Articles
Name | Author | |
---|---|---|
CASE STUDY: Streamlining maintenance planning at JetBlue | Erin Ritola, General Manager, Maintenance Planning, JetBlue | View article |
CASE STUDY: The transition to mobility | Stephane Menard, Chief technology Officer, M3 Solutions, Steve Bogie, Partner, AeroATeam and Frank Milillo, Partner AeroATeam | View article |
CASE STUDY: Virgin Atlantic uses an electronic record system for lease requirements and returns | Lee Butterfield, Head of Aircraft Programmes and Asset Management, Virgin Atlantic | View article |
CASE STUDY: Kalitta Air takes a big digital step | Luke Usher, QC Records Manager, Kalitta Air | View article |
CASE STUDY: Helvetic goes from a fully managed system to a SaaS solution | Christian Suhner, Chief Technology Officer, Helvetic | View article |
CASE STUDY: Streamlining maintenance planning at JetBlue
Author: Erin Ritola, General Manager, Maintenance Planning, JetBlue
Subscribe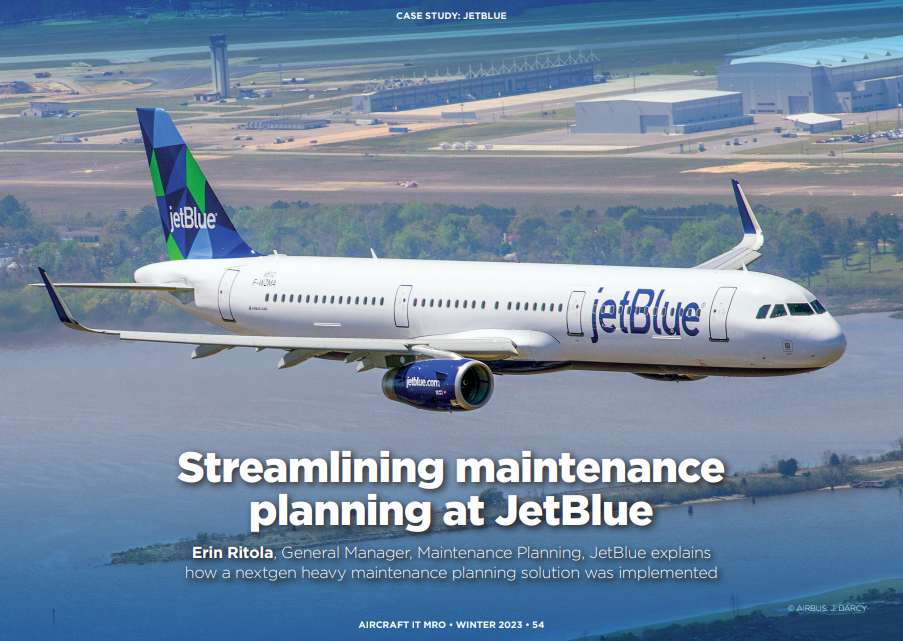
A case study on implementing a nextgen heavy maintenance planning solution
Although I trained as an aircraft technician, I joined JetBlue shortly after 9/11 and took a maintenance planning role rather than as a line technician. In 2006, I joined the heavy maintenance team as a controller taking all the planning work for heavy maintenance with me. We split heavy maintenance out of our Planning organization to keep it centralized to heavy while letting line maintenance planning focus on line maintenance. Even before 2015, we realized that wasn’t really working well for JetBlue overall. The airline had grown quite a bit with, then, 200 aircraft and we were working towards what we called our TechOps 300 project which was to consider how we were going to operate at 300 aircraft instead of the small-fleet point of view that we’d had before. So, I reconsolidated planning back into one group and brought with me the heavy maintenance scheduling concept that I’d been developing over the past decade.
THE CHALLENGES OF THE OLD SYSTEM
At that time, I started working together with two other planners for heavy maintenance and realized that the system that I had developed, while it was endlessly customizable and had worked well for JetBlue in the past, wasn’t going to work for us very well in the future.
The reason was that it was completely Excel based and while there was a tremendous amount of detail in it, which our team liked along with the detail and the information in it, when we tried to teach it to the new planners, they just didn’t get it. So, the first big con that said that we needed to find something else was that fact that it was really difficult to train other planners on the system plus, it was hard to share. We tried splitting it by fleets for which, at the time, we had two primary fleets, the A320 fleet and the E190 fleet and were starting to take on the A321 aircraft and get into sub-fleets. But even with splitting the system, trying to marry all that material back together into one published document just didn’t work. It was tedious, it was time consuming and, as we added more people to the team, it became increasingly error prone.
