Articles
Name | Author | |
---|---|---|
Solutions In Practice: Bytron | Rod Tinnion, AIS and QA Officer | View article |
Case Study: The value of digitization at Air Hong Kong | Atila Taran, Manager Line Operations, Air Hong Kong and Emil Ahlgren, Sales Manager EMEA, Web Manuals | View article |
EFB should stand for enhanced flight bag – PART 2 | Sébastien Veigneau, President, dgBirds | View article |
Will Trajectory Based Operations (TBO) usher in a new way of working? PART 2 | Michael Bryan, Principal, Closed Loop | View article |
Case Study: The value of digitization at Air Hong Kong
Author: Atila Taran, Manager Line Operations, Air Hong Kong and Emil Ahlgren, Sales Manager EMEA, Web Manuals
Subscribe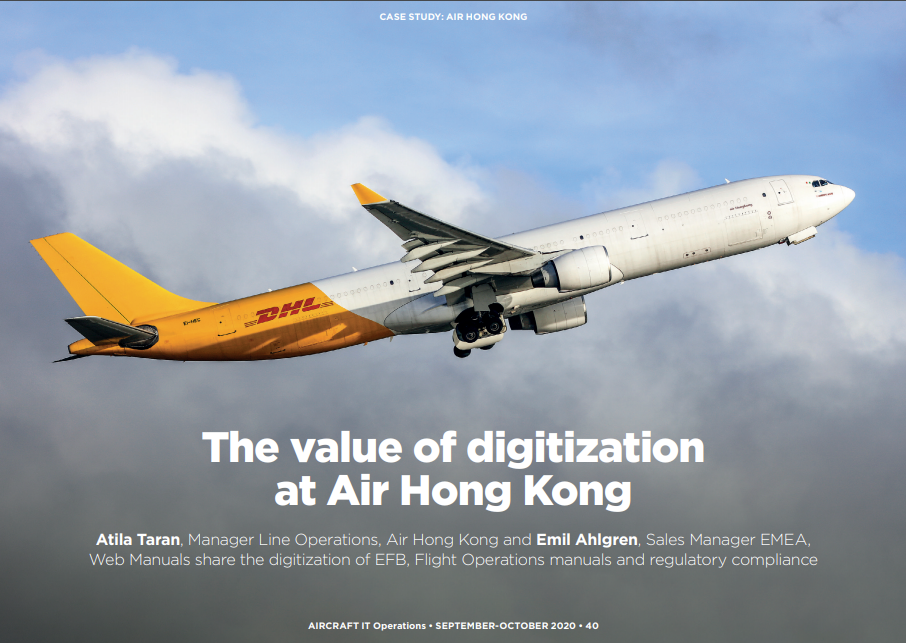
Atila Taran, Manager Line Operations, Air Hong Kong and Emil Ahlgren, Sales Manager EMEA, Web Manuals share the digitization of EFB, Flight Operations manuals and regulatory compliance.
Air Hong Kong is a small cargo business founded in 1986 in Hong Kong. The business has, in recent years, gone through a number of transformations including being bought by Stanly Ho, the ‘Casino King’ before, in 2002, being acquired by Cathay Pacific. At the end of 2002, DHL bought 40 percent of the business, rebranded Air Hong Kong and signed a fifteen year joint venture agreement. The airline started with a freighter version of the Boeing 707 and then a small fleet of Boeing 747-F types, the last of which was retired in 2018. The fleet now consists of ten Airbus A300-600F and A330-300 types mainly operated for DHL Aviation but with a couple operated by ASL Airlines Ireland. Air Hong Kong serves thirteen major cities in Asia from the Hong Kong hub carrying mainly DHL Express cargo and a little general cargo. This is the network (figure 1).
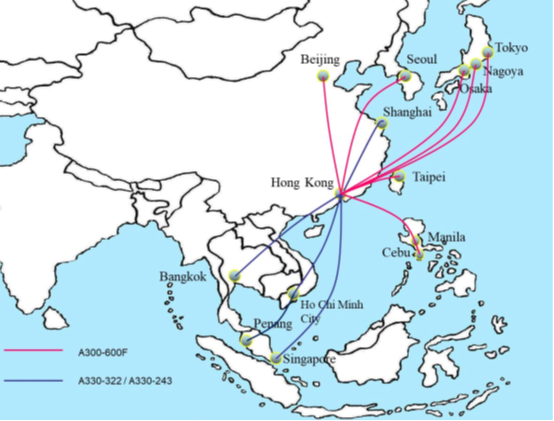
Figure 1
THE PAPERLESS JOURNEY
And now to the main purpose of this article which is to share the journey to paperless operation for Air Hong Kong. Atila first heard about the EFB (Electronic Flight Bag) in 2009 at an Aircraft Commerce conference in Bangkok and found it so exciting a concept that he went back, reported on the development to the DFO (Director Flight Operations) and COO (Chief Operating Officer), proposing that Air Hong Kong adopt EFB technology to which they agreed but asked for a business case. The challenge was how to make a business case? Atila researched business case techniques and made a case for category 2 EFB for Air Hong Kong. But after all the studies, research and so on, the project had to stop as it was too expensive. Air Hong Kong is a small operator with a simple operation with no cabin crew, not even a dispatch function – pilots dispatch themselves. However, Atila was not discouraged and continued attending Aircraft Commerce conferences and learning about EFB until 2015 when the tablet was introduced for use in the EFB environment so that EFB could be installed on an iPad, Samsung Tablet or Microsoft Surface.
