Articles
Name | Author | |
---|---|---|
CASE STUDY: Mapping a better solution for Frontier Airlines | Joshua Lee, Senior Manager Technical Programs, Frontier Airlines | View article |
CASE STUDY: Improving efficiency of Wizz Air’s taxi fuel planning | Jaime Romero Waldhorn, Fuel Efficiency Manager at Wizz Air | View article |
CASE STUDY: Silk Way West Airlines embraces digital EFB and EFF solutions | Zahid Sultan Khan, Chief Pilot, Silk Way West | View article |
CASE STUDY: Fueling efficiency: how Azul soared with predictive analytics | Caio Garcia, Captain, Flight Ops Engineering Manager and Fuel Efficiency Manager at Azul Airlines | View article |
CASE STUDY: Engaging pilots in fuel efficiency at Azul Airlines | Caio Garcia, Captain, Flight Ops Engineering Manager and Fuel Efficiency Manager at Azul Airlines | View article |
CASE STUDY: Digital EFB operations at Aerolíneas Argentinas | Captain Ulises Raymundi, Pilot at Aerolíneas Argentinas | View article |
White Paper: Digital Towers and sharing useful information | Andy Taylor, CSO Digital Towers AT NATS | View article |
CASE STUDY: Engaging pilots in fuel efficiency at Azul Airlines
Author: Caio Garcia, Captain, Flight Ops Engineering Manager and Fuel Efficiency Manager at Azul Airlines
Subscribe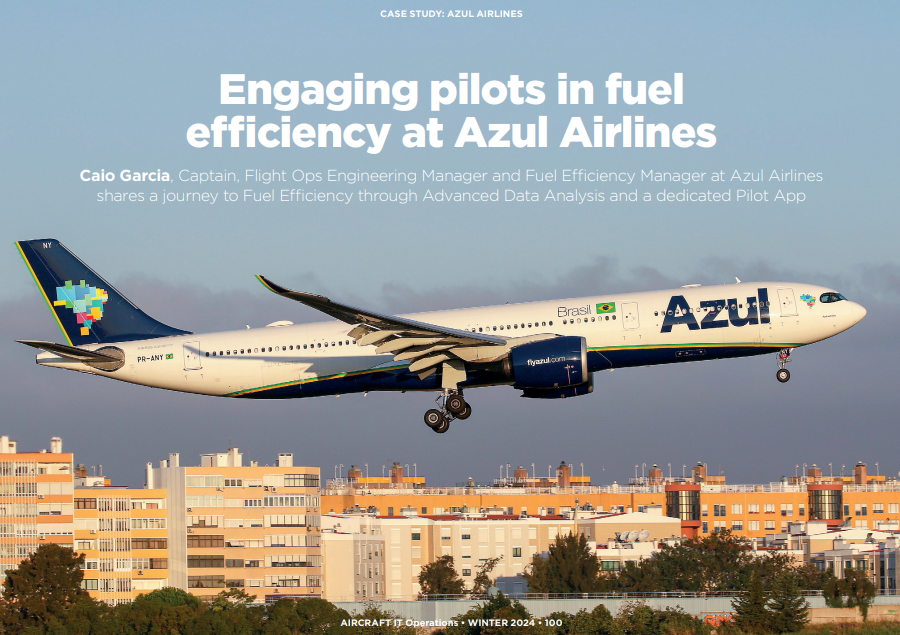
Caio Garcia, Captain, Flight Ops Engineering Manager and Fuel Efficiency Manager at Azul Airlines shares a journey to Fuel Efficiency through Advanced Data Analysis and a dedicated Pilot App.
Before diving into the details of this case study, it’s important to provide some context about the environment in which it applies.
Azul Airlines
Azul Airlines serves approximately 158 destinations, including many smaller airports across Brazil (Figure 1).
