Articles
Name | Author | |
---|---|---|
CASE STUDY: Etihad Airways bring cockpit and cabin logs together | Masoud Al-Alawi, Manager Aircraft and Digital Operations, Etihad Airways | View article |
CASE STUDY: Digitalizing the warehouse at Finnair and DHL Supply Chain | Otto-Wilhelm Orumaa, Operations Excellence Manager, Finnair | View article |
CASE STUDY: A Better Documentation Solution for Cebu Pacific | Hazel B. Ocampo, Manager – Configuration Management – EFM at Cebu Pacific Air | View article |
CASE STUDY: Joramco’s new system offers a better way of working | Shakespear Nyamande, Vice President of Planning at Joramco | View article |
CASE STUDY: Etihad Airways bring cockpit and cabin logs together
Author: Masoud Al-Alawi, Manager Aircraft and Digital Operations, Etihad Airways
Subscribe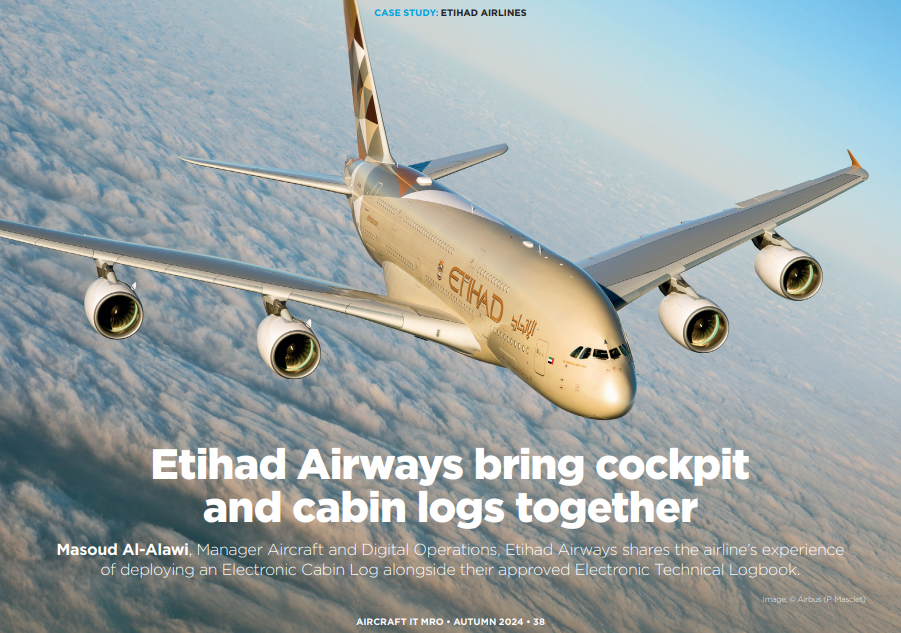
Masoud Al-Alawi, Manager Aircraft and Digital Operations, Etihad Airways shares the airline’s experience of integrating the eCabinLog8 with the eTechLog8
In this article I’m going to share our experience at Etihad with the electronic Technical Log and, in particular, the eCabinLog8 implementation and integration. We’ll look at the project overview, challenges that we encountered when we deployed the eCabinLog8 and what are the benefits that we have gained. Finally, I’m going to share what we are planning to do in the next 12 months or so. But, before any of that let me introduce you to Etihad Airways.
ETIHAD AIRWAYS
A relatively young airline compared with other regional operators in the Middle East, Etihad Airways was established in 2003. We operate out of Abu Dhabi from the recently re-named Zayed International Airport (figure 1).
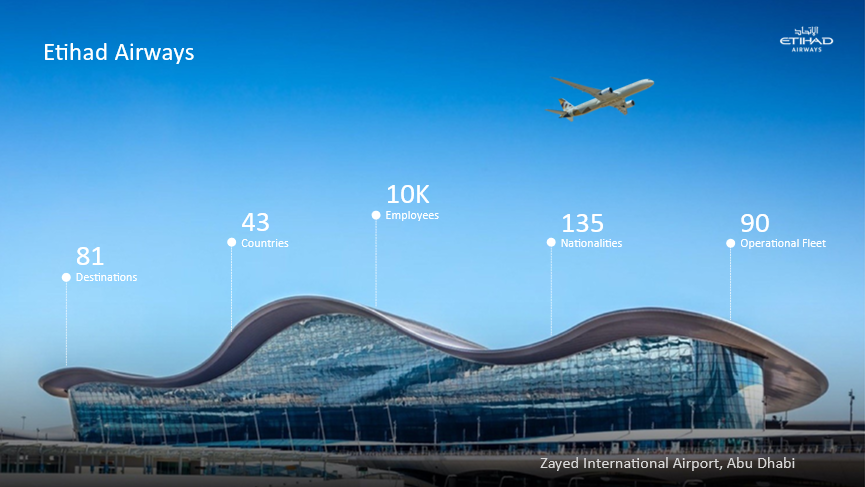
Figure 1
As you can see, it’s a beautiful structure: state of the art modern facilities with 65 gates and capacity to handle more than 30 million passengers a year. I saw the ‘Mission Impossible’ movie before going live to see the terminal and the movie certainly portrays the full magnificence of this terminal. It is in line with Etihad’s own ambitious growth plan.
