Articles
Name | Author | |
---|---|---|
WHITE PAPER: Current Trends in the Predictive Maintenance Aftermarket | Dr Ip-Shing Fan, Senior Lecturer in Enterprise Systems at Cranfield University and John Maggiore, senior aerospace leader and consultant and Senior Advisor to the Integrated Vehicle Health Management (IVHM) Centre at Cranfield University | View article |
CASE STUDY: Making a good digital start at Heston Airlines | Edgaras Knyzas, Head of CAMO, Heston Airlines | View article |
CASE STUDY: Production planning and control at China Airlines | Wei-Fong Wang (Matt), Senior Engineer, Maintenance Division, China Airlines | View article |
CASE STUDY: An RFID cabin monitoring tool at AirAsia Thailand | Banyat Hansakul, Group Head of Engineering, AirAsia and Nazrulazli Najmudin, Senior manager, Product and Technology, Asia Digital Engineering (ADE) | View article |
CASE STUDY: Production planning and control at China Airlines
Author: Wei-Fong Wang (Matt), Senior Engineer, Maintenance Division, China Airlines
SubscribeWei-Fong Wang (Matt), Senior Engineer, Maintenance Division, China Airlines shares the airline’s experience of digitally transforming maintenance through data
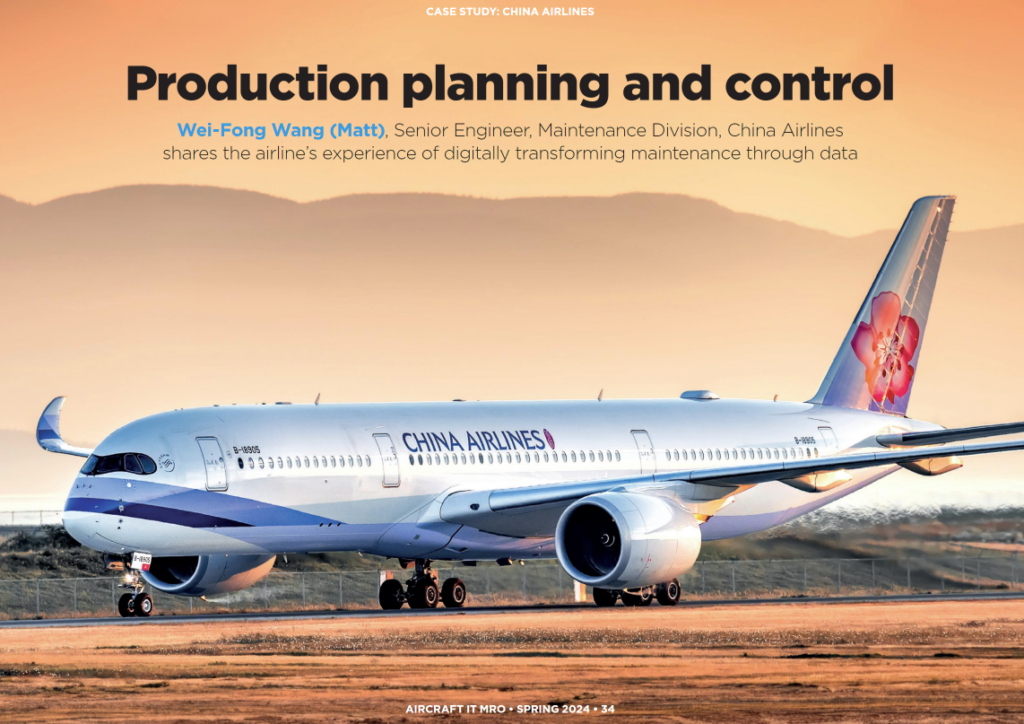
In this article I’m going to take the opportunity to share with readers the story of China Airlines’ integration of information with a domestic organization change. But I’ll start by telling you something about the subject of the study, China Airlines.