With this change, the EFB project was restarted and, in 2016, all Air Hong Kong pilots were given iPads. For two years, they were looking for applications and the right mounting for the aircraft then, in early 2018, the airline started an EFB trial. At the start of 2019, approval was granted by the Hong Kong CAD (Civil Aviation Department) for Air Hong Kong’s EFB using Navblue eChart as the chart type B software and Web Manuals for the manual.
However, the journey did not end there, as the EFB solution (figure 2) shows.
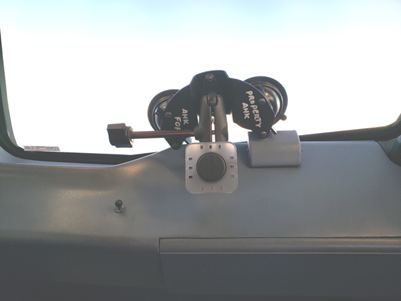
Figure 2
It’s very simple with RAM suction cups and Pivot cover, a simple solution but it does the job. Figure 3 shows the next project at Air Hong Kong which is EFF (Electronic Flight Folder) with an in-house Cathay Pacific application which has also been approved and which pilots at Cathay Dragon are already using: it will next be adopted for Air Hong Kong following a trial in early 2020 and, if approved, Air Hong Kong will start using the application. It basically digitalizes all flight plans, NOTAM and weather.
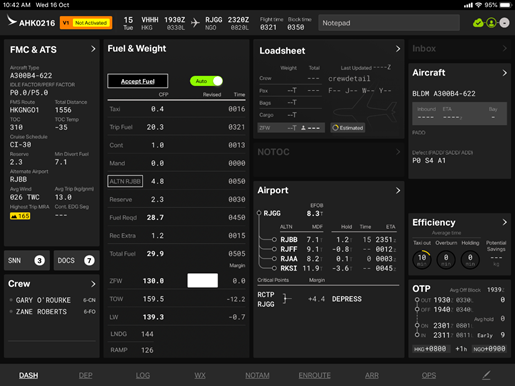
Figure 3
After the EFF project, the next project will be the eTech Log (ETL/ELB). There is still some way to go on Air Hong Kong’s journey to digitalization but hopefully, by the end of 2020, the airline will be completely paperless.
WORKING WITH THE DIGITAL MANUAL
In figure 4 is Air Hong Kong’s old system for managing manuals, working with paper; as readers will know, it generates a lot of work and can take up to a month to revise a paper manual.
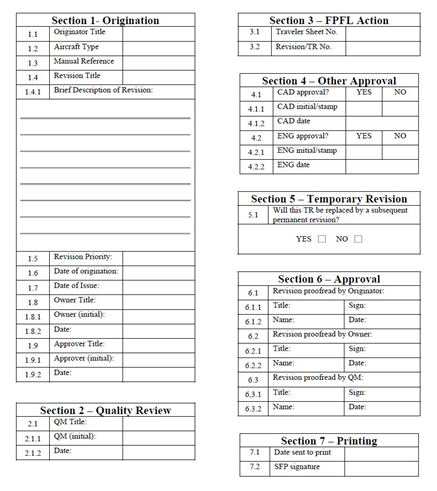
Figure 4
The revisions need first to be recorded and those notes handed to Publications who, in turn, will draft them into a revised copy and return that, in the case of Air Hong Kong, to Atila who will make further adjustments, send them back for re-drafting and to be returned again… Then each changed part of the manual has to be seen by the departments that it affects and they’ll come back with more corrections. It’s a lengthy process and, because of this, Air Hong Kong would often hold a number of revisions until there was enough material to make a more complete manual update.
Using Web Manuals, this process has been cut to three or four days with the owners of a manual able to go to the system right away and themselves change the content within the manuals; and that is all that needs to be done. The rest is completed automatically by the system with all the appropriate notations included to ensure that the right revision is automatically replicated wherever and in whatever manuals it is applicable. Then, after the originator has completed the change, they’ll put the document into review; the reviewer will be notified and can go to the system to review the changes right away. Following the review, the reviewer will release the document to the final proofer, who will proof it, approve it and clear it for publication. It’s a very simple system: once the manual owner has clearance from the proofer, they can press the publish button and, within minutes, all pilots will receive notifications by email and can read the changed copy and content there and then.