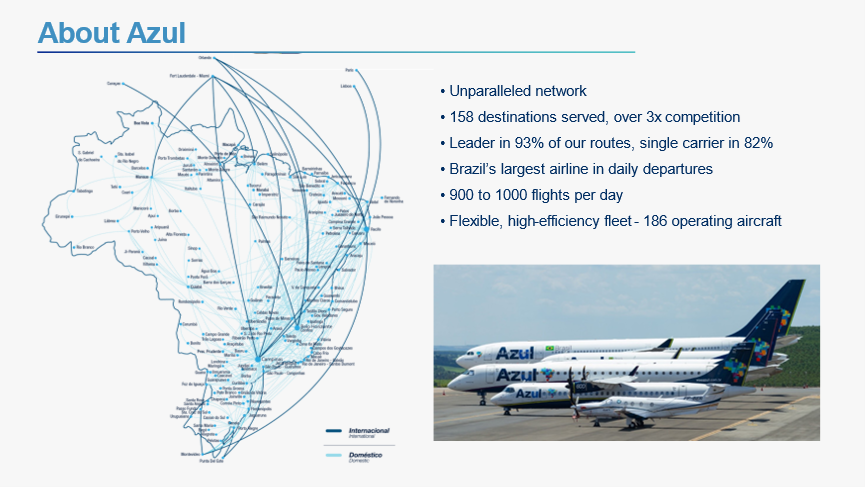
Figure 1
Our fleet consists of 186 aircraft, including Cessna Caravans, ATR 72-600s, Embraer 195 E1/E2, ERJ-190s, Airbus A320/A321neos, A321neos, A330ceos, and A330neos. Additionally, we operate a couple of Pilatus aircraft to transport parts to address any AOG (Aircraft on Ground) situations at remote airports. Operating within the Amazon region presents unique challenges, as parts are often difficult to procure locally. Therefore, the capability to ferry parts and deploy specialized maintenance teams is essential to minimize aircraft downtime in remote locations. We operate approximately 900 to 1,000 flights daily, depending on the season.
A little bit about our partner, OpenAirlines. They have more than 70 airline clients, including about 40 new ones since 2020, especially with the fuel rises post-COVID. It’s a great community and they’re great partners. We particularly appreciate interacting with other airlines in the community and we’re proud of being a part of this community.
SkyBreathe® is a pretty comprehensive solution: there are a lot of advanced computations that go into it as well as advanced analytics plus it offers ease of use which, as you’ll see, is one of the main reasons we selected it. There are also some new things being developed with AI, which we’re going to test in the coming weeks and months with the help of our business partner, Mohi (figure 2).
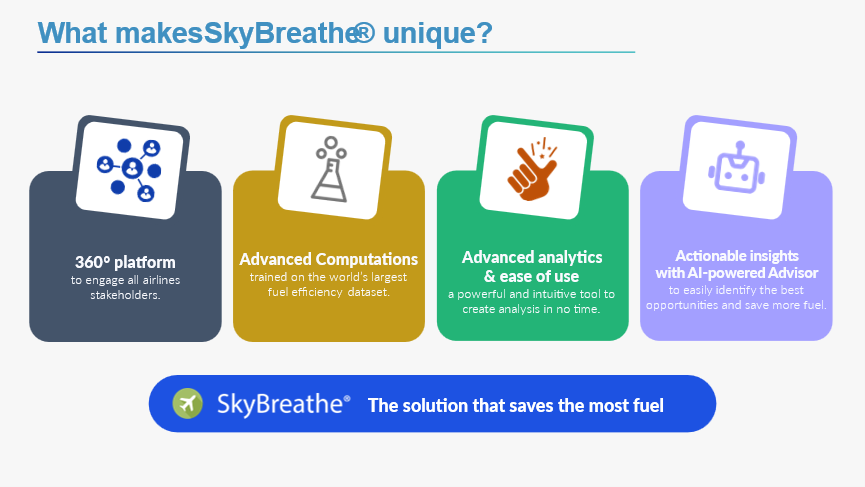
Figure 2
SkyBreathe® is a 360-degree platform which means that it empowers all your teams around fuel efficiency: OCC (Operations Control Center), dispatch, finance department, sustainability team, fuel team, and ops team. This all-in-one platform lets you bring everybody on board and gives you all the tools you need to succeed in your fuel efficiency program. Everyone is connected and gets the same source of information.