CHINA AIRLINES
Based in Taiwan Taoyuan Airport since 1959, China Airlines has a strong safety culture. We fly to over one hundred destinations with more than 12,000 employees. In addition to the main airline, there are two subsidiaries in the China Airlines Group, Mandarin Airlines catering regional flights and Tigerair Taiwan catering domestic flights, largely to serve offshore islands. The fleet is currently made up of more than 80 aircraft including Airbus A350, A330 and A321neo as well as Boeing 777ER, B777 Freighters and B747 Freighters, plus B737-800. There are also 24 Boeing 787 Dreamliners on order.
I’m part of the China Airlines EMO (Engineering Maintenance Organization) and in that organization there are three divisions.
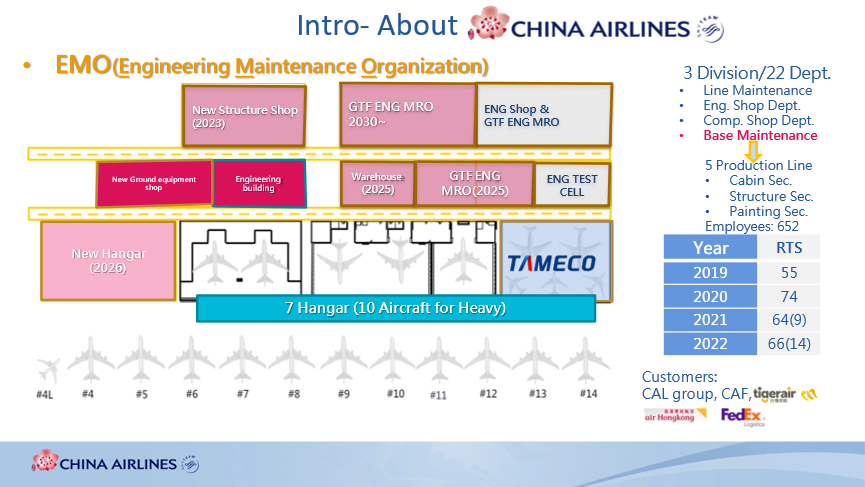
The first division encompasses the Engineering Division, which includes the Engineering Department, Planning Department, IT Department, and Material Support Department. Additionally, we have the Quality Assurance Division, consisting of the Quality Control Department, Audit Department, and Standards Department. Of particular note is the EASA Part 147 Training Center within this division.
The primary focus is the Maintenance Division, with Line Maintenance for Line operations. This division also houses a Component Shop for component overhaul and the Engine Shop. In 2025, we plan to open a new Engine Shop, and between 2025 and 2030, another one will be established specifically for handling Pratt & Whitney GTF engine MRO.
In the meantime, we inaugurated a new Structure Shop for Thrust Reverser (T/R) and Composite Material Maintenance Service. Furthermore, there are plans to open a new two-bay hangar in 2026. Currently, we operate seven hangars capable of simultaneously handling heavy maintenance for up to 10 aircraft. Additionally, we have a 100% subsidiarity MRO company named TAMECO.
In the Base Maintenance department, there are five production lines, each consisting of a Cabin section, a Painting section, and a Structural section. This department stands as the largest within the EMO, boasting a workforce of nearly 700 employees. From 2019 to 2022, our average for aircraft Return to Service (RTS) from Heavy Maintenance exceeded 50. Our clientele includes the China Airlines Group, encompassing Taiwan Tigerair and Mandarin Airlines, along with FedEx and the Taiwan Air Force.
WHY CHINA AIRLINES NEEDED A PRODUCTION PLANNING & CONTROL (PP&C) SOLUTION
There were four key drivers that made us realize that we needed this new.