The plan is to double the fleet and be serving more than 130 destinations by the end of the decade, and we’re getting there. Currently, Etihad flies to 81 destinations in 43 countries and has more than 10,000 employees from all over the globe – there are 135 nationalities in the workforce. The current operational fleet, at the time of writing, stood at around 90 aircraft of various types and models. To give some scale to our ambition, we inducted 16 aircraft in the past year with the plan to induct a further 23-25 aircraft by the end of 2025; so we feel that we’ve made a very good start.
ETIHAD’S DIGITALIZATION PROJECT
As part of this growth plan, from a technical front/point of view, we embarked on a digital transformation program a couple of years ago (figure 2.1).
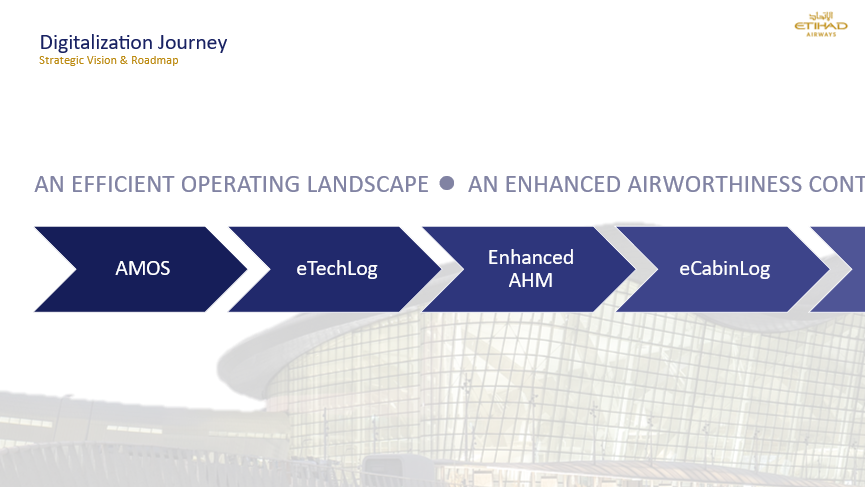
Figure 2.1
We started by consolidating all of our aircraft into AMOS and leveraging the capabilities of AMOS in streamlining our processes. At the same time, we embarked on implementing the eTechLog8 and completed that project in 2023 with the implementation of the eCabinLog8. There are a number of other initiatives that we have been undertaking and deploying. That journey is still ongoing, we continue to follow the roadmap (figure 2.2).
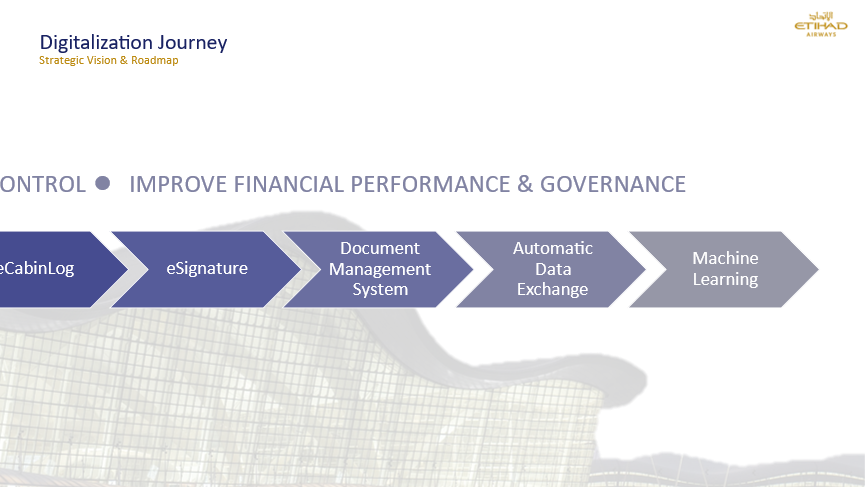
Figure 2.2
We’re planning to implement the eSignature this year (2024) and that will mark a significant leap towards a paperless environment. Likewise, we are also consolidating all of our documents and data into a digital platform that will allow our engineers to have access to the data they need and be able to access it anywhere and anytime using any of the devices that they have. That flexibility is what we are aiming to achieve by consolidating all the documents into one platform.
Something that we have started and that remains ongoing is our collaboration with various vendors on how to make data exchanges which we’ve have done with Boeing parts exchange. We have completed that with our reliability data; we also established that connection with one of the engine OEMs. That is an ongoing discussion with a number of vendors to enable our systems to start talking to each other and to exchange data. As with every other airline, we are all looking at machine learning models to see how we can increase our performance using artificial intelligence and Etihad is no different. We are working in collaboration with a local university which specializes in artificial intelligence and we are trying to come up with models that we can then incorporate into our processes and increase our performance.
THE eTechLog8
Now, to the main topics of this case study, the eCabinLog8 and eTechLog8 (figure 3).
