has developed some interfaces to connect ACARS to the back-end of eMRO to fetch all maintenance data that pilots would need to handle a contingency scenario. We can retrieve information, collate it with the facts, such as maintenance checks, due dates and notices to crew. In addition, there are links to Jasper reports which is another way to retrieve this information. Both are powerful tools and we wanted to get the most from them since they add value and give support to the whole ecosystem.
In figure 12, you can see a real test flight.
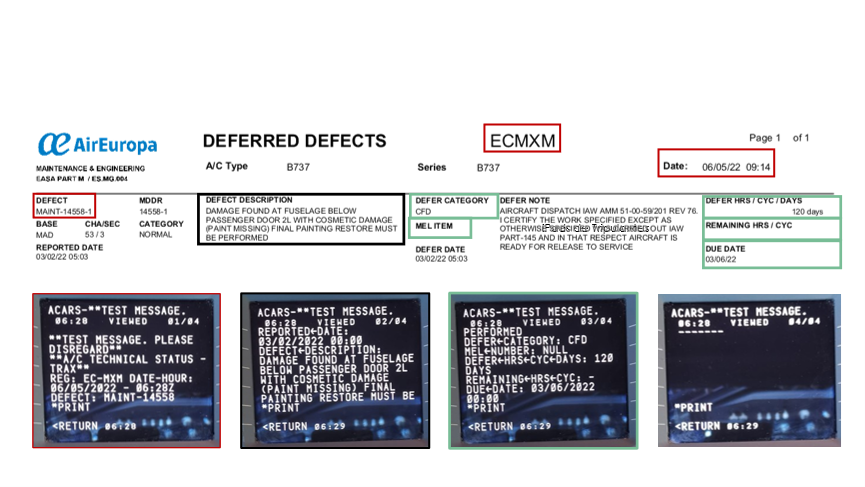
There are some deferred defects and, on the other side of the figure a Jasper report. The Jasper report shows an example of a deferred defect with the minimum information that the pilot would need to dispatch the aircraft and, underneath the Jasper report, some snapshots from the ACARS report with the same information.
To conclude, the results so far. We have begun to test all this in the real environment and the results have been good. It’s a way to detect hidden details that might have been overlooked before. And here, the final key users gain a special relevance with their feedback. We need to detect any possible gaps in our processes, minor gaps with the app, with the integrations. Looking over the work we have done at Air Europa, we are proud of it, we are achieving our goals with minor changes which is normal. We hope this will have been useful for anyone considering embarking on a similar digital transformation and paperless maintenance project.
Contributor’s Details
Francisco De Borja Mas Boned
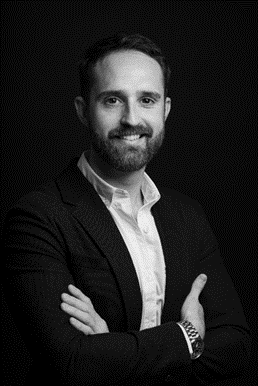
Head of Innovation in Air Europa Maintenance and Project Manager of emro & emobility implementation
Borja is a Telecommunications Engineer who started at Air Europa Maintenance in 2017 as Innovation Manager. In addition to managing innovation projects, he has played a leading role in the implementation of eMRO and eMobility suite (TRAX) as project manager. This project was considered strategic within the company’s digital transformation plan, whose GoLive was in July 2021, marking a major milestone on Air Europa’s Maintenance digitalization roadmap.
Juan Miguel Sánchez García
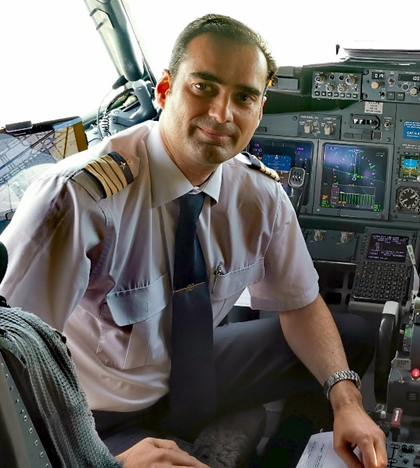
Captain and Line Training Captain, and Engineer in Computer Science
Juan Miguel has been in aviation for over 20 years and is a Captain on the Boeing 737: he was also type rated on Airbus 330 and Embraer 195. He is passionate about hardware and software programming skills due to his academic background as an Engineer in Computer Science and is involved in the digital transformation project in Air Europa to deploy TRAX eMobility.
Air Europa

Headquartered in Mallorca, Air Europa is Spain’s third-largest airline, flying non-stop to more than 60 destinations, including points within Spain as well as international destinations across Europe, Africa, Asia, North America and South America. The fleet of 48 aircraft includes Boeing 787-8 and -9 types as well as, Boeing 737-800, Embraer E195 and ATR72. Maintenance operations include part145 and CAMO.
TRAX
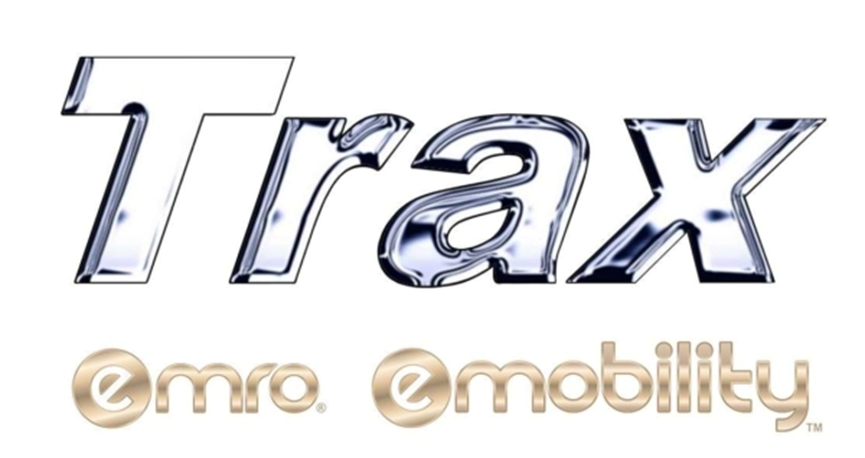
TRAX eMRO is an enterprise software provider of aircraft fleet engineering & maintenance, MRO, planning, compliance and inventory management. The eMobility Suite is truly mobile with offline capability to ensure users can work in Wi-Fi/Cellular dead zones. Organizational capabilities and support solutions include: custom software development, software maintenance, mobile solutions, systems application integration, release upgrade support, SaaS cloud hosting, Project Management & implementation support, user training, business analyst consultation & business process mapping & documentation, gap analysis, data migration, & QA testing.
Comments (0)
There are currently no comments about this article.
To post a comment, please login or subscribe.