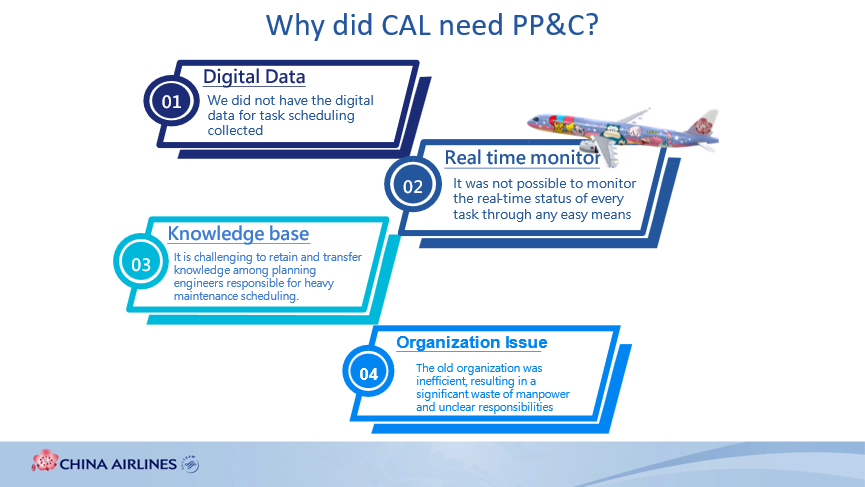
Before we had implemented the PP&C solution, we didn’t have digital data for scheduling, especially for heavy maintenance planning; neither did we have digital data to allow us to easily monitor the status of Heavy Maintenance processes. The third driver was about our planning engineers whose knowledge was not easy to transfer, again, especially for the Heavy Maintenance planning. Before PP&C, they used Excel files to plan the Heavy maintenance but nobody cared about the Excel files or that a given aircraft had to be returned to service. The next issue was that our old organization was inefficient resulting in a significant waste of manpower and unclear responsibilities.
WHAT PP&C DOES
For the PP&C solution at China Airlines, we have chosen to cooperate with IFS whose solution is comprised of three parts.
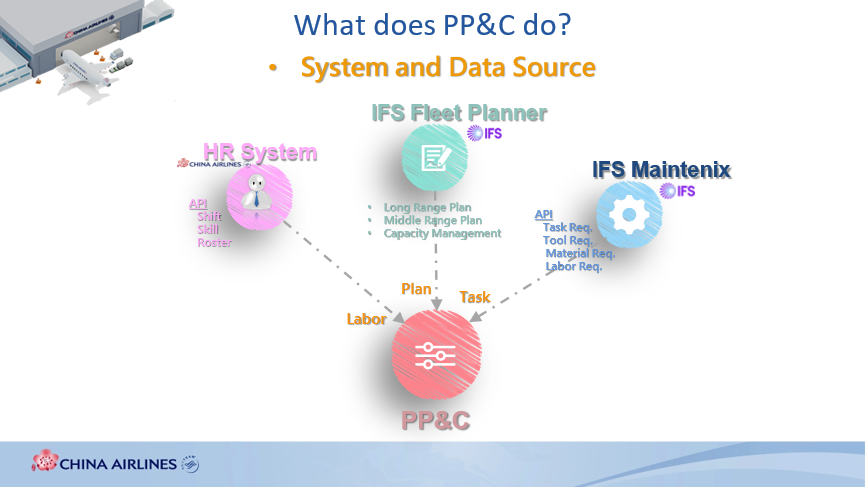
Those three parts are Labor, the Plan and the Task. They all have APIs (Application Programming Interfaces) that share data and therefore improve the data in the system. The HR (Human Resources) system deals with Shifts, Skills and Rosters and feeds into ‘Labor’ in the PP&C module. We are using IFS Fleet Planner for Long-Range Planning, Middle-range Planning and Capacity Manager which all goes into the Plan in PP&C. And, because we are using IFS Maintenix for our MRO solution, Task required, Tools required, Material required and Labor required all get fed into PP&C which will integrate the three input sources.
For China Airlines, the work flow is about our Engineering Planning department who will commit and transfer the work package 30 days before the work package commences.