SELECTION CRITERIA FOR A NEW SYSTEM
So, our VP at the time agreed that we should shop around for a new solution, but I hate to shop. I find what I need, decide if I can afford it, make sure that it’s going to work and buy it. However, the VP wanted us to shop the market, look at all the offerings out there then generate detailed reports on the pros and cons of the different programs and find the industry leading, next generation heavy maintenance planning software that will lead JetBlue into the future. That launched a review of what was in the market but first, we established what we wanted to do. Our main focus was to get away from the spreadsheet; no more manually moving blocks of information around. Then we considered how did we want planning to work overall? Planning is more than just putting work into work orders, and it’s a whole lot more than the basics of who does what, at what time, where and with what stuff. Planning sets the strategy for the organization; it sets the tone and says where you are going; it can start and stop aircraft. If the planning team don’t do their work properly, then the production teams are sunk.
So, we started an epic shopping trip with the idea that I wanted to change how planning worked. I wanted to get our heads out of the granularity of everything that we were doing day-to-day and push us forward into leading conversations about how we do the work that we needed to get done so that we would be setting strategy for how our aircraft operate not just putting things into work orders and making sure they’re in the shop on time.
On that basis, we decided on some basic requirements that we needed for our next generation, industry leading, heavy maintenance planning software. In the beginning it was simple; no blocks and automated scheduling production with automated reporting; we didn’t want manual tallies or inputs, it all had to be automated. Second was scenarios; we wanted to be able to see options and to be able to show people the consequences of decisions they were making. We wanted to understand how a program is going to work and evolve over time and where we’re going to have work where it makes sense for us to have work. We need to be able to do this quickly and to show the difference between all of the scenarios and to be able to rapidly get that over to people who really don’t want to give us the time of day.
Ease of schedule publication
The next part was ease of schedule publication. This is still something that we struggle with today; trying to get out that big picture of all of the schedule options we have but making them make sense to people so that they can use that information as the basis for decisions.
This is for an audience that goes from material groups all the way up to senior VPs and finance, and our exec crews, for them to have great ideas that are going to help us. We have to be able to talk hyper-technical on one side and then high enough detail where we can get non-technical people on board with us on the other side.
Interface with the M&E system
The next basic requirement was that we wanted to make this easy on ourselves, to be able to interface with our M&E system which, for JetBlue, is TRAX. We wanted to ease the burden of washing information from one system to the next, back and forth, which was something we were concerned about at the time as we were looking for another third party to handle our schedule. We took this another step and added the things that I called the great ideas. So, those basic requirements would give us an automated schedule but it was not going to be industry leading, next generation at that stage; it was going to have that potential but not be there yet at that time.
Schedule optimization
The next thing we started to look for was schedule optimization. Those who work in planning will know, especially if they work with contractors, that a schedule that optimizes for cost will probably look very different from a schedule that optimizes for days out of service; the question is, which one is better and how do you evaluate that? One of the things that airlines struggle with, especially on the tech ops side, is how to identify opportunity costs. Being able to show a schedule that optimizes only for cost value versus a schedule that optimize for days out of service was a step in the direction of simplifying the job of identifying an opportunity cost. The question is, where do we want to place the value? Is it in time or is it in the money or some combination of both? Or is there another factor that we want to optimize for? How do we want to handle all of this stuff?
At the time, we were starting to work towards using our own data. Having been a start-up in 2000, JetBlue was responsible for the maintenance program and how it was worked, and we’d finally amassed the data set to be able to start pushing our program to work for JetBlue based on our own data. This is particularly important for JetBlue because, excluding the pandemic, we have industry leading aircraft utilization. The basic schedule in the maintenance program that comes from the OEM, really didn’t fit for JetBlue. I was doing checks on average six to eight months ahead of the rest of the industry because the utilization rate was forcing it. However, that didn’t necessarily mean that the aircraft were indicating that the work needed to done. On the other side, there were times when the aircraft were indicating that work really needed to be done. The challenge was how to balance out the program, how to step away from the basic black check methodology with which everybody is most familiar and incorporate our real experience into the scheduling system in order to have a program that works for JetBlue? To be able to do that, we needed a complete forecasting template.
Any one of our aircraft today will have from between 1400 and 1800 individual tasks running on them on any given day and the planners go through all of those to group them up into A checks, B checks, C checks, 75,000 hours services… things like that, to help us manage those tasks so that we don’t have to look at every single one of those 1,500 or so tasks every day. But even then, pulling those groups together is a significant amount of work and making sure that they line up and repeat on the basis that we want, so that we can leverage each opportunity in the way that works best for us, takes a lot of skill and time. If our industry-leading, next generation heavy maintenance software could help us to make that happen, that was something that we wanted to investigate further.