WORKING WITH IOSA (IATA OPERATIONAL SAFETY AUDIT)
Air Hong Kong has probably gone through five IOSAs so far. In the past, to deal with the IOSA Auditor, it would be necessary to have a table covered with documents, paper and books; then, to open the manuals one at a time which was very time consuming. And sometimes when the auditor asked for something not on the airline’s checklist, it was quite a job to find the requested information in the manuals. But, with Web Manuals, everything is automatic. So for the last IOSA at air Hong Kong, Atila only had to have a screen in front of him with the Web Manuals Compliance Library to simply use links to those parts that had to be shown to the auditor. As they went through the ISARPS (IOSA Standards And Recommended Practices) they only had to click on the relevant link to bring up the right screen. There is no paper anymore and the process is very efficient and fast.
THE CHALLENGE OF STAYING COMPLIANT
Compliance is something that arises daily in our sector. Here, we want to share with readers not only an understanding of that challenge but also the challenge of using inefficient tools leading, in the end, to qualified people doing unqualified things. So we just want to talk about the journey, the revision process that arises every day and traditionally looks rather like this (figure 5).
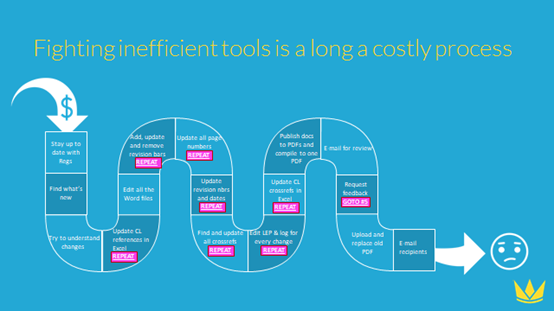
Figure 5
The first thing is that you need to stay up-to-date with the latest published regulations by going to websites and other sources to see what has changed and/or is new compared to the old version in order that you can understand what that change entails. With that knowledge, you’ll update the compliance reference list in Excel to make sure that you have the right information according to what has changed or been added. The next stage is to undertake all the editing in Word, a lot of manual work to ensure that the structure is correct and being sure to update the revision bars and the revision number, and the revision dates. This is something that is done, of course, recurrently, depending on how many updates you do. Then after the updates have been done it is also important to remember the cross-references, the links to the other documents that will be affected by the change – usually using a manual list to keep track. Next is to edit all the affected pages, table contents, the Change Log and list of affected pages. Make the changes and also update the Revision Bars once again. Publish the PDF is the next job and to update the cross references to the documents to complete the compliance linking.
Before publishing the documents or generating the PDF, depending whether each chapter is in a stand-alone file, it has to all be emailed for review. Hopefully the reviewer will open and review the document and offer feedback, as requested by the compiler, which might, in turn, mean returning to the Word files to re-edit them followed by the whole content updating process, making all the updates, removing the Revision Bars and setting up new ones. That’s all before continuing once more through the rest of the journey, everything mentioned above, to hopefully be able to replace the old manual with the revised one before sending an email to all recipients saying ‘here is a new revision that you need to check out’ which, hopefully, they will do. This is a journey that Web Manuals hears about every day: it is what we mean when we talk about the challenge of bad tools.
Some of the more common challenges that get brought to Web Manuals’ attention from operators before they become Web Manuals users are listed in figure 6.
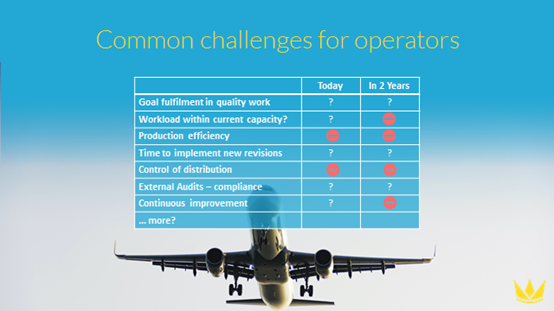
Figure 6
We need also to keep in mind, ‘where are we today and where will we be in two years’ time?’ Maybe ‘goal fulfilment in quality work’ is something we can deal with today but, again, what will it look like in two years’ time? The ‘workload within current capacity’ might be OK today but companies always strive to grow and do better so, once more, what will it look like in two years? And do we need to plan for that? For the implementation times on new revisions: we have suggested that a month is what it takes using traditional tools and processes. Maybe that’s OK today but, yet again, how will we judge it in two years. These are some of the challenges that we hear a lot about. We should try to ensure that qualified people do not spend their valuable time doing unqualified work such as updating revision bars and changes to manuals but that they rather do the qualified work for which they have been hired.
Comments (0)
There are currently no comments about this article.
To post a comment, please login or subscribe.