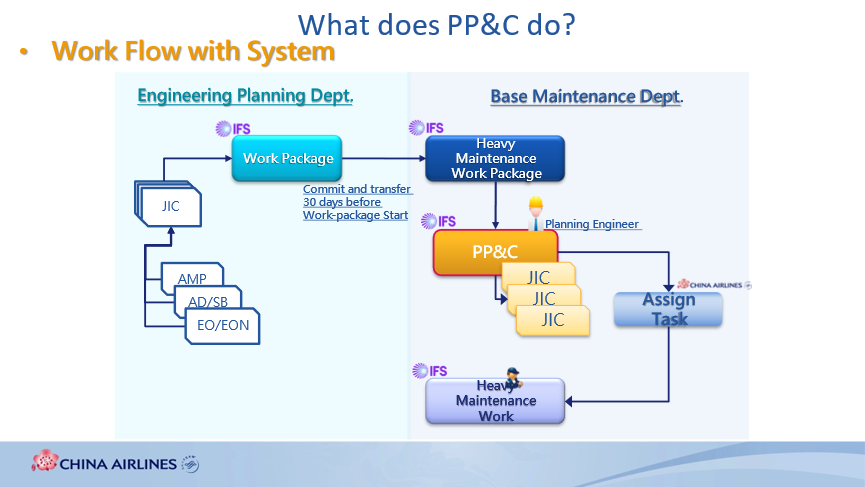
The work package includes all Job Instruction Cards (JIC), such as the Aircraft Maintenance Program (AMP), Airworthiness Directives (ADs), Service Bulletins (SBs), or Engineering Orders (EOs). Upon receiving the work package, the planning engineers in the Base Maintenance Department plan all tasks in the Production Planning & Control (PP&C) system. As heavy maintenance begins, the tasks are assigned through a web-based system on the Intranet (designed by China Airlines), facilitating a seamless and digital completion of the entire process.
So, what are the benefits from this chart?
PP&C is currently used by the planning engineers, the Project Manager and the Planning Controller. PP&C users can move the task into the work-package and every task will show on a Gantt Chart Currently, PP&C is not used by mechanics, who continue to use the original system.
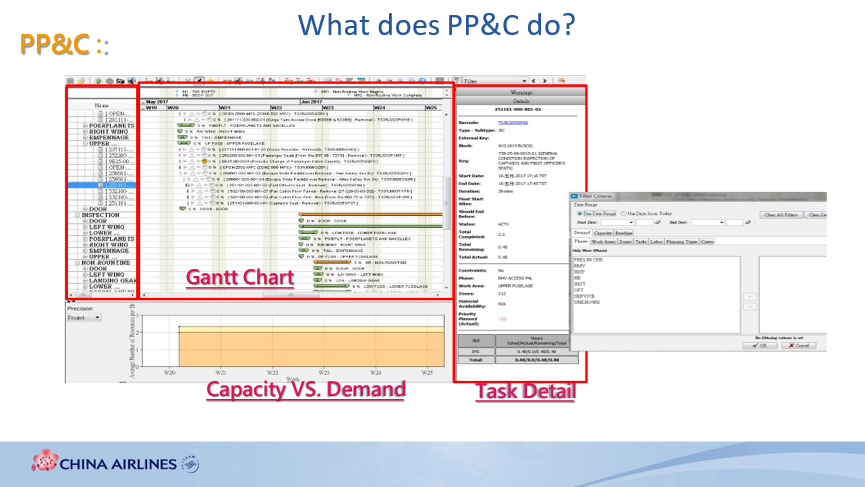
If the user clicks on any single task, that will show the details of the task and it will show the capacity versus the demand for the manpower for the task. It will show the materials status and the manpower status with a filter, sorting and tracking those elements. The Project Manager and Planning Engineer can effortlessly monitor these aspects for each task. If you configure the data in the system, users can categorize by phase and work area and PP&C will automatically help to arrange the scheduling for the right places and times to do the work.
PP&C also generates a daily report showing how many hours have been used for planned jobs and a non-routine report that shows how many hours are being taken up for non-routine jobs. PP&C has one specific function, which is the Knowledge Base, that can save a plan in heavy maintenance such as for the Triple Seven C1, if it is a good plan, it can be saved to the template, so that the next time there is a Triple Seven CI Maintenance to be performed the whole work package can be taken from the Knowledge Base to help with scheduling and planning the job.