The last step and the most tedious aspect of planning is work order generation; what could we do with that? So, we started a development project with somebody else who said that they could do all of this for us. However, two years and countless bugs later it crashed. It was intensely painful for JetBlue to have lost all of that time and effort, and have to start over. But that’s what it was.
JET BLUE AND AERROS FROM AEROSTRAT
We not only had to start shopping again but there were also a few leadership changes at the time. Then Aerostrat came into the frame with a solution that was ready. We’d had a lot of conversations during that time with other groups explaining what we’d done, where we’d been and where we could go. In this, they all broke into two main groups. One was ‘the systems that are set-up are for black check methodology, repeating C checks for ever’, while the other groups were those in development and, following our previous experience, that was not something JetBlue wanted to repeat. Also, the vendors offering black check methodology were saying that, that is now the OEMs work and they could set it up or us within a week which seemed a bit too quick.
Aerostrat came in somewhere in the middle: they were beyond development, they had a product that we’d be able to implement and work forward with right away but they also had the flexibility and the willingness to talk about all the work that we had done, what we had at the time and where we wanted to go into the future. So, we opted to work with Aerostrat.
The research and decision process started in 2019 and went into early 2020 which is when we decided to implement Aerros in JetBlue. All readers will be aware of what happened in 2020 and things quickly got intense. Although implementation could have been easier, we opted to go through through numerous scenarios during the pandemic as well as numerous datasets, working with Aerostrat to get the information in to the system. Partly because of our previous experience, we did run 2020 schedules concurrent through Aerostrat at the same time until we were confident that we were going to be OK. With the benefit of hindsight, it is clear that was unnecessary; once we had the data set together and once it started working, it would have been fine. With tremendous support from Aerostrat, we got there, we know exactly how it all works and in 2021, we proceeded with the brand-new schedule.
This was a difficult time to change manage something this big. Our teams had been seeing the same style of maintenance schedule, the same style of tallies for that information in the heavy maintenance schedule since 2004. And I had been very accommodating over the years to make sure that they got all of the data that they wanted in the way that they wanted it. But now we had a new system that looked different, had different nomenclature, the way things worked was different and everybody was distracted by events in the wider world at the time when we were making that change. While we were confident on the tech side and on the planning side, the rest of the organization was not. So, implementation was more challenging for us because everything looked different and felt different and nobody wanted to make time to learn anything; it all felt hard.
We actually got buy-in from our stakeholders starting with internal and tech ops first with scenarios showing the options. We were successful, when everyone was thinking that because we weren’t flying their aircraft, they didn’t have to do heavy checks, we realized that we had to do heavy checks or we’d pile up a mountain of work that we’d be unable to climb over after the pandemic. Showing scenarios, showing different options, actually showing everybody that if we just stopped the heavy checks throughout the time of the pandemic, what we would need when we wanted to fly again. That realization jump-started acceptance.
And then there was the final thing, the big thing, the overall view. This really got us over the hurdle with everybody during the pandemic; they could visually see the health of our schedule, accounting for time remaining on things just by looking at the picture. That made all the difference for us. We chipped away over time and got tremendous support and we gave people options so that they could understand that they were going to get the information that they needed and they were going to be involved in conversations to make sure that their interests were accounted for in the schedule and then overall we could also evaluate, again pictorially, via the rainbow, how well or not well this was working for us now and in the future.
JETBLUE AND AERROS TODAY AND TOMORROW
Today, things have changed: our stakeholder input has become much more dynamic than it was in the past, and we have different stakeholders now than we did then – these days, pilots offer opinions on the subject.
Stakeholder input
Fleet strategy has definitely become a function where, instead of that being an input to us, we work options with our treasury group and finance team, as to what is the best strategy for how we handle these aircraft as it impacts on heavy maintenance costs over time. As stated above, JetBlue leads the industry in utilization and it’s better than ever now that we have been able to show what is the impact of that industry-leading utilization. It’s not just technicians being tired, pushing on the overnights and relying too heavily on the heavy maintenance events to act as a re-set. Now there’s a bigger and more dynamic conversation that lets everybody have a stake into how we handle the fleet into the future.
We have also now come into an interesting period where we’re talking about what is the right level of transparency. Our heavy maintenance schedule goes out to about five hundred people who represent about a hundred and twenty different groups covering all aspects of the airline as well as some external stakeholders with our business partners. Not every single person on the distribution needs all the information that we are now capable of putting out but we have to ask what is right them. We don’t want to be holding too much back, we want to be very transparent and put it all out there but that might not be the best competitive decision. We do need to decide what is right for who and how do we handle that; That was the discussion underway at the time of writing.