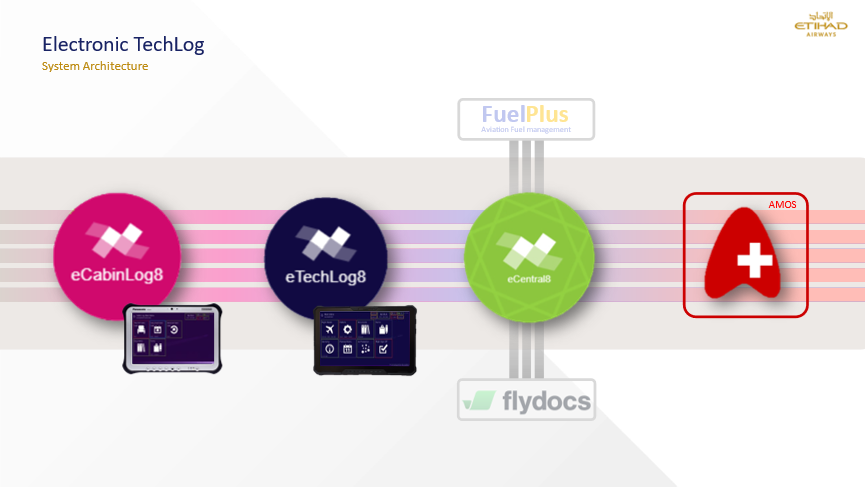
Figure 3
The figure shows what is currently installed at Etihad. There are two devices that are installed on board the aircraft; one device with the eTechLog88 application and the other device with the eCabinLog88 application. These two devices talk to each other through a Peer-to-Peer connection using Wi-Fi hotspots. All of that data goes into eCentral8 which is the management system managing integrations and the various administrative functions that we have. From there we have currently integrated all the defects, flight logs and flight data to AMOS as well as our technical records system; all the TLPs (Technical Log Pages) go automatically into flydocs. We are currently in the final phases of integrating our fuel management system into the ALB and that will increase the data integration between these two systems. But, how did we get here? (Figure 4).
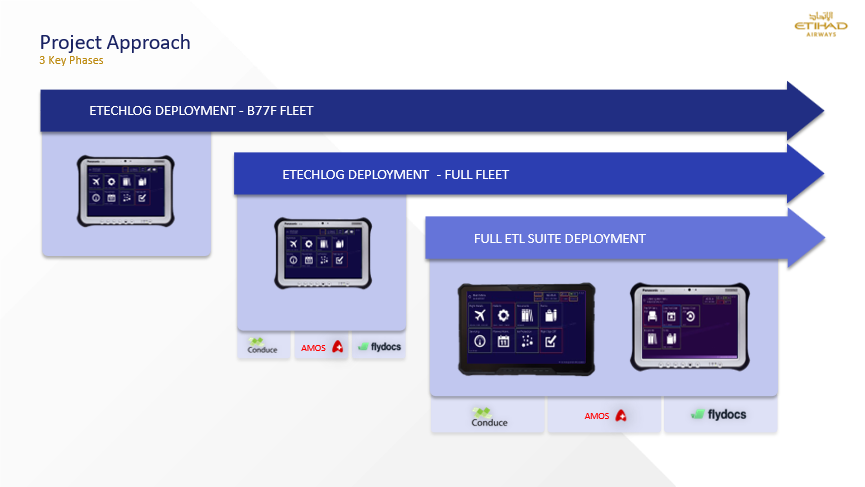
Figure 4
We started this project in late 2019 and then Covid hit but we decided that we might as well just continue with whatever aircraft were still flying, which were the freighters, and we divided the project into three phases. The first phase was just to deploy a simple ‘paper to electronic device’ replacement leaving everything downstream of that almost unchanged. Then, gradually, as the aircraft and fleets resumed flying, we started to roll-out the system to the other fleets but, most importantly, that was when we also activated the integration and really started reaping the benefits of the new system. Finally, last year, to complete the project, we deployed the eCabinLog8. You will see that in the last deployment there were two types of devices which I’ll explain further below.
On reflection, I think that we might have done better; we could have deployed the whole system in much less than three years but, because of Covid and so many other issues with which readers will be familiar, having faced and gone through the issues of Covid, we decided on those three phases and, from start to finish, it took us about three years to complete the transition from paper to electronic solutions (figure 5).
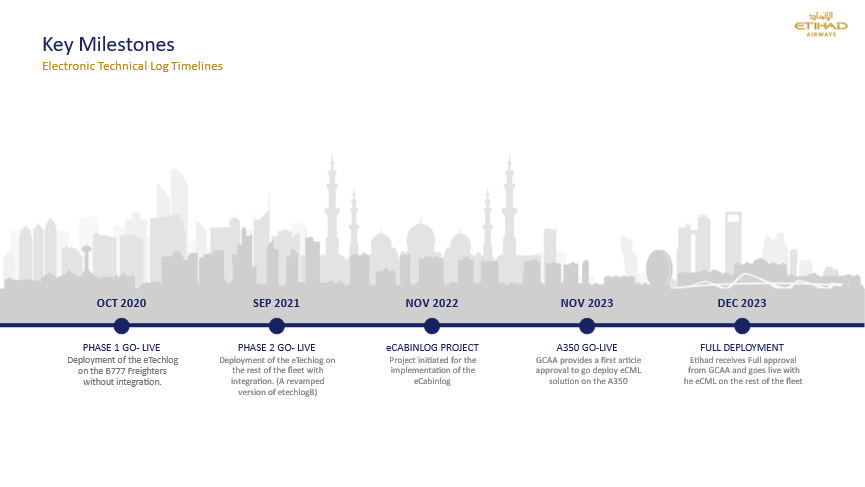
Figure 5
Within that, it took a little bit over a year for the eCabinLog8 implementation.
PROJECT MANAGEMENT
This section will look primarily at the eCabinLog8 implementation (figure 6) but the process is more or less the same as how we did the eTechLog8 implementation.
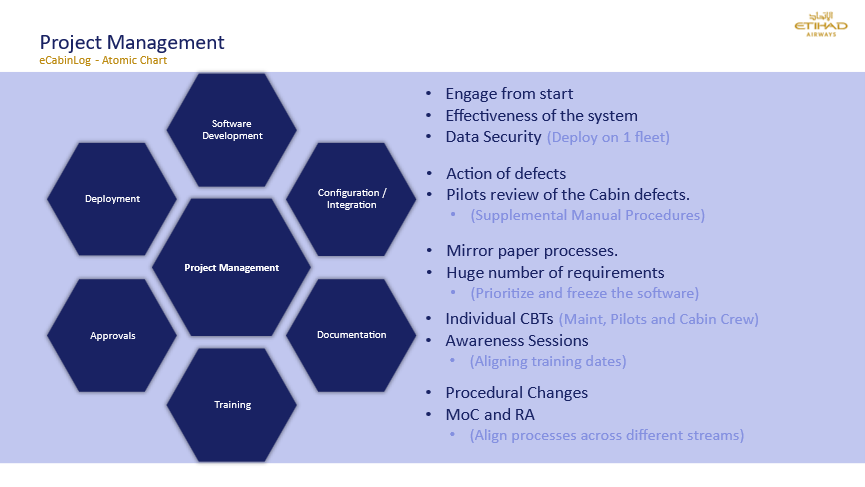
Figure 6
We divided the project into several areas and had a manager nominated to run those areas. When we started with the eCabinLog8, we had a mandate to go-live by 1 November 2023, that was a date that we could not change. But then we also had our own requirements that we posed to Conduce. One was that we wanted all of the cabin defects to be integrated to the MIS (Maintenance Information System) system regardless of whether they were safety or non-safety related defects. That was because we put a lot of emphasis on our cabin and we wanted to have better control and management of all the cabin defects in the MIS system.
The next objective that we gave Conduce was that we wanted to use two devices to simultaneously action defects. That was a very big challenge for Conduce but they accepted that challenge and came up with several iterations while, at the same time, we kept adding more requirements until, a couple of months later, they asked us to list all of our requirements so that they could work on something concrete and consistent. In light of that, my advice to anybody who is undertaking a similar project is that it is sensible to have all of your requirements listed well in advance of the project and, most importantly, is really good to ensure that those requirements are understood by the vendor.
In figure 4 you saw the two devices that we used when the full project was deployed. One of the challenges that we faced on implementation of the eCabinLog8 was adding the second device into the mix. We had Panasonic devices for the eTechLog8, which was working fine but, unfortunately, we were not able to get those devices from Conduce and Conduce after some testing advised us to go with the second device. When you get a second and newer device you start to question whether you’re going to deploy that for the eCabinLog8, deploy it on the eTechLog8, are you going to deploy two Dell devices across one fleet and Panasonics across another fleet? These were some of the challenges that we had to address in order to understand exactly what would be the impact downstream once we deployed the eCabinLog8.
And, again, because we had told Conduce that we wanted to have simultaneous actioning of defects in both of the devices, there were certain areas where we could not trust the system to provide enough certainty and in discussions with the vendor and the stakeholders, we than decided to have additional certainly through manual procedures that we had put in place.
Another area was documentation. In any project, documentation is one of those boring tasks but that has to be done. Because we were adding cabin crew procedures, flight crew procedures and maintenance procedures all in one mix, we needed to ensure that we had everyone aligned with what they needed to do and that there were no ambiguous procedures between other departments. Under documentation we had the MOC (Management of Change/Means of Compliance) and Risk Assessment and the way in which we approached this was that we created one management of change process and then each stakeholder – the pilots, the cabin crew, Maintenance, CAMO – all created their own risk assessments surrounding the implementation of this process.
Training was another of the areas that we had to look into. It might seem to be one of the easiest ones, you just create the training material and deploy it but, at Etihad, we made it a little more challenging. We created three different CBT (Computer Based Training) programs for the stakeholders – one for Maintenance, one for cabin crew and one for the pilots – and on top of that we had numerous awareness sessions raising awareness of what we were deploying, especially for the cabin crew who were getting this system for the first time, and for the outstations.
Approvals was another of the challenges that we had to go through but the good thing here was that we engaged with our authorities very early at the beginning of the project; so, we understood the concerns they had and their expectations. Our authorities were particularly interested in the training, especially the outstation training. They wanted us to ensure that data is secured and that its integrity is not breached and we had to work with Conduce to take these devices through several penetration tests during which some vulnerabilities were highlighted which were dealt with and those test results were part of the supporting documents that we sent for our regulatory approval.
Lastly, on the approvals, they wanted us to monitor the effectiveness of the Cabin Log. This was the challenge: we had the eTechLog8 that was a live and running system. eCabinLog8 is a companion to the eTechLog8 so we could not run trials outside of the production: we had to deploy it in production and then run the monitoring to understand and identify any areas that we wanted to change, which was a good thing. We were able to identify a lot of software glitches that Conduce immediately patched but more than that, we also identified some issues on the new hardware, we identified some training gaps and enforced the awareness sessions a little more proactively to ensure that people fully understood the change.