The whole implementation of the PP&C solution in China Airlines took six months from kick off to go live.
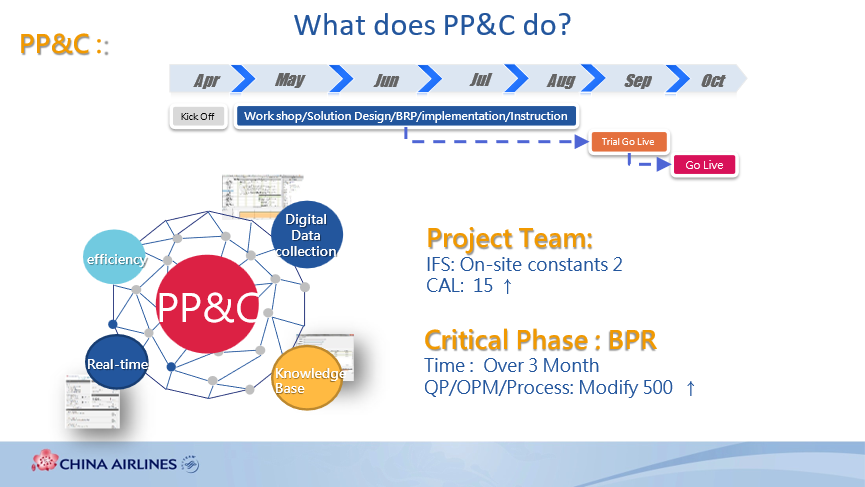
Of that time, we dedicated four months to developing the workshop solution design for Business Process Re-engineering (BPR) implementation and instruction. Following this, we conducted two trial runs over a two-month period. The first trial run focused on the narrow-body 737-800, while the second trial run centered on the 777-300ER. IFS provided valuable on-site support by sending two consultants to assist with the implementation. Their professional approach and commitment, even working during holidays, were greatly appreciated. China Airlines contributed a team of 15 members. The most critical phase was the BPR, as it involved substantial changes to our colleagues’ procedures, the Operational Procedures Manual (OPM), and over 500 processes.
WHAT CHANGED POST-IMPLEMENTATION
How did China Airlines’ implementation of the PP&C solution affect different divisions and departments? To answer that, let’s look first at our old organization (figure 7).
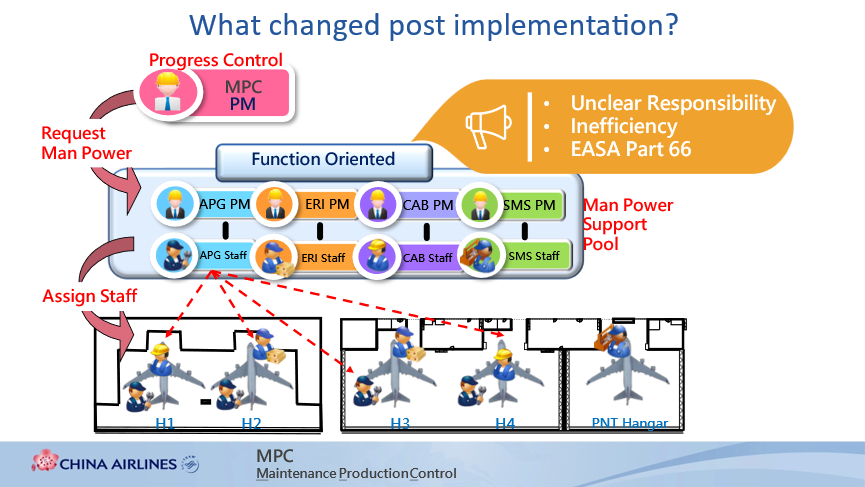
The organization before we took on PP&C was function orientated; we separated mechanics by their skills. Like the Airframe, Powerplant and General (APG), the Electronic, Radio and Instrument (ERI), Cabin and Interior (CAB) and Structure and Metal Shop (SMS). We had one Maintenance Production Control Center (MPC) with a few project managers in charge of Heavy Maintenance management and monitoring, and the controller for all heavy maintenance aircraft, but they didn’t have the power to control the availability of human manpower. They needed to request the manpower they needed every day and the section manager assigned the staff to the aircraft. So, implementation of PP&C encountered some problems.