The other thing that we’ve noticed, on the planning side in particular, is the scenarios of which there are a lot, including for 2024. The challenge is, how do handle the scenarios and how do we get decisions made for them: decision making timeframes do not match the building of scenarios so how do we marry those up? How do we keep the information that our stakeholders are looking at, relevant to today? This is new and an interesting problem to have and is something that we’re actively working through with the Aerostrat team. We’re looking for a continued partnership with Aerostrat into the future looking at things like a how do we merge scenarios. Like ‘these two lines form with this scenario with those two lines for that scenario’ or, this scenario for the rest of 2023 but that scenario for the first six months of 2024. How do we marry those into one to say that this is our new standard and start moving forward from there. Those are the new problems we have and are engaging with Aerostrat to work through.
The other thing that we miss by far the most from our old Excel days is production performance tracking. When things went bad in the old Excel days there would be reds and blacks for delays which everybody could see. What it gave us was an example of a production problem versus a planning problem. How the schedule developed over time and how it all worked out together was visually represented for everybody to see and I really want this back. It’s a high priority for us because it changes how conversations happen. Too often, planners take the blame for problems that are not theirs because they are the ones who out it down on paper for everybody else to see. Showing that difference means that you can have a completely different conversation with your stakeholders. We want that back and Aerostrat are working on it.
The other thing that we could do before is we could also show how everybody else’s great ideas would impact our schedule. So, if there is a check and an interior modification is added to that, we would add a black to that check for the interior modification because the 30-day check will now take 45 days but, with Aerros, we can distinguish 30 days for the check and 15 days for the added work.
We have a concept with our stakeholders that all of our MROs are equipped with everything it takes to build a plane from the ground up and the walls are lined with AMPs who cannot wait to get onto an aircraft and do their work. However, that is not our reality and showing that difference matters to us; showing visually that impact is something we want to be able to do in the future. And then the other thing too, as we have changed our conversation going forward, we need new bridges, we need bridges over to different work groups to help them to seamlessly take in our information and for us to take in back from them, also seamlessly so that we can make decisions faster because that now is our new hold-up. Instead of making a schedule being the hold-up, getting decisions is now our hold-up.
That’s where we’re at today and that’s how the implementation of Aerros has worked for JetBlue and we look forward to continuing that work into the future.
Contributor’s Details
Erin Ritola
After graduating from Vaughn College of Aeronautics and technology in 2006 with a BSc Aviation Maintenance and Aircraft Maintenance Management, Erin joined JetBlue as Maintenance Planner / EO Planner working with the team to ensure that all maintenance tasks were accomplished to FAA standard. In 2009, she was appointed Heavy Maintenance Controller responsible to maintain the Heavy Check Schedule and, in 2015, Erin was appointed Manager Strategic Maintenance Planning at JetBlue.
JetBlue
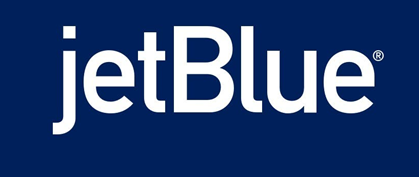
JetBlue operates over 1,000 flights daily and serves 104 domestic and international network destinations in the United States, Canada, Mexico, the Caribbean, Central America, South America, and Europe. JetBlue has codeshare agreements with member airlines of Oneworld, SkyTeam, and Star Alliance. The 285 strong fleet includes Airbus A320 and A321 Classic, Long-Range and neo models as well as Airbus A200 and Embraer E190.
Aerostrat
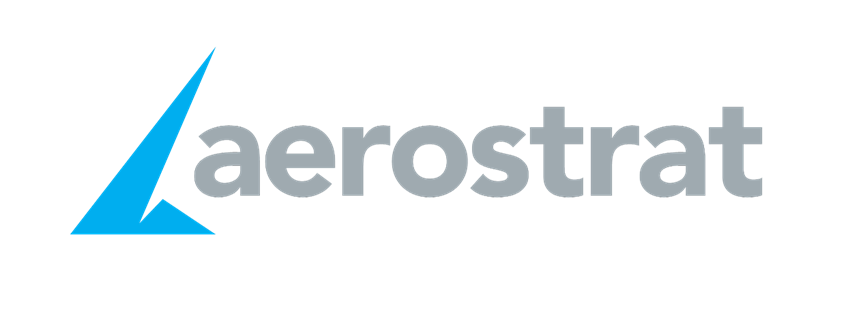
Aerostrat is based in Seattle, WA and offers one product called Aerros, a one-of-a-kind program that manages an airline or MRO’s aircraft maintenance schedule. Aerros enables users to optimize the maintenance program by managing various maintenance and operational constraints, which maximizes event yield, drives costs down, and enables the organization to plan proactively, not reactively. Aerros is also integration-ready and designed to work as an extension of a user’s existing information systems.
Comments (0)
There are currently no comments about this article.
To post a comment, please login or subscribe.