Lastly came the deployment. We were given a month to deploy and, unfortunately, we picked a month in the peak season during December which was when we rolled out the complete Cabin log to the rest of the fleets. How we managed to do that was that we got a dedicated team from the Part145 who were removed from their rosters and were solely dedicated to just deploying the eCabinLog8. We managed to deploy four or five aircraft every day and 1,500 to 1,600 cabin defects were transferred from paper to the eCabinLog8.
ENGAGEMENTS
There are no projects that are without some fond memories.
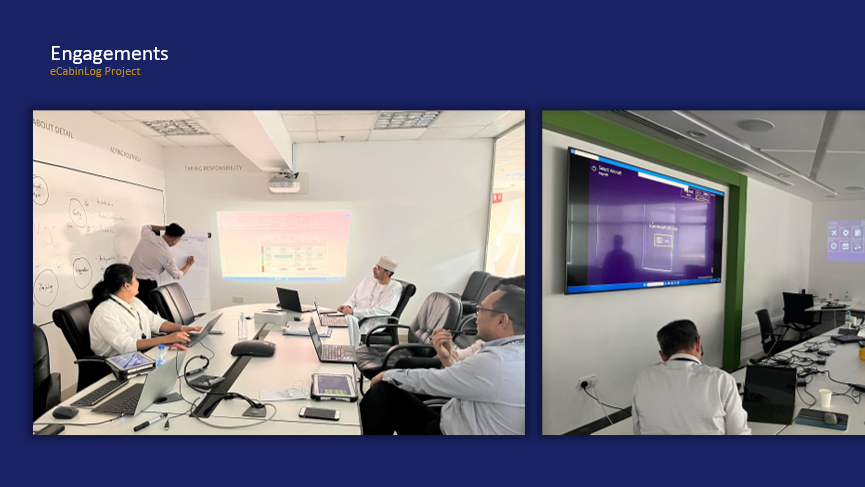
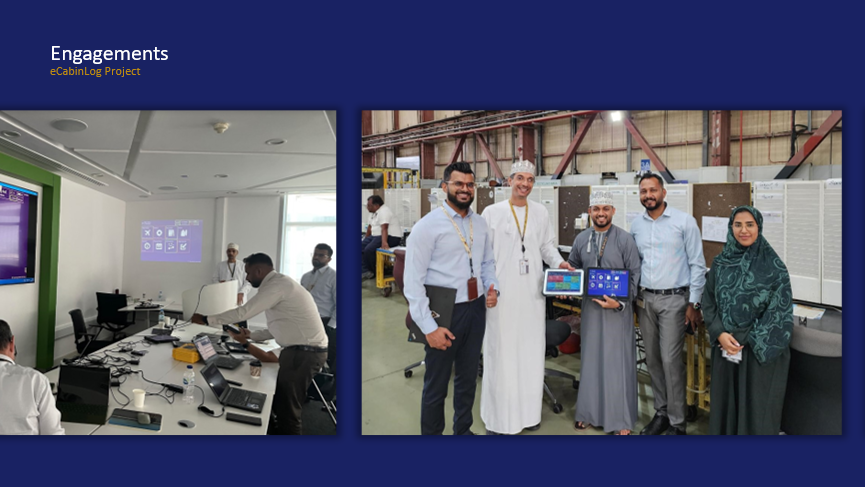
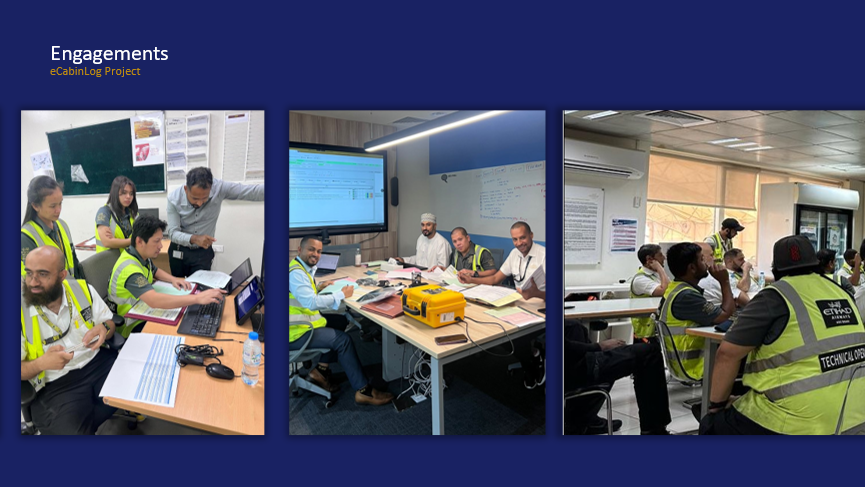
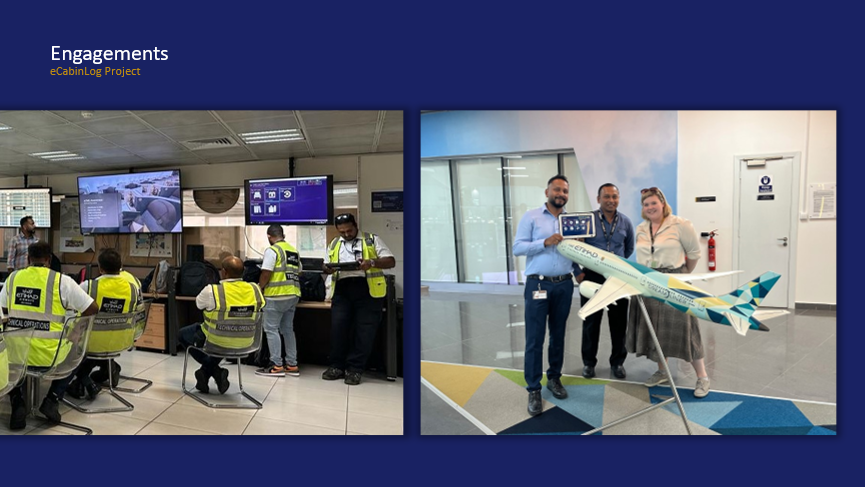
Image 1 is when we started the discussion with Conduce who already had a Cabin Log application which we rejected before we started going back to the drawing board to give them all of our requirements. It was quite challenging for them but a couple of months later they had something usable that we were happy about. It was quite a good moment for all of us when we deployed the eCabinLog8 (image 2). In image 3 are some of the times when we were doing the awareness sessions and the deployment. We were very pleased at the end with the deployment (image 4) and, of course, meeting the timelines.
BENEFITS
When we look at benefits, we have tried to visualize them as an iceberg (figure 7).
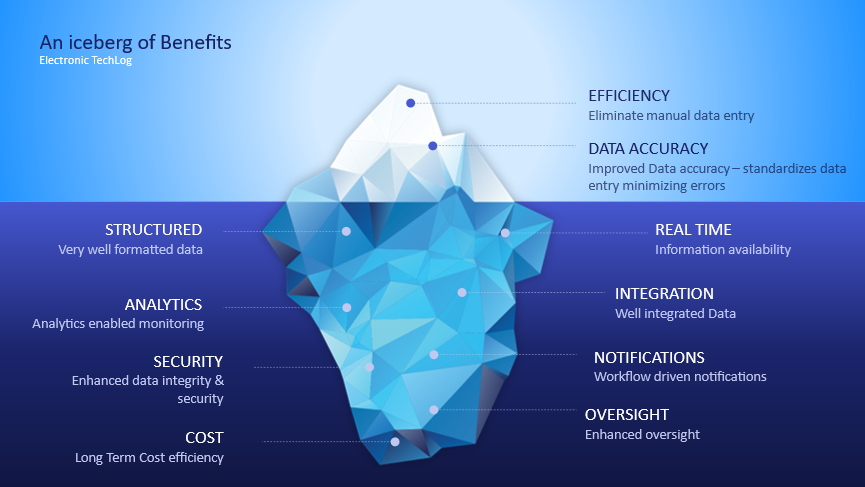
Figure 7
The tip represents the immediate benefits that we have realized with the deployment of eTechLog8. Errors are automatically minimized and manual data input is almost zero: those are the very quick gains that you get but that’s just the tip of the iceberg. When you start looking under the hood with the capabilities for real-time data, structured data, integration… then you start to realize that you can do more with the data. I was having a discussion with a colleague about the ability to use data to get more out of it and we worked out that there is the possibility to do a lot more analytics, the data itself is more secured, there are notifications and alerts that can be triggered and a lot more that cannot be quantified but they all support what we are aiming for; to have a better oversight and control of the data. And, looking at the cost, it’s not just the cost savings on the paper, which we used to justify the cost of the eTechLog8; all of these other benefits come into the picture.
Our reliability team started using this data to build up an analytical report for the cabin (figures 8.1 and 8.2).
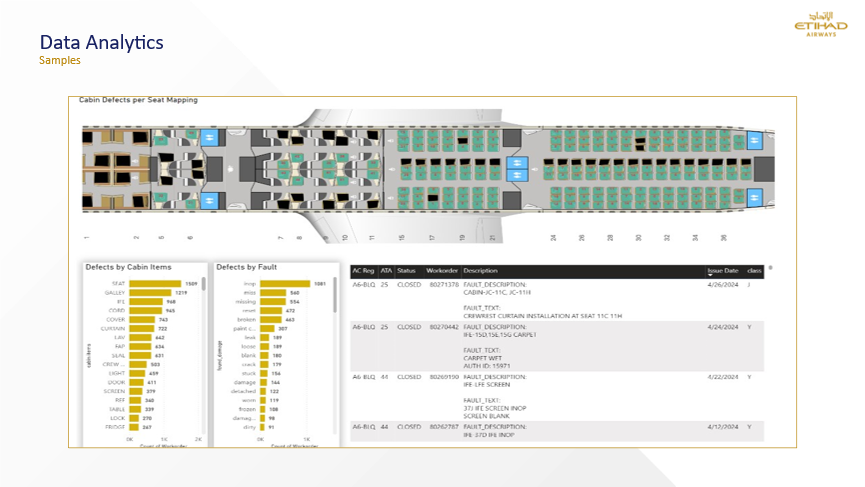
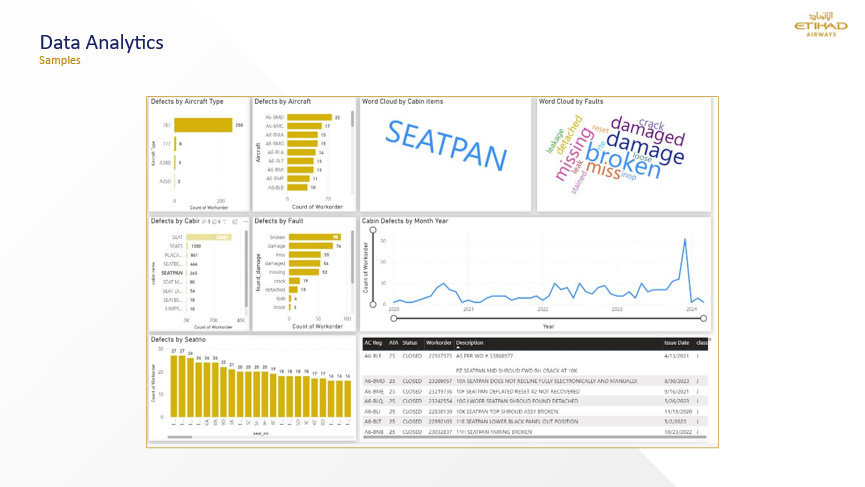
It’s still a work in progress but they’re grabbing all of that data and pushing it into a report with some logic to visualize it on a LOPA (Layout of Passenger Accommodations) and identifying the areas most prone to defects. Again, we are working with some machine learning models but the idea is to use this data and come up with a logic to identify areas where we can improve and eventually come up with some preventive maintenance that we can put in place before the defects are raised.
Figure 9 is our LOPA that we upload to the devices on board the aircraft.
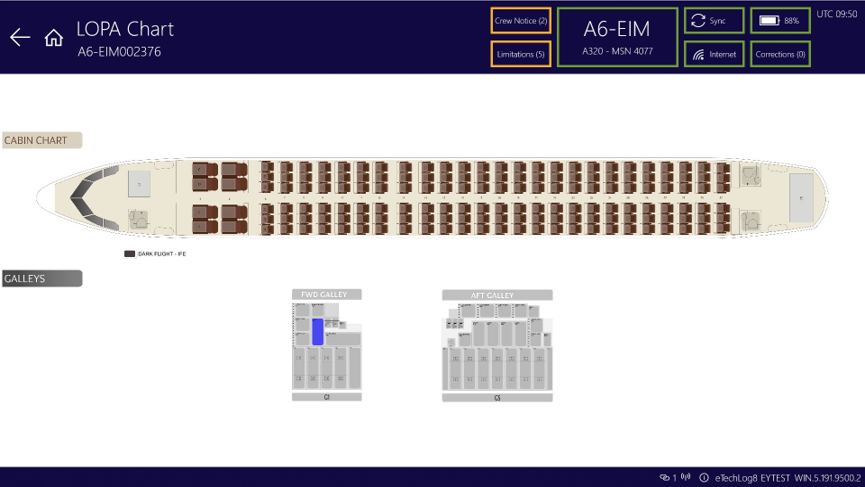
Figure 9
The reason why I have included this is that, before we went live with the eCabinLog8, we would notice the same defects getting raised several times because the cabin crew did not have the time to go through and identify what were the actual defects. They’d go in, see a defect and just raise it. When other crews came in, they would raise the same defect again and again. With this LOPA the visualization again makes it so easy for them to identify the defect and, once we deployed that, the duplication of defects went down to almost zero.
Although figures 10.1 is not from the eCabinLog8, I ‘d like to include it.
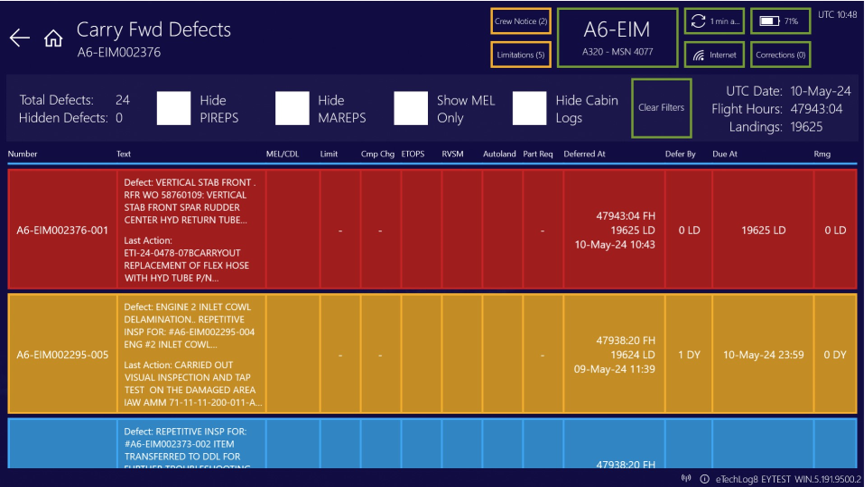
Figure 10.1
Again, it’s the power of this technology that gives engineers the option to be able to identify areas where they need to take action from the eTechLog8 as well as the system stopping the engineer from doing anything further unless they first action the reported defects. If it’s in red, it means that needs to be actioned before the aircraft can be released.
Repetitive defects (figure 10.2) is one of the other ones that I’d like to show readers.
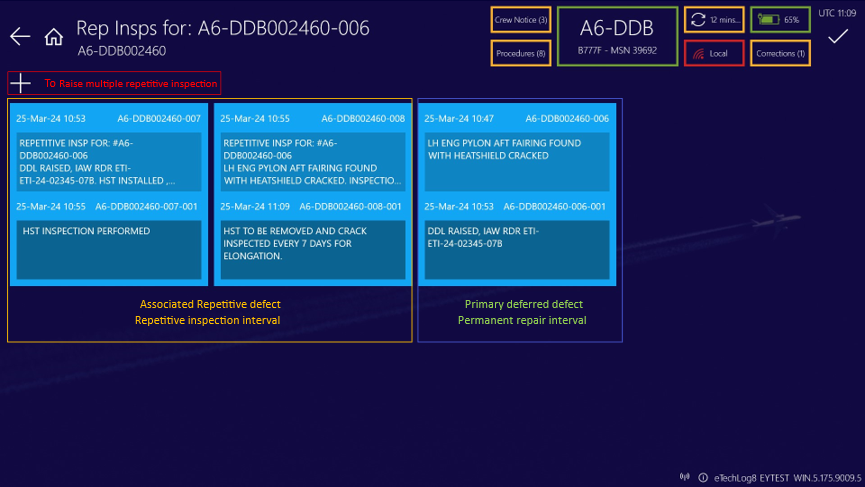
Figure 10.2
You link one defect with so many other repetitive inspection defects.
I’ve explained how good it is, how we implemented it and all that, but, as with any system, it also comes with its own challenges: challenges of connectivity, challenges of human error where someone misses something, software glitches that we continuously engage with.
These are challenges that will always be inherent to the system and we have built several Power BI reports to ensure that we monitor these before they actually cause us a delay and/or non-compliance (figure 11).
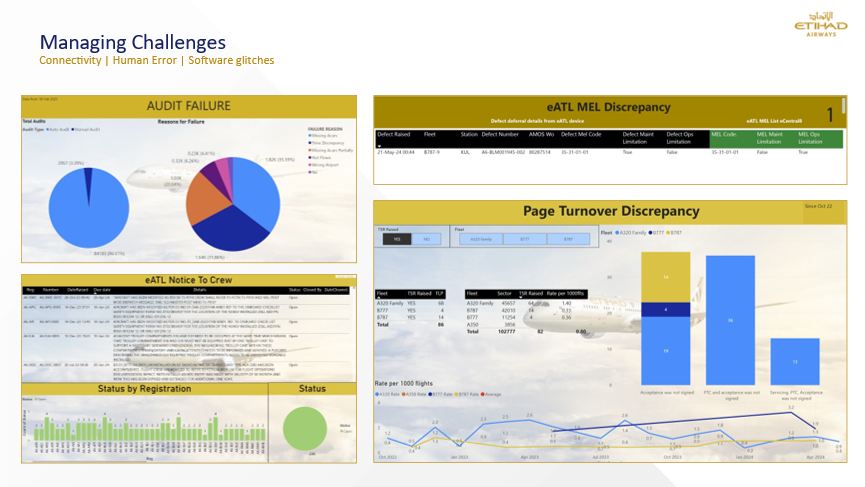
Figure 11
The final figure, figure 12, is what we are planning to do in the next twelve months.
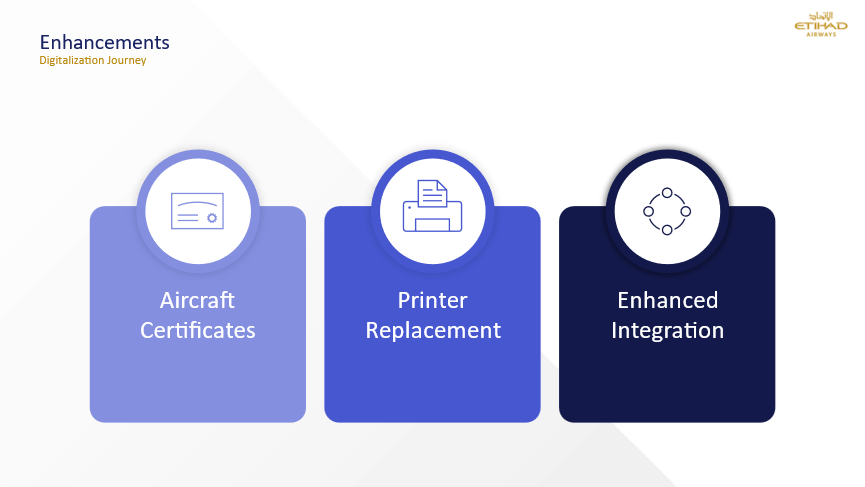
Figure 12
This is a long shot but we want to replace the aircraft certificates with a digital format. We cannot be certain whether the authorities will agree to that but we have started the engagement with them. It’s an area where there are a lot of questions and doubts but this is our aim to leverage the system to get us away from the paper-based world. We’re also planning printer replacement; I’ve seen a number of people who say that Conduce has a printer but we’re going to remove that and go with USB, one of the projects that we are working on. Lastly, we are pushing Conduce to increase and enhance integration: I think we will gain more capacity and more benefits, including structural, components and more, if this can be achieved.
Our journey on this is continuing but I hope that sharing our story with you will be useful for any readers considering embarking on a similar project.
Comments (0)
There are currently no comments about this article.
To post a comment, please login or subscribe.