The first problem was an unclear allocation of responsibility because the project managers were responsible for everything, but allocation of the manpower was not within their control. The second problem was inefficiencies because they were spending a lot of their time assigning manpower. The third problem was EASA Part 66 because our new certificate for EASA for the mechanic required all historical data for that mechanic and they needed to get that. If we were using the old registration, it just focused on the one area, not all areas, so we couldn’t apply for the new certificate from EASA.
PP&C was not just software for China Airlines; it was also a catalyst to let China Airlines seriously consider potential problems in our organization. We spent one year for simulations and for testing, for the trial run and to do the whole new production line.
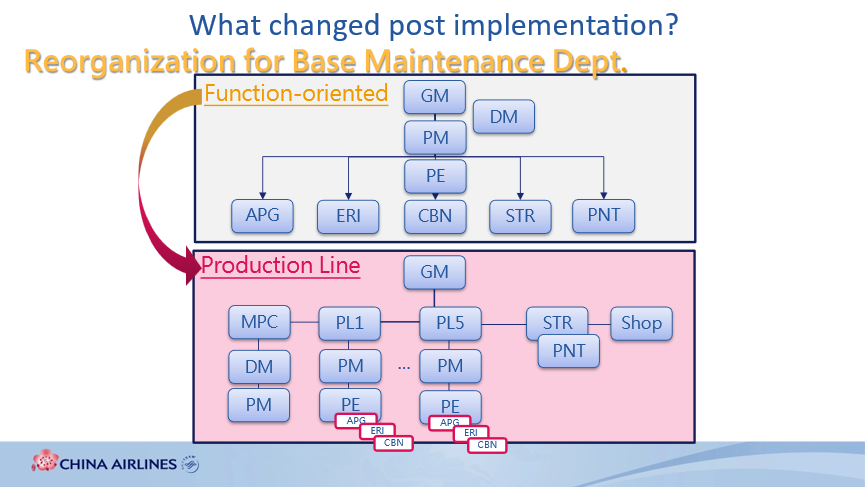
At the time of writing, our maintenance production centers were arranged in these departments. We have a duty manager who will assign the aircraft to the production lines. We separate the mechanics, the APG, ERI and Cabin mechanics who are sent to every production line and we also keep the structure and the section and the internal shop because they are needed to support the production line.
Also, we have taken three years for training the APG and the ERI mechanics. Right now, the ERI mechanic will know how to change the engine and how to open the right panels. At the same time, we have renovated our office and the Control Room.
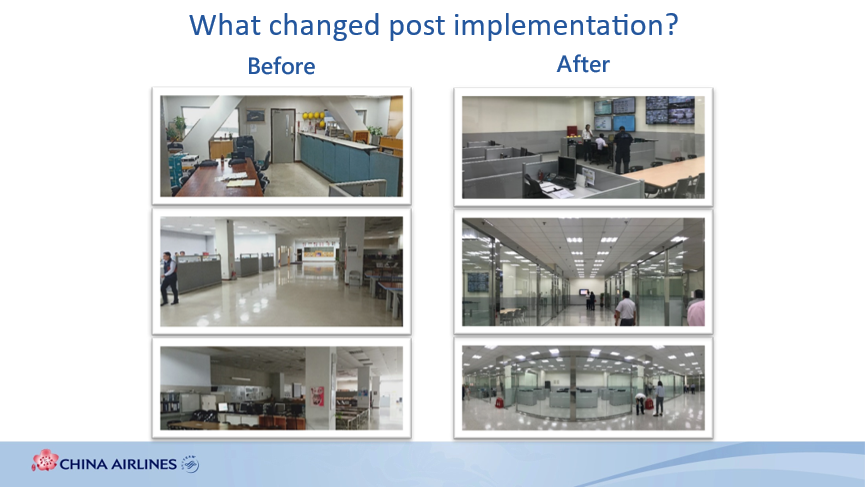
At China Airlines, we now also create over twenty reports. The first one was our dashboard.
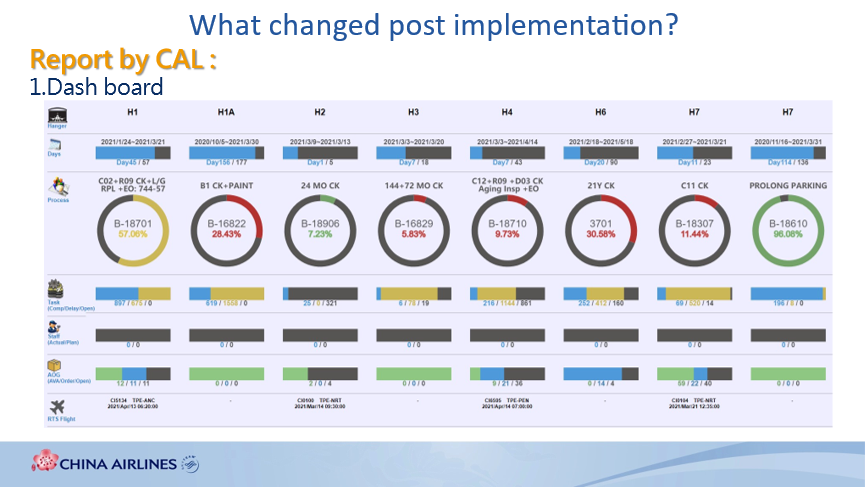
Right now, we refresh the dashboard every 30 seconds, allowing users to drill down into a detailed dataset for each item. The first item on display is ‘where is the aircraft?’ If the aircraft is in motion, the dashboard dynamically updates. The second item shows the number of remaining days. The third item, represented by the circle, is the progress indicator for Heavy Maintenance: if they are behind the total schedule by 10%, the indicator turns amber; if the delay exceeds 20%, it displays in red. This visual cue serves as a reminder for both the manager and project manager, signaling significant delays that require attention and action.
For each task, we want to know details about the delay, how many tasks are open, how many staff are engaged on the task compared to how many were planned, plus we consider the AOG parts and how many of those AOG parts are available right away, how many are on order or how many are still open. And, if there is an RTS (Return to Service) Flight it will show at the bottom of the Dashboard.
After implementation of PP&C, we had to think about the quality for the planning engineers. We created one report to check every day with their KPIs.
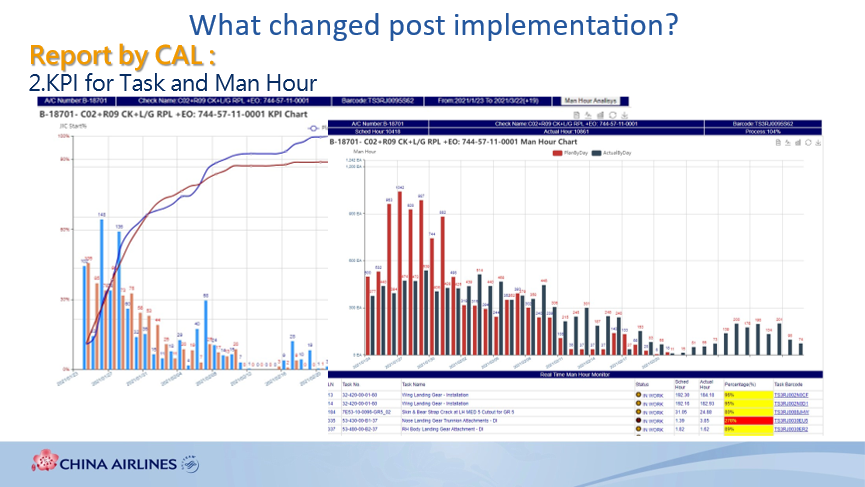
From the KPI Chart, we will know how many tasks we need to start today and how many tasks are actually being started. The red lines show how many tasks need to be complete for the ratio while the blue line is how many tasks were expected to be completed. Every day, using this report, we can check our status and be very careful about our manpower; so, the next one is our manpower chart in real time. Readers will understand, in heavy maintenance we have a huge physical area so we cannot use laptops or PCs everywhere, especially with the Intranet. So, we have designed and developed a new mobile application for China Airlines to work with the PP&C solution.