FUEL EFFICIENCY AT AZUL AIRLINES
Fuel efficiency at Azul is very much pilot oriented. What we notice is that it doesn’t matter what sort of bells and whistles, what optimization, what kind of good stuff you put in, if the pilot doesn’t follow that or doesn’t fly it well, the savings won’t be very high. It’s like driving your car; you might do everything you want, but if you step on the gas too much, you’re going to waste fuel.
One of our key successes is implementing ‘APU Zero,’ where we operate without using the Auxiliary Power Unit (APU) by plugging into external power instead. Additionally, our Standard Operating Procedures (SOPs) include practices such as constant descent angles, reduced acceleration altitudes, single-engine taxi operations (both in and out), cross-bleed starts, reduced flap usage, intersection departures, route optimization, and rolling takeoffs.
We’ve also partnered with the Operations Control Center (OCC) to ensure the most economic aircraft are assigned to routes where they’ll be better utilized. This involves deploying aircraft with minimal degradation on longer flights and leveraging strategies like cost index adjustments, route optimization, tankering, and reclearance planning. On the air traffic control (ATC) front, we collaborate with ATC authorities to make approaches and departures as fuel-efficient as possible, particularly at our main hubs. We utilize SkyBreathe® as well to support these efforts. Finally, our Tech Ops team plays a critical role. They ensure operational efficiency by facilitating APU Zero, performing engine washes, and maintaining the aircraft to keep them AS sleek and as fuel-efficient as possible.
Before we had SkyBreathe®, everything was set up into a database (figure 3).
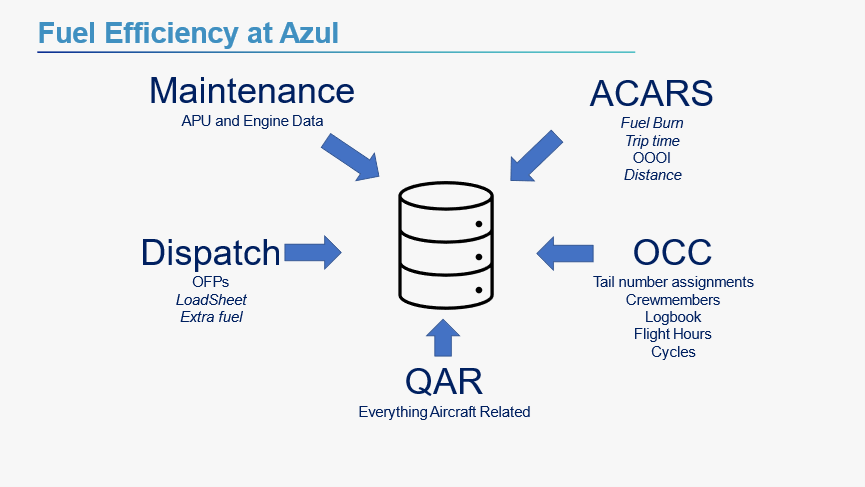
Figure 3
Inputs to the database come from various sources: Maintenance provides APU and engine data; Dispatch contributes operational flight plans (OFPs), load sheets, and extra fuel details; ACARS supplies fuel-burn metrics, trip times, OOOI (Out, Off, On, In) times, and distances; and OCC adds tail number assignments, crew information, logbook entries, flight hours, and cycles. The goal is to ensure that the flight data we’re analyzing corresponds to the actual flight in question. This requires proper synchronization, seamless communication between systems, and high-quality data.
And finally, there’s QAR (Quick Access Recorder) data, where things get more complex.
QAR (Quick Access Recorder) data can be especially challenging to manage, particularly in a multi-fleet scenario. Take the ATR, for example—it’s a relatively straightforward aircraft in terms of data handling. The E1s (first-generation Embraer jets) are also quite manageable, but the E2s present significant challenges. Being a newer aircraft, Embraer has packed a wealth of data into the E2s. However, the complexity of processing this data and the design of the system create unique difficulties for operators. Setting-up the E2 can also be demanding initially.
The A320s have their quirks but are generally easy to work with. Then there are the A330s, which add their own complexities. The overarching challenge is ensuring all these systems ‘talk’ to each other seamlessly within a unified platform.
For example, consider monitoring a single parameter – whether the parking brake is engaged. With ATR data, we receive a lever assignment; with Airbus, we get brake pressure; Embraer uses an indicator light; and the A330 combines elements from different sources. Harmonizing this data across a multi-type fleet to create a consistent and fair monitoring framework is incredibly challenging.
This complexity has shifted our team’s focus from analysis to programming, as significant effort is spent on bridging these data gaps. Unfortunately, this has led to IT frustrations, with valuable brainpower being diverted to tasks outside our core business objectives.
We needed a tool that required minimal development effort from our team and offered a quick, intuitive interface. This was especially important for scenarios where we’re presenting to C-level managers or high-level leadership. In such cases, we often need to generate a study quickly to validate that we’re on the right track, particularly when leadership is scrutinizing alignment or questioning key assumptions. SkyBreathe® emerged as the tool that met these needs, enabling us to produce studies on the spot with remarkable efficiency. It also supports increased pilot engagement with fuel efficiency initiatives.
SkyBreathe® has proven highly effective in facilitating new studies due to its ease of use. It allows us to validate concepts quickly before committing to deeper analysis. Additionally, it provides accountable managers and teams – such as fleet or dispatch managers, whose core focus isn’t coding – with actionable insights through user-friendly panels. These managers can independently build and review dashboards, while our team focuses on cross-checking and refining as needed. This functionality has been invaluable in reducing bottlenecks and improving overall workflow.
A critical priority for us has been improving the quality of feedback provided to pilots. SkyBreathe® supports this with features like SkyBreathe®MyFuelCoach, which has been a game-changer for pilot engagement, along with advanced analytics (see figure 4). These tools empower pilots and other stakeholders to make more informed decisions, enhancing fuel efficiency across the board.
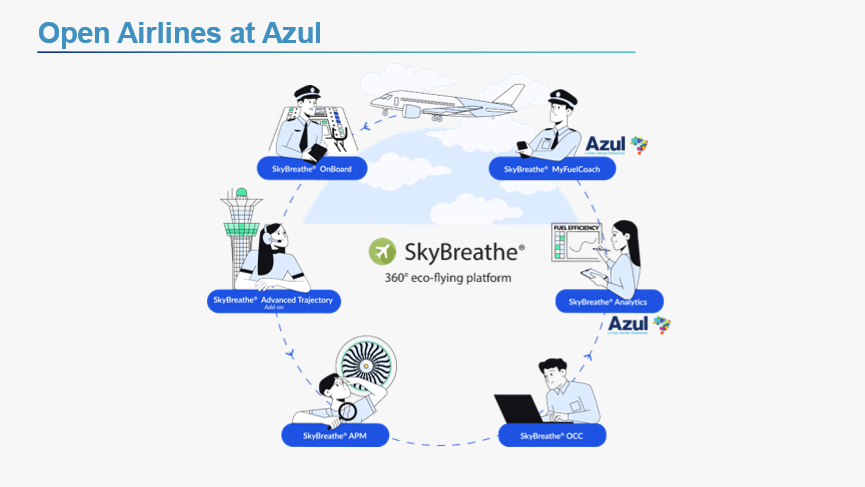
Figure 4
SkyBreathe® 360° platform includes SkyBreathe® OCC, SkyBreathe® NewGen APM, SkyBreathe® Advanced Trajectory, SkyBreathe® OnBoard, but our main focus is SkyBreathe® Analytics and SkyBreathe®MyFuelCoach. It’s a pretty comprehensive tool for whatever state your airline is in terms of experience.
IMPLEMENTATION TIMELINE
We signed a contract with OpenAirlines in December 2022 (figure 5) and began the huge data transfer in January 2023.
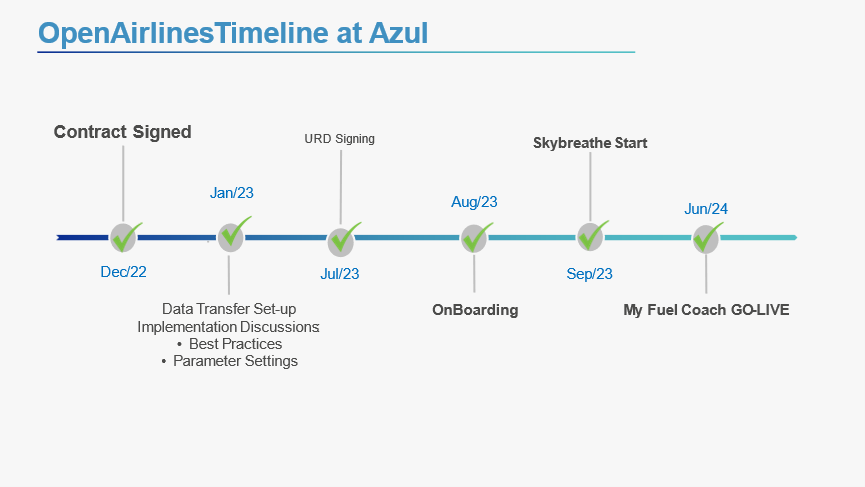
Figure 5
By July, once we had finalized and signed off on the URD (User Requirements Document), our benchmark for measuring best practices, we began the onboarding process about a month later. After ensuring everything was properly set up, we officially started using SkyBreathe®. This marked the beginning of the heavy lifting: aligning data from all fleets and ensuring that historical data was consistent with the outputs from SkyBreathe®. Once we had confidence in the system’s reliability and accuracy, we launched SkyBreathe®MyFuelCoach, a project in its own right.
Our initial focus was on ensuring SkyBreathe®’s reliability. Transitioning from our in-house solution, which had been in use for five or six years, required careful planning and execution. Offboarding the previous in-house system and fully adopting SkyBreathe® was a significant undertaking. To ensure a smooth transition, we concentrated on building confidence across key teams. This included the fuel team, leadership (pilot, OCC, and general operations), and Maintenance, particularly because of their involvement with initiatives like APU Zero. Collaboration with these groups ensured they were comfortable with the tool and its capabilities. We also took a phased approach to transitioning between our legacy data and SkyBreathe®, gradually implementing best practices for SkyBreathe®MyFuelCoach.
SkyBreathe®MyFuelCoach was one of the primary reasons we chose SkyBreathe®, as it played a crucial role in achieving our goals. Figure 6 outlines the timeline we followed for its implementation.
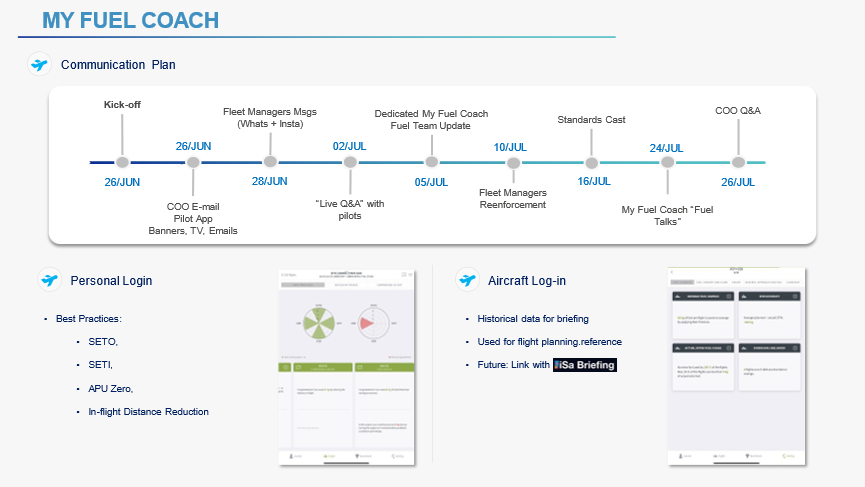
Figure 6
The rollout began in June 2024 with a comprehensive communication plan that extended through July – a full month of consistent messaging from leadership. This included email updates, Q&A sessions, and presentations aimed at engaging everyone and ensuring clarity on how the tool works. We focused on getting pilots involved, encouraging them to ask questions, and addressing any concerns. Our priority was to ensure there were no outstanding questions by the time the tool was rolled out. We emphasized that the tool’s sole purpose was to manage and optimize fuel usage, not to monitor or penalize individuals.
Concerns about data usage often arise, particularly from unions. However, this was mitigated by an agreement established back in 2016 or 2017 regarding data usage for fuel efficiency. When we introduced SkyBreathe®MyFuelCoach and SkyBreathe® Analytics, we reiterated that the same data source was being used, consistent with the previous agreement. As a result, union acceptance was relatively straightforward. The involvement of the Safety department, particularly the FDM (Flight Data Monitoring) team, was instrumental in ensuring a smooth rollout. Their participation reinforced trust and transparency throughout the process.
Pilots have access to two distinct interfaces (see figure 7). The first is a mobile app available on iPads and iPhones, where pilots can review their individual flights. The second interface is integrated onboard the aircraft, providing real-time access to relevant data.
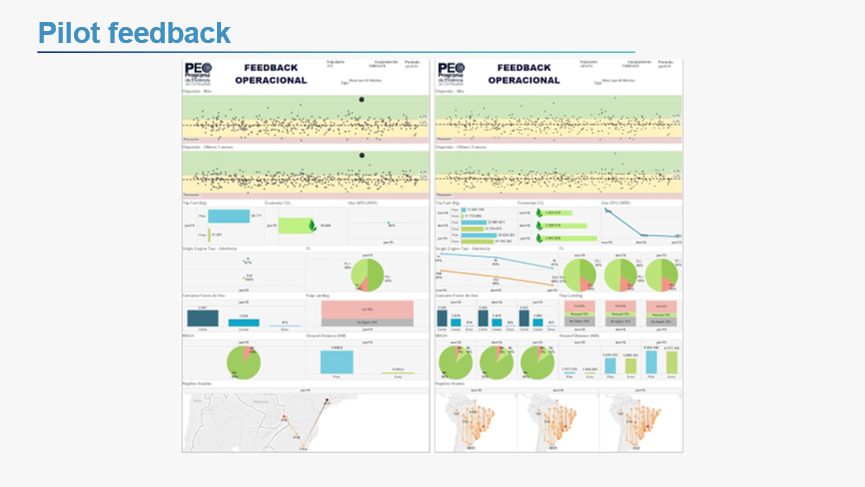
Figure 7
The personal login (shown on the left) provides access to four key best practices: single-engine taxi-out/taxi-in, APU zero, in-flight distance reduction, and other familiar metrics. These were easy for pilots to understand and measure, as they were already part of their routine. We initially rolled out these four best practices to help pilots build confidence in the tool, demonstrating that it supports both their performance and the airline’s objectives. The goal was to engage pilots and get them comfortable with the tool, so, moving forward, we could gradually introduce additional best practices to maintain interest and engagement, especially on the aircraft.
On the aircraft’s EFB (Electronic Flight Bag), we offer a generic login that allows pilots – let’s say, those flying to France for the first time in winter – to view statistical fuel data for that specific flight. For example, when flying into Orly, they can see how much extra fuel other aircraft have used, how many have diverted, the actual flight duration, and how the planned versus executed fuel use compares. This data helps ensure that our fuel calculations in the OFP (Operational Flight Plan) are as precise as possible, minimizing both excess and insufficient fuel.
Looking back at Figure 3, you can see what we had before – the operational feedback. At the top of Figure 7, you can see a comparison between the individual pilot’s fuel efficiency and the rest of the group. Below this, we provide detailed metrics such as trip fuel, fuel saved, fuel wasted, CO2 emissions, GPU usage, single-engine taxi-out adherence, flight level adherence, and fuel consumption per flight phase. On the right side, a timeline comparison shows how the pilot’s fuel efficiency has evolved over months (November, December, and January).
While this data was useful, it didn’t provide specific insights for pilots on how to improve. For example, while a pilot might see that their month was more efficient than the last, they wouldn’t know exactly where to focus their efforts to improve further. Pilots want details like: “Where can I improve my single-engine taxi-out? Is it a particular airport, runway, or day?” This type of analysis was difficult to achieve with the previous system.
That’s where SkyBreathe® and SkyBreathe®MyFuelCoach made a significant difference. With SkyBreathe®MyFuelCoach, we can provide pilots with precise feedback on where they saved fuel relative to the OFP, broken down by phase of flight (as shown in Figure 8).
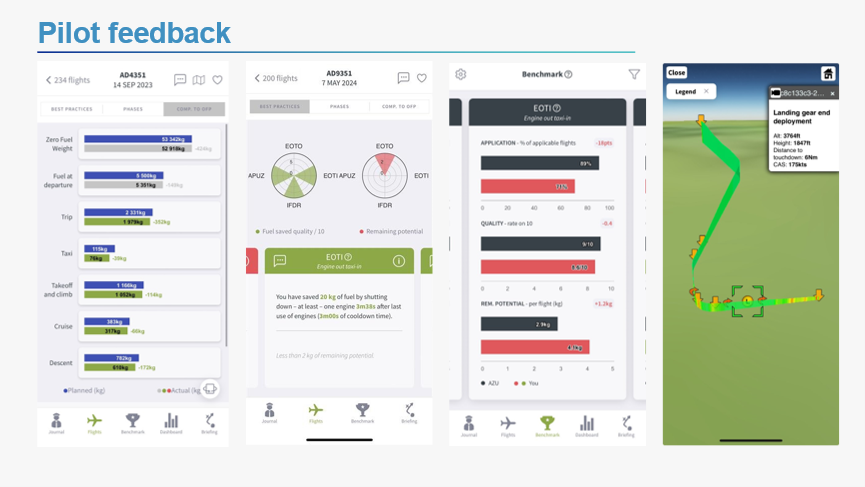
Figure 8
With these metrics, it’s much easier for pilots to digest information on a per-flight basis, seeing where they’ve saved fuel, performed well, or where they need improvement. For instance, with engine-out taxi-in, the data shows that the pilot saved 20 kilos by shutting down one engine three minutes before the last use of the engine. This allows the pilot to understand exactly where they can take action on their next flight or at another location. Additionally, there’s a comparison of the pilot’s engine-out taxi-in performance relative to the rest of the group. This helps the pilot see how they measure up in terms of fuel efficiency for this practice.
One of the most popular features, however, is the map that visually represents how the pilot configured the aircraft. This is similar to what you would see in a Flight Operations Quality Assurance (FOQA) system, but with the added benefit of showing the pilot areas where they could have configured the aircraft more efficiently.
We encourage instructors and training captains to use this visual tool in their training sessions. When they’re working with a pilot over the course of a month, they can walk them through the app to highlight areas for improvement. This approach helps pilots apply the data to their next flight, making training more actionable and memorable by grounding it in the details of past flights. We also collaborate closely with ATC (Air Traffic Control). Our ATC team works with different authorities and regions to discuss potential improvements for approaches and departures. For example, Figure 9 shows how we approached the VCP authority at our main hub, pointing out that the black line represents their published procedure.
