Articles
Name | Author | |
---|---|---|
CASE STUDY: Transavia Netherlands upgrades to the latest MRO IT solution | Gerard de Bruyn, Product Owner of the technical department, Transavia Netherlands | View article |
CASE STUDY: Canadian North took control of its device fleet | Gail Campbell, Senior Manager Maintenance Information Systems, Canadian North | View article |
CASE STUDY: Affinity reaps the benefits of a new IT solution. | Grahaeme Colledge, Technical Director at Affinity Flying Training Services, and Tim Alden, Strategic Partnerships Director at Veryon | View article |
WHITE PAPER: A step into the future for an MRO software solution | Andrew O’Connor, Head of Product Management, Aviation and Paul Lynch, Group Managing Director, Aviation, both at Aspire Software | View article |
WHITE PAPER: AI is Powering Growth of Lifecycle Optimization Tools | Dr Ip-Shing Fan, John Maggiore and Professor Anna Smallwood, all at Cranfield University | View article |
WHITE PAPER: Gains for MRO from digital solutions | Remon Sweers, VP of Products, QOCO systems | View article |
CASE STUDY: Transavia Netherlands upgrades to the latest MRO IT solution
Author: Gerard de Bruyn, Product Owner of the technical department, Transavia Netherlands
Subscribe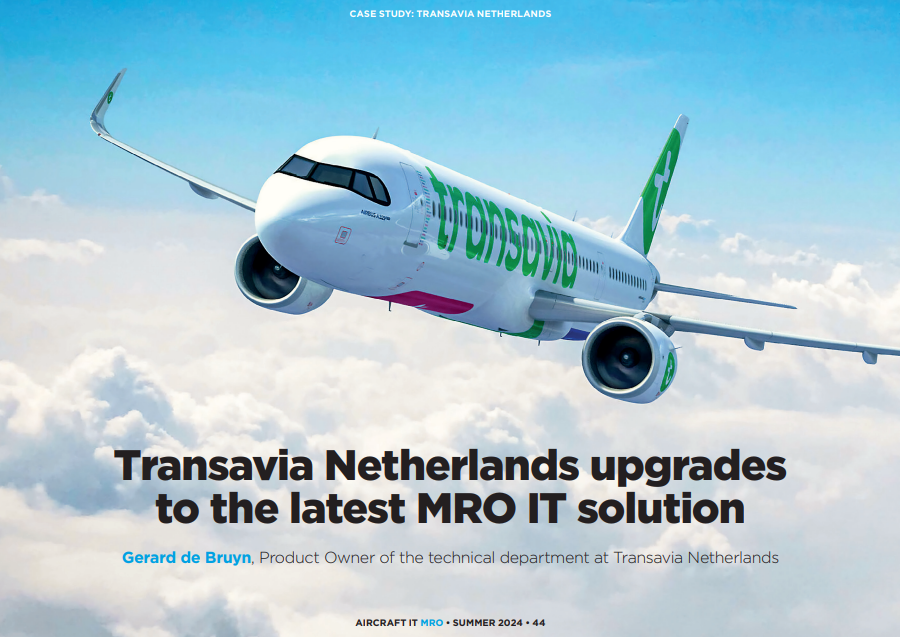
Gerard de Bruyn, Product Owner of the technical department at Transavia Netherlands
In this case study, I want to tell you about Transavia Netherland’s experience with TRAX eMobility; why we decided to adopt it, how the implementation went and what we have gained from our new solution and apps. We’ll look at what was the goal of the project, how we approached the change, the challenges encountered along the way, the progress we have made and the lessons that have been learned. We’ll then take a quick look into the future plans for the solution in Transavia Netherlands. However, before any of that, I’ll introduce the airline in which the case study happened.
TRANSAVIA NETHERLANDS
Launching in 1965 as a Dutch charter airline, Transavia has seen a lot of changes over the almost 60 years since then (figure 1).
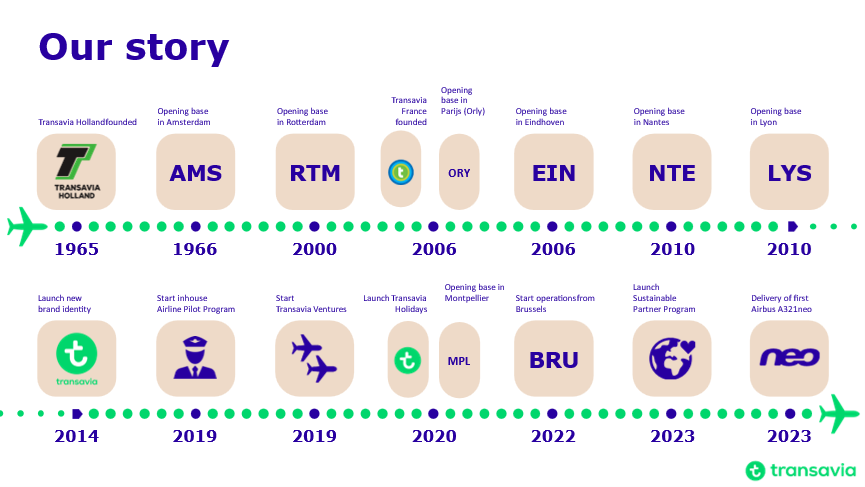
Figure 1
Early in the twenty-first century, we adopted a low-cost airline model and expanded with our sister company in France in 2007. The most recent big change for Transavia is that we decided to switch our fleet from all Boeing aircraft to fully Airbus A320neo family aircraft.
Here are a few statistics from our business; in 2023, we flew more than 22 million passengers on 135,000 flights to more than 160 destinations, mainly in Southern Europe. At the time of writing, our fleet was 128 aircraft strong and still predominantly Boeing 737s (figure 2).
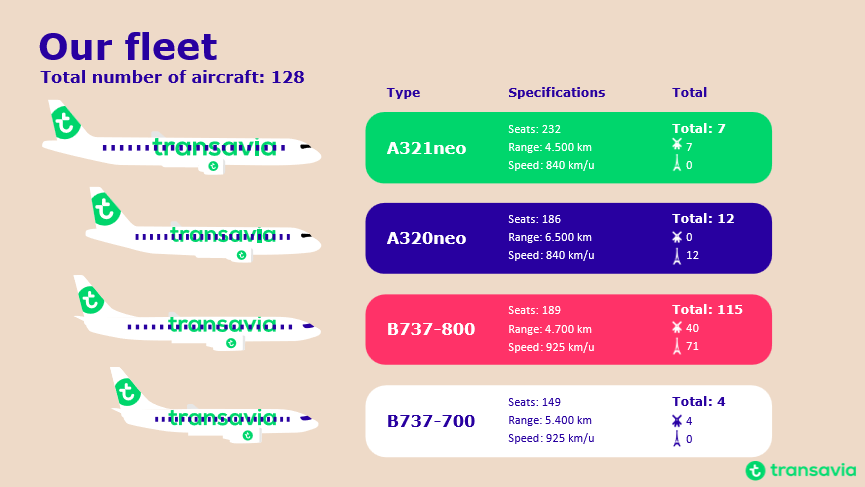
Figure 2
In the Netherlands, we still had four 737-700s as well as 40 of the B737-800. However, we had started introducing the Airbus A321neo at Amsterdam and A320neo at Orly. At the end of 2023, there were seven A321neos in Amsterdam and 12 A320neos in Orly. This will be a big change for us and will mean a mixed fleet for the next seven years until we have a full Airbus fleet by the end of 2031.
Transavia Netherlands is the smaller of the two Transavia airlines but, in the Netherlands, we are the number two airline overall, second to our parent airline KLM, and, in the low-cost market, we are the largest (figure 3).
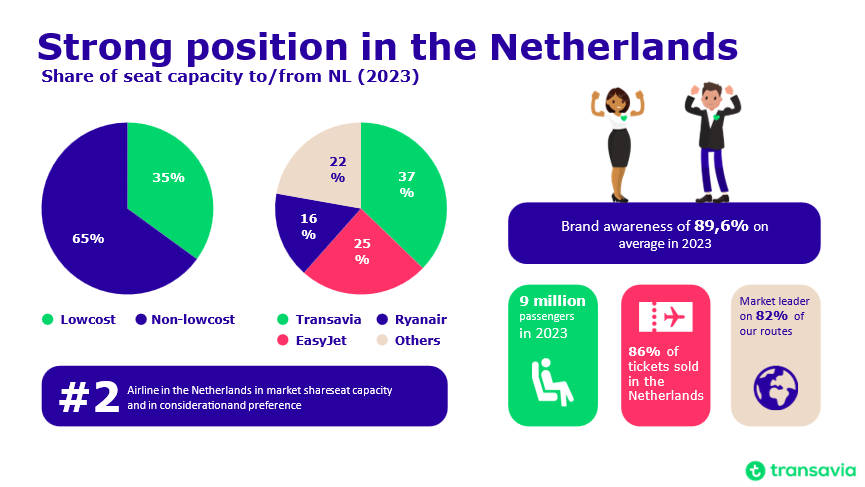
Figure 3
Our brand awareness in the Netherlands is almost 90 percent and we are the market leader on 82 percent of the routes we serve. From the early days of Transavia which were 100 percent charter, the airline has evolved to the low-cost airline of today with charters only accounting for three percent of operations at the time of writing (figure 4)
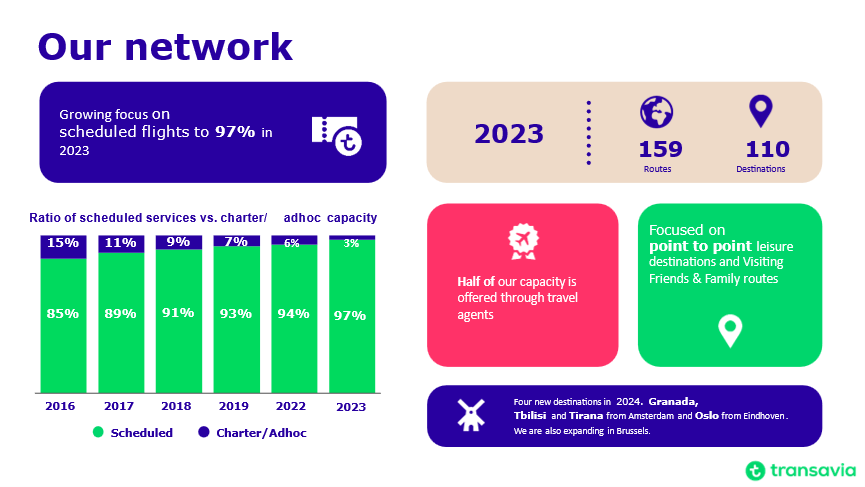
Figure 4
GOALS
As with any project, we set some important goals for this one. First of all, there were the challenges that we had within MRO operations which included a shortage of technicians, something with which readers will be familiar. A lot of experienced people are retiring but fewer new recruits are joining as aircraft technicians. Another challenge is the EU ‘Denied boarding compensation’ (regulation 261/20004)’ which will cost us a lot of money should we have a three-hour delay or more. And, especially on Amsterdam, Schiphol, airport it’s pretty crowded and travel time to and from a ramp can take up to 15 or 20 minutes. Also, in the past, it used to take about half-an-hour to get the right paperwork to the aircraft so our goal, in this respect, was to have the technicians enabled with the right information at the right time to support the right decisions. That will improve the efficiency of the technicians as well as reducing the need for verbal communications. The process before was very cumbersome; the technician had to call the shift leader to report an AOG situation, the shift leader would then report it to Maintenance Control and Maintenance Control would report it to Operations. It all took time and the verbal process often meant that the story had changed by the time it reached Operations. Ultimately, we wanted to become paperless, introducing QuickTurn and Line Control from TRAX is the first step of setting up the paperless process.
APPROACH
For the approach, we defined three phases. Quickturn and Line Control were implemented in the first phase because we felt that would deliver a benefit for technicians from the beginning and with less investment. The second part was already underway at the time of writing to include the implementation of AeroDox, Production Control and TaskControl. AeroDox was implemented as part of the entry into service (EIS) to provide our technicians with Airbus documents, with offline capability on their iPads. The third phase is PilotLog and CabinