Articles
Name | Author | |
---|---|---|
CASE STUDY: Mapping a better solution for Frontier Airlines | Joshua Lee, Senior Manager Technical Programs, Frontier Airlines | View article |
CASE STUDY: Improving efficiency of Wizz Air’s taxi fuel planning | Jaime Romero Waldhorn, Fuel Efficiency Manager at Wizz Air | View article |
CASE STUDY: Silk Way West Airlines embraces digital EFB and EFF solutions | Zahid Sultan Khan, Chief Pilot, Silk Way West | View article |
CASE STUDY: Fueling efficiency: how Azul soared with predictive analytics | Caio Garcia, Captain, Flight Ops Engineering Manager and Fuel Efficiency Manager at Azul Airlines | View article |
CASE STUDY: Engaging pilots in fuel efficiency at Azul Airlines | Caio Garcia, Captain, Flight Ops Engineering Manager and Fuel Efficiency Manager at Azul Airlines | View article |
CASE STUDY: Digital EFB operations at Aerolíneas Argentinas | Captain Ulises Raymundi, Pilot at Aerolíneas Argentinas | View article |
White Paper: Digital Towers and sharing useful information | Andy Taylor, CSO Digital Towers AT NATS | View article |
CASE STUDY: Fueling efficiency: how Azul soared with predictive analytics
Author: Caio Garcia, Captain, Flight Ops Engineering Manager and Fuel Efficiency Manager at Azul Airlines
Subscribe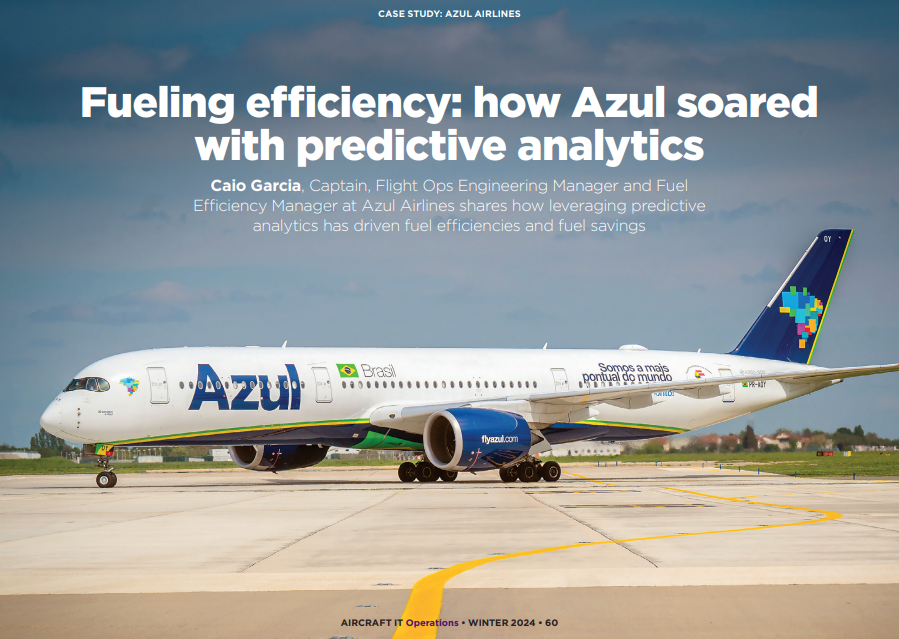
Caio Garcia, Captain, Flight Ops Engineering Manager and Fuel Efficiency Manager at Azul Airlines shares how leveraging predictive analytics has driven fuel efficiencies and fuel savings.
Before diving into the details of this case study, it’s important to provide some context about the environment in which it applies.
AZUL AIRLINES
Azul Airlines serves approximately 158 destinations, including many smaller airports across Brazil (Figure 1).
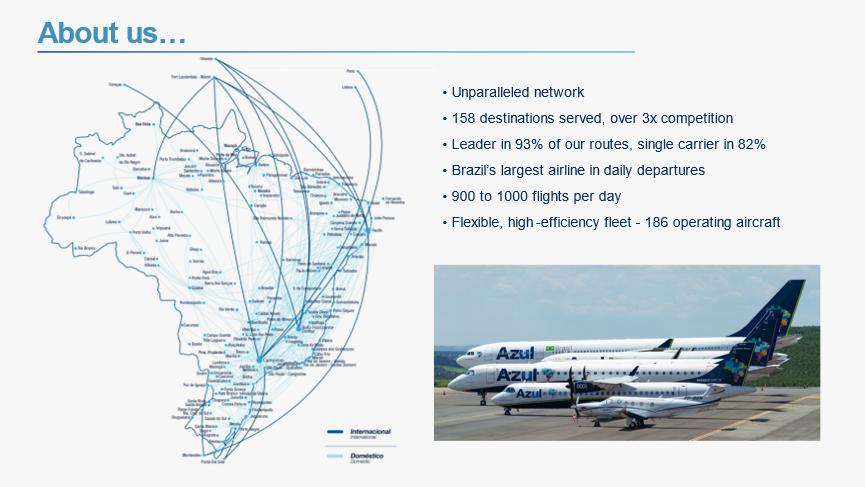
Figure 1
Our fleet consists of 186 aircraft, including Cessna Caravans, ATR 72-600s, Embraer 195 E1/E2, ERJ-190s, Airbus A320/A321neos, A321neos, A330ceos, and A330neos. Additionally, we operate a couple of Pilatus aircraft to transport parts to address any AOG (Aircraft on Ground) situations at remote airports. Operating within the Amazon region presents unique challenges, as parts are often difficult to procure locally. Therefore, the capability to ferry parts and deploy specialized maintenance teams is essential to minimize aircraft downtime in remote locations. We operate approximately 900 to 1,000 flights daily, depending on the season.
Azul and SITA: Working Together
Our partnership with SITA began in 2009, and they have been a trusted technological business partner ever since. We collaborate closely, often testing solutions before their official release (Figure 2). This valued partnership allows us to co-develop and gain early access to advanced technologies, providing us with the opportunity to test and refine them ahead of deployment.

Figure 2
Our initial collaboration with SITA resulted in Azul adopting AIRCOM, which now facilitates all communication with our aircraft through SITA’s AIRCOM services. Additionally, we leverage flight tracking via Mission Watch, which provides critical support to our dispatchers and Operations Control Center (OCC). Mission Watch ensures flights remain on schedule and avoid severe weather or other foreseeable disruptions along their planned routes. We also prioritize fuel optimization through solutions like OptiClimb and eWAS Pilot. Onboard each aircraft, pilots have access to an iPad equipped with eWAS Pilot, providing them with the same advanced weather interface available to dispatchers. This shared platform enhances situational awareness and operational efficiency – more on this later.
FOCUSING ON CLIMBOUT
When analyzing our operational scenarios, we consider the fuel consumption across short, medium, and long-haul routes (Figure 3).
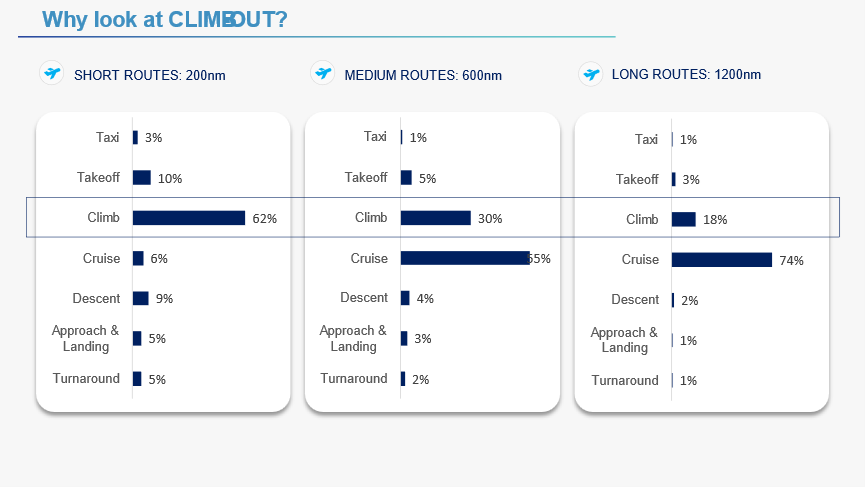
Figure 3
For short routes, approximately 62% of a flight’s fuel consumption occurs during the climb-out phase, making it a significant contributor to overall usage. Given that most Embraer fleet operations consist of 40- to 50-minute flights, these aircraft greatly benefit from optimization applications. The Airbus A320s primarily cover routes ranging from 200 to 600 nautical miles, occasionally extending to 1,000 nautical miles, while the Airbus A330s are dedicated to longer-haul operations. As shown in Figure 3, the climb-out phase is typically the first or second highest phase in terms of fuel consumption on any flight. This year, we are intensively examining the climb and cruise phases to identify areas for further optimization. One key strategy has been leveraging OptiClimb to enhance efficiency during the climb phase.
IMPLEMENTING A NEW SOLUTION
For any flight deck solution to succeed, securing pilot buy-in is crucial. The key to achieving this is simplicity. If a new system adds more than 30 seconds to a pilot’s preparation time or routine without a clear explanation, adoption will be challenging. The solution must be straightforward, seamlessly integrated into Standard Operating Procedures (SOPs), and accompanied by clear communication about its benefits. When pilots understand how a change improves efficiency without increasing workload, buy-in is naturally built.
One common question from pilots is why we’re transitioning from ECON to OptiClimb when ECON has been used effectively for decades. My response is simple: “Why rely on a fax machine when you could use email?” OptiClimb represents an evolution—building on what ECON provided but offering significant advancements. While ECON was effective in its time, it relied on a baseline aircraft model. OptiClimb, by contrast, delivers tailored, tail-specific optimization based on flight data unique to each aircraft.
OptiClimb integrates seamlessly with our operational processes. It automatically ingests data from the Operational Flight Plan (OFP) and generates recommendations 30–40 minutes before a flight, considering forecasted winds, temperatures, and aircraft-specific characteristics like weight and historical performance. This precision is achieved through extensive machine learning and integration with other onboard applications, ensuring pilots receive the most accurate and actionable information. The system also provides baselined savings reports for each flight, allowing us to compare current flights with similar ones from the past. This capability demonstrates measurable efficiency gains, reinforcing its value. Perhaps most importantly, OptiClimb requires minimal pilot input, maintaining a low workload while delivering substantial benefits.
WHAT IS OPTICLIMB?
SITA captures a rolling years’ worth of historical flight data for each tail number and applies machine learning to this data (Figure 4).
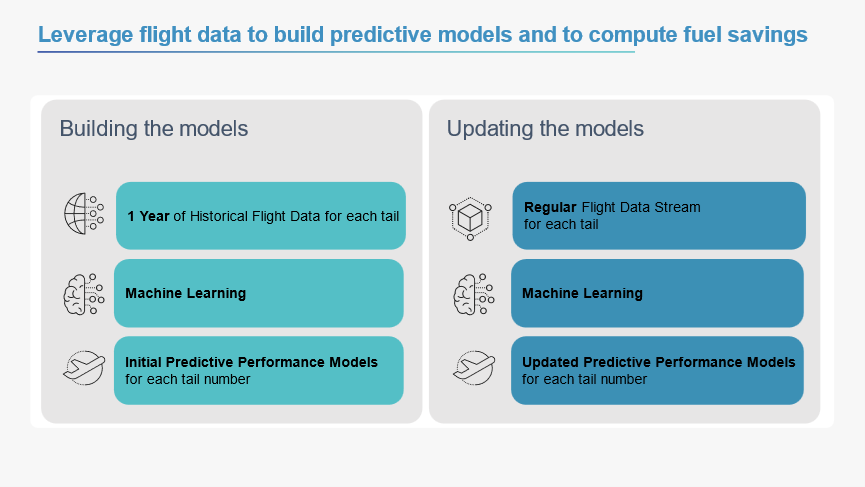
Figure 4
The process begins with creating a predictive performance model that analyzes the aircraft’s flight characteristics, degradation factors, and performance trends. It also examines whether specific actions – such as engine washing – improved performance. All this data is integrated into OptiClimb. Once OptiClimb is in use, it continuously receives data, which feeds back into the system, allowing for increasingly accurate recommendations. One observation we’ve made is that when new aircraft are added to the fleet, it takes some time for OptiClimb to ramp up. However, as the aircraft are flown more, the system gradually refines its recommendations.
After processing the historical data and completing the machine learning phase, OptiClimb receives the OFP data, 4D weather forecasts, and the tail-specific predictive performance model. It then applies a ‘what-if’ engine to generate recommendations, which are delivered to the pilots through three redundant channels to ensure they always receive the information (Figure 5).
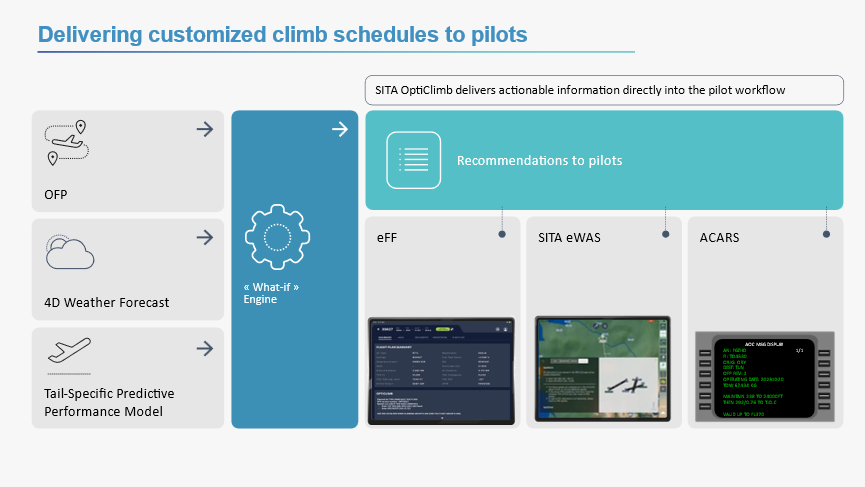
Figure 5
These channels are:
- eWAS Pilot, positioned centrally in Figure 5;
- EFF IsaBrief, our in-house software solution for the Electronic Flight Bag (EFB), which also outputs recommendations;
- ACARS, for additional redundancy.
By using these three channels, we ensure that pilots receive the necessary data, even if one channel faces issues—such as ACARS shortages in Brazil or 5G connectivity problems. The information will reach the pilots through at least one of the channels available.
HOW DOES IT WORK AERODYNAMICALLY, AND HOW DOES IT FLY?
The operation of OptiClimb can be broken down into two key phases (Figure 6).
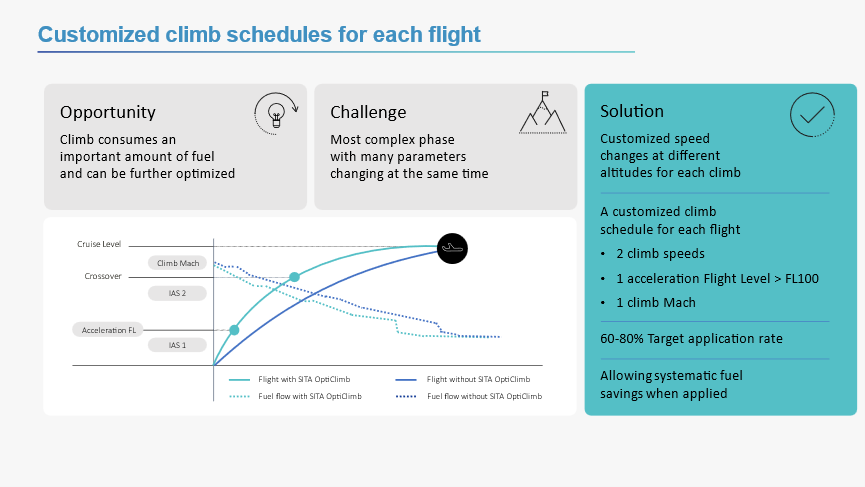
Figure 6
The first, IAS1 (Initial Acceleration Speed), also known as the Acceleration Flight Level, can be seen at the bottom of the figure, with IAS2 following. These represent two speeds: the initial climb speed and the second speed after the Cross-Over altitude, which is when the aircraft transitions from knots (nautical miles per hour) to Mach (a percentage of the speed of sound). Once the aircraft surpasses this cross-over altitude, its speed increases, accelerating towards cruise speed. During this phase, the aircraft is optimized to climb as quickly as possible, taking advantage of favorable weather conditions such as ideal winds and ISA (International Standard Atmosphere) temperatures. Once the aircraft reaches the cross-over altitude, it begins to build energy, enabling it to reach the cruise level with optimal conditions for maintaining cruise speed.
OPTICLIMB AT AZUL
In Figure 7, you can see how we began implementing OptiClimb at Azul.
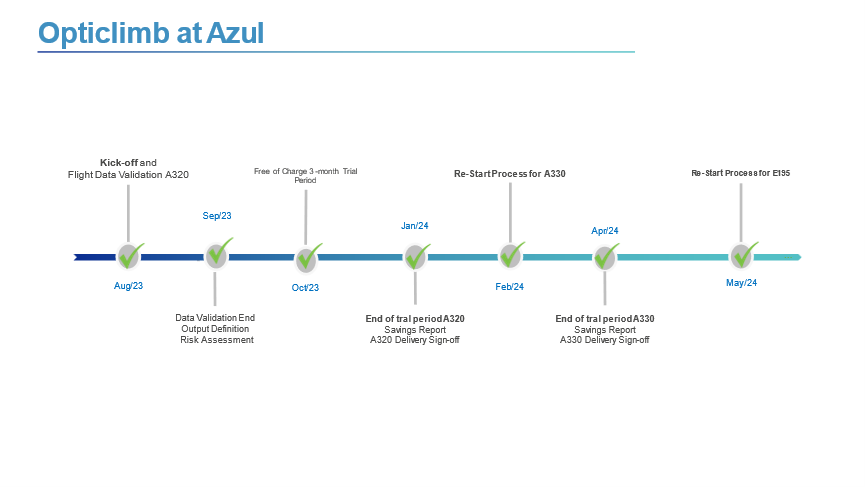
Figure 7
We kicked off with OptiClimb in August 2023 and started data validation about a month later, aiming to understand all the insights we could gather. In October, we began a free three-month trial period, which concluded in January when we went live with the Airbus A320 fleet, fully incorporating it into our SOPs. Once the A320 fleet was fully integrated, we moved to the A330s, and, after ironing out any issues there, we proceeded to the Embraer E1/E2 fleet. There are still some challenges with the E2, which are not specific to SITA or Azul, but rather due to data interpretation issues with the aircraft itself. This is something we’re addressing in collaboration with our partners, as it’s a common issue with E2 data.
At the time of writing, we were finishing the E1 integration, which had gone smoothly. The phased implementation approach was critical to ensure that each aircraft type was fully tested before progressing to the next. Every aircraft has unique characteristics and data requirements, so we took the time to work closely with the chief pilots, IT, and other departments to ensure proper integration and smooth operations. The process helped the team learn from each phase, making subsequent implementations more efficient and informed. By the time we reached the Embraer E1, the transition was seamless, making it one of our smoothest rollouts to date.
One of the key advantages of OptiClimb is how it simplifies management for leadership, particularly pilot leadership. The system clearly presents the information needed for effective program oversight, ensuring that pilots can easily understand and apply it. Pilot buy-in was crucial, and with OptiClimb being integrated into the SOPs (Standard Operating Procedures), it became part of their routine without adding to their workload. Additionally, explaining the new technology as a novel experience – especially since no one else had used it – helped increase buy-in. The gradual, phased rollout not only allowed us to troubleshoot and refine the system before each phase but also gave us the time to foster a supportive culture before fully scaling up.
Challenges mainly arose in relation to Air Traffic Control (ATC). There were some Standard Instrument Departures (SIDs) where OptiClimb faced penalties due to speed restrictions. In these cases, ATC would sometimes restrict us, but we worked through it. Initially, the application methodology was more manual, especially with the A320 fleet, which served as our test bed. Over time, the process became more automated, which improved the application rate and made it easier for pilots to adapt and embrace the system.
Figure 8 shows SITA eWAS working alongside OptiClimb.
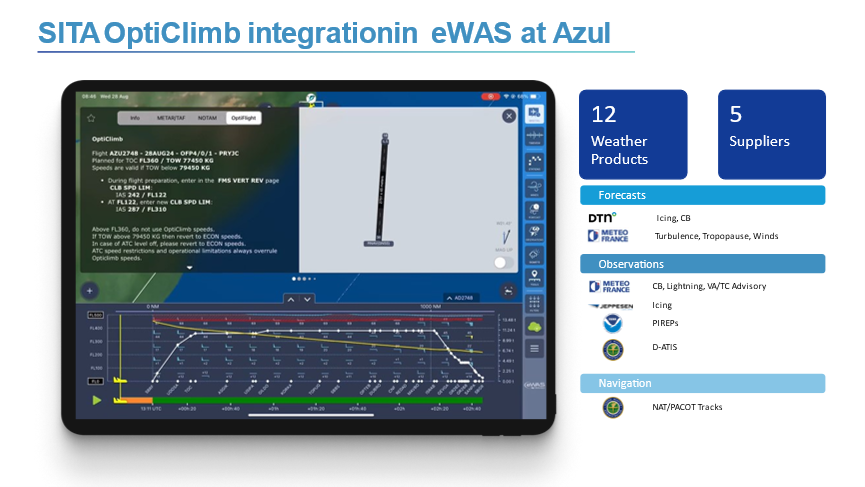
Figure 8
PILOT INTERFACE WITH OPTICLIMB
When the pilot inputs the data into eWAS Pilot, they receive a comprehensive route overview, including all weather information displayed (as shown in Figure8). Once the pilot reviews the route briefing and weather conditions, they can then check the OptiClimb/OptiFlight recommendation within the app. In the top corner of the app as well as on the departure airport, there’s a small leaf icon. By clicking this icon, the pilot can access detailed information about the airport, and on the right side of the screen, there are four buttons: Info, METAR, NOTAMs, and OptiFlight. This setup enables the pilot to view the OptiClimb recommendation as part of their weather and flight assessment process. The integration of this data into the pilot’s workflow ensures that everything is part of their normal flight preparation.
For the A320, we use a managed mode without the Mach speed setting. On the ground, the pilot inputs the recommended OptiClimb speed into the vertical revision page. Later in the flight, they input the data again. Previously, we had to switch the aircraft from managed speed to manual speed, which occasionally led to oversights, especially during high-workload situations like climb and ATC communications. By keeping the system in managed speed, we eliminated the risk of forgetting the manual input, resulting in a higher application rate.
For the Embraer fleet, the process is even simpler. The pilot inputs both speeds on the ground, and once the data is entered into the FMS (Flight Management System), OptiClimb takes over for the climb phase. From there, the system runs automatically until the aircraft reaches cruise, with no additional pilot input required. The higher automation on the Embraer fleet, particularly with the ground-based speed input, has led to an even higher application rate.
Figure 9 illustrates some of the average savings per climb for the A320/321 fleets.
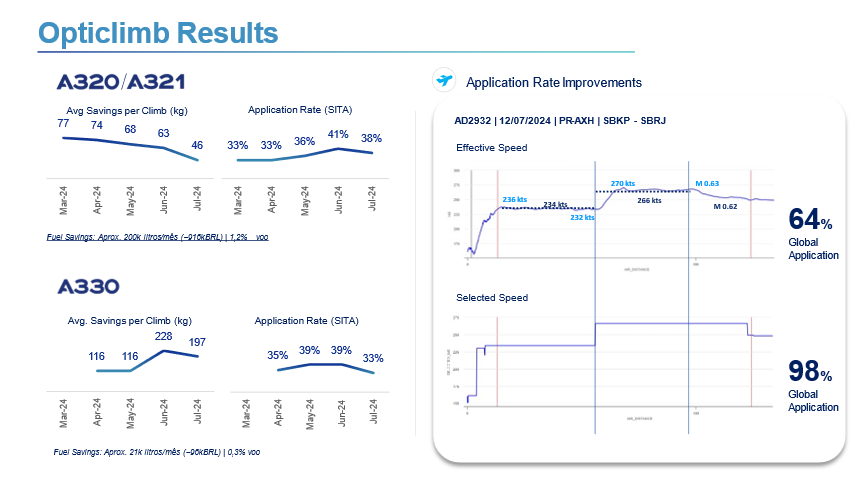
Figure 9
SAVINGS AND APPLICATION RATE IMPROVEMENT
The savings from OptiClimb gradually declined, and the application rate dropped slightly for the A320/321 and A330fleets due to certain flight characteristics and external factors. In July, we encountered weather and ATC challenges that impacted operations. However, even with these obstacles, we observed an average savings of about 46 kg per climb for the A320/321 and 197 kg for the A330.
We are continuously working on improving the application rate. On the right side of Figure 11, you can see a specific flight example. To measure the application rate, SITA and Azul analyzed the indicated airspeed, but this measurement can be affected by turbulence, climb speeds, and other variables. In discussions with our fleet captains, we realized that we may have been focusing on the wrong metric. Once we adjusted our focus to the actual speed instead of the indicated airspeed, the application rate improved significantly – from 64% to 98%. This adjustment removed the influence of turbulence and other factors, providing a more accurate reflection of the pilots’ actual application of the system.
Figure 10 shows a comparison of flight-to-flight savings.
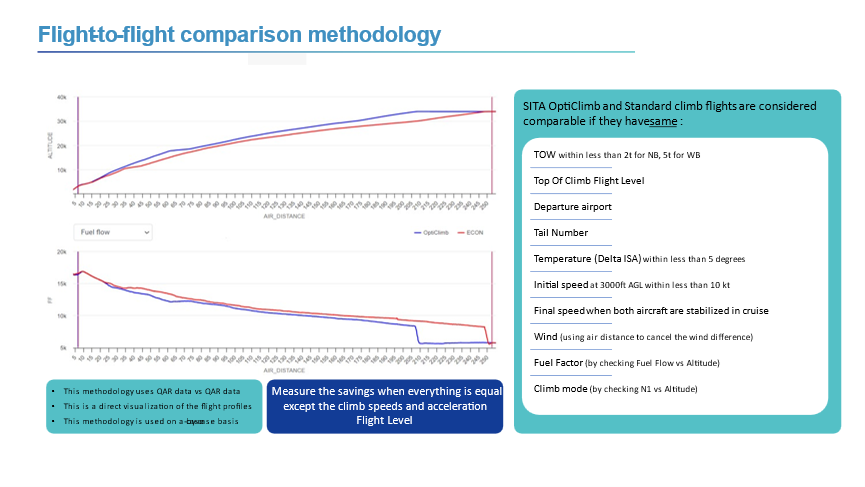
Figure 10
Secondly, in figure 11 is an example of one of our own flights.
OPTICLIMB VS. ECON PERFORMANCE COMPARISON
In Figure 13, the blue line represents OptiClimb, while the red line represents ECON. The first graph shows altitude over distance, demonstrating that OptiClimb climbs at a higher rate compared to ECON, before both systems level off. The second graph, which shows fuel flow, illustrates that OptiClimb consistently consumes less fuel than ECON until both lines converge towards the end of the climb.
The key to OptiClimb’s efficiency lies in its ability to leverage weather conditions during the climb phase, optimizing the aircraft’s performance to maintain a slightly lower fuel flow compared to ECON. For these graphs to be comparable, several parameters must align, as shown on the right side of the figure:
- Take-off weight (within a 2-tonne difference);
- Same top-of-climb flight level;
- Identical departure airport;
- Matching tail number;
- Consistent temperature (Delta ISA);
- Same initial and final speed;
- Identical wind conditions;
- Comparable fuel factor;
- Consistent climb mode.
By matching these performance parameters, the system can analyze and compare OptiClimb’s performance against previous flights in the database to assess its effectiveness.
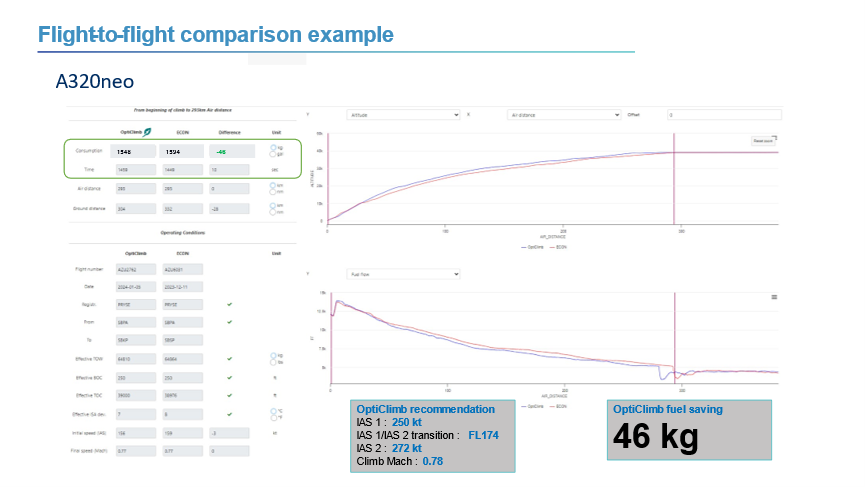
Figure 11
FLIGHT SAVINGS AND PERFORMANCE INSIGHTS
In this example, we see a 46 kg fuel saving, which aligns with the data shown in Figure 12, though with some added variability due to turbulence and other flight factors. As the aircraft climbs and reaches FL390, it levels off, maintaining the necessary cruise energy to sustain the cruise speed. For those familiar with flight deck operations, typically when the aircraft levels off, the throttle is slightly advanced, and once cruising speed is reached, it reduces. However, with OptiClimb, the throttle remains at the optimal level once the climb speed is achieved, as the system ensures the aircraft has the required cruise energy to maintain speed in level flight.
To summarize, the results show an average fuel saving of 46 kg, a 38% application rate that continues to rise, which resulted in 148 tonnes of fuel saved in July 2024, along with approximately 465 tonnes of CO2 saved (Figure 12).
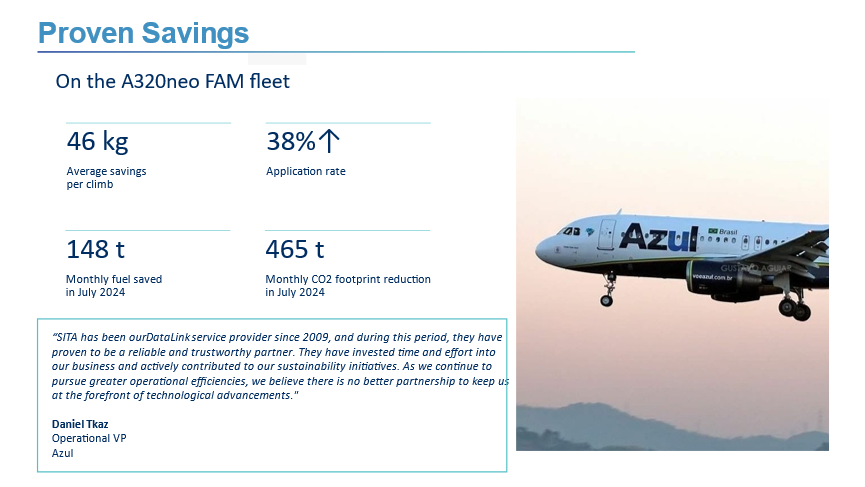
Figure 12
LOOKING TO THE FUTURE
We’re seeing some promising results from our efforts so far, particularly with the climb phase. We’re pleased with the progress and are now focused on the next step: implementing in-flight shortcut recommendations (Figure 135).
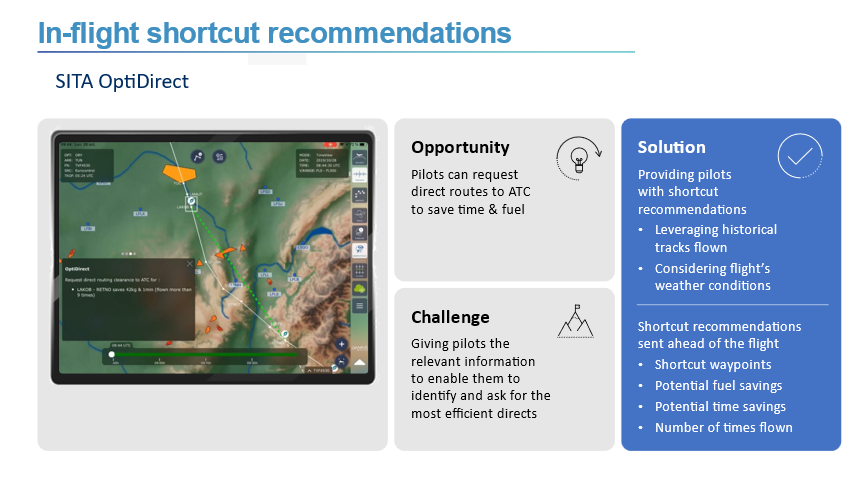
Figure 13
We are now exploring SITA OptiDirect, in conjunction with the eWAS tool, to provide recommendations for in-flight distance reduction. These recommendations will be based on our historical data to ensure that we receive the most accurate and probable in-flight distance reductions. The goal is to build on our success with the climb phase, and once SITA completes the final studies for the ATR (Aero-Thermodynamic Research) aircraft, we plan to begin rolling out these flight recommendations by the end of the year.
This has been an incredibly insightful, albeit challenging, process. We’ve learned a great deal and made significant progress. I hope that sharing our experience proves useful for any readers contemplating a similar project.
Comments (0)
There are currently no comments about this article.
To post a comment, please login or subscribe.