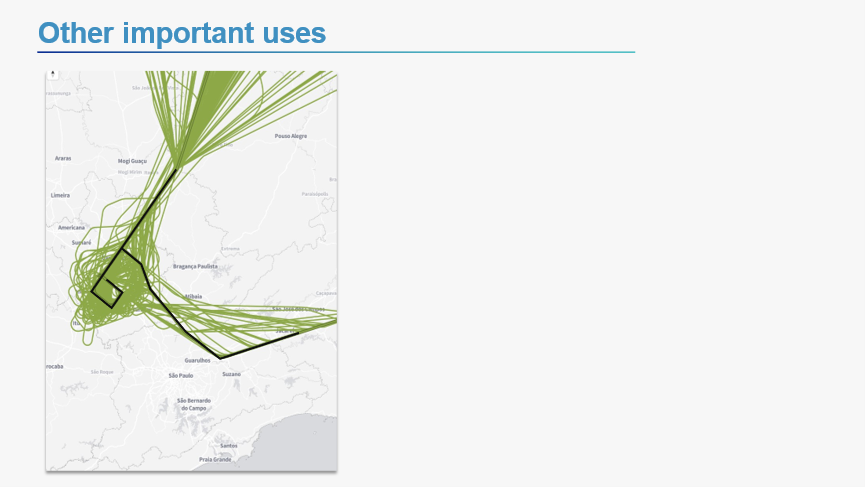
Figure 9
The green line represents the route we are being asked to fly, but in many cases, it doesn’t align with the published approach. On a daily basis, we’re not even following the planned approach. We engage with ATC to discuss how we can make the flight paths more efficient, ultimately improving the overall efficiency of the flights. We demonstrate the potential savings in fuel and CO2 emissions, using SkyBreathe®‘s data to make a compelling case for more fuel-efficient routes. By involving ATC with our fuel efficiency metrics, we foster a collaborative approach to optimizing air traffic control procedures.
We also work closely with dispatch to improve zero fuel weight and center of gravity (CG) precision. We’ve developed some innovative solutions, particularly with APU and hotel mode zero. For those unfamiliar with ATR operations, hotel mode zero refers to a process where the ATR engine is kept running with the propeller locked, effectively serving as an APU (Auxiliary Power Unit). We’re actively helping to enhance this process for ATR operations.
Looking ahead, we’re focusing on initiatives such as flight level adherence monitoring. This will ensure pilots are consistently flying at the optimal flight level or, at the very least, adhering to what was specified in the OFP. These are just a few of the exciting initiatives we’re planning with SkyBreathe® moving forward.
WRAP-UP
Switching from an in-house solution has freed up more time for us to focus on analysis rather than development. This shift means our teams are now doing less programming and more of the important work – looking at where we can save fuel, improving efficiency, finding better ways to communicate, and expanding the scope of our best practices. There were many things we couldn’t address before due to time constraints, but now, with SkyBreathe®, we have the ability to develop those solutions.
Managers, especially fleet managers, appreciate this shift. They now have direct access to the tool, allowing them to manage fuel usage more effectively and explore new possibilities on their own. This empowerment has been a key benefit. Perhaps most importantly, we’ve seen a significant increase in pilot buy-in and self-development. Alongside other initiatives – such as Lido, our OFP provider, OptiClimb, SITA, and other tools – we’re witnessing more efficient flight planning and better management of extra fuel. One of the most notable improvements is a consistent reduction in extra fuel use, which has dropped by about one to two percent each month. This is especially important in Brazil, where fuel is among the most expensive in the world, second only to a few countries like India. Fuel costs represent 50 to 60 percent of our operational expenses, so this reduction is a major saving. We are all deeply focused on improving fuel efficiency, and SkyBreathe® has been instrumental in helping us implement these changes smoothly. I hope this article serves as a helpful resource for anyone considering a similar development in their own operations.
Comments (0)
There are currently no comments about this article.
To post a comment, please login or subscribe.