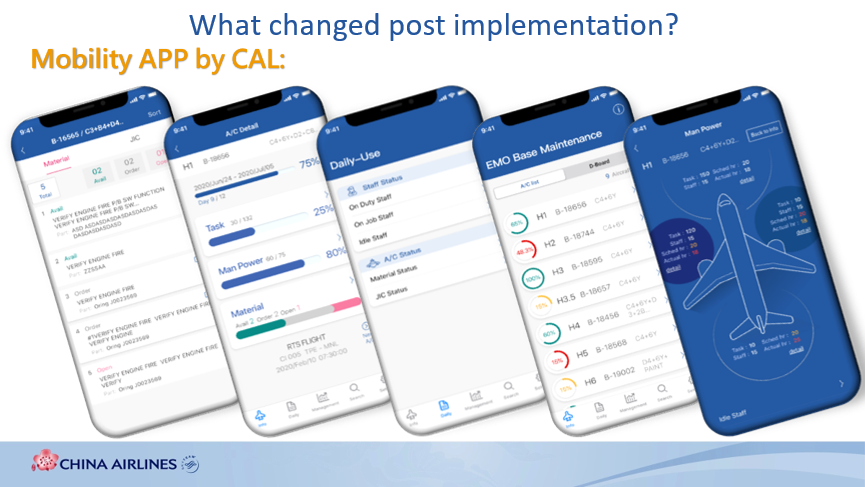
The concept is that the App pulls data from PP&C, from the Maintenance system, and from our HR system. The first screen in Figure 11 uses the materials list combined with the progress and that can be seen for one aircraft so that users will know what percentage has been progressed right now. Also, if the user clicks on any one aircraft in Heavy Maintenance, that will show the task, manpower and material. The task will have another list that will show how many tasks have been assigned with how many tasks have been completed, and every task will show the scheduled hours and the actual hours, in real time. The right screen is manpower minutes. We separate the aircraft into the four parts; for example, the right part is how many tasks (right now we have ten tasks) and 15 staff in this area. The scheduled hours are 20 hrs and the actual hours are very close to the scheduled hours so that will remain in the project manager. The tail area could maybe have some problems such as a material issue, tasking issue and/or mechanic issue which might cause a delay.
For China Airlines, the combination of implementing PP&C from IFS, using the maintenance system and our re-organization to the production line brought about several efficiency improvements.
In the first place, we have reduced total man hours by 5% per year and have reduced multi-crew JIC (Job Instruction Card) manhours by 10% per year. Heavy Maintenance turnaround time (TAT) has been reduced by 13 days per year so delayed returns to service are down to less than one a month. Actual man-hours have increased to 5.5 hours per day for Heavy Maintenance mechanics while planning engineer planning time has reduced by 50%. And finally, which is special for us, we no longer lose any physical Job Instruction Cards (JICs).
LOOKING TO THE FUTURE
We continue to work with IFS to further enhance PP&C, plus we are undertaking a line planning solution evaluation. We will continue sharing ideas and feedback on the operation of the solution with IFS. Internally at China Airlines, we are creating a data bank and a data warehouse with plans to implement data mining. Also, in recent months, we have kicked off APP Phase 2 with extra functions for the APP. Lastly, we have a new mission for China Airlines because I have been asked to generate the strategic plan for the next five to ten years. We want to create smart hangars using mobility and a smarter warehouse. We’ll be happy to share our information and experience if any readers want to contact us.
I’ll close with the words of Michael Jordan, “I can accept failure, everyone fails at something. But I can’t accept not trying.”
Comments (0)
There are currently no comments about this article.
To post a comment, please login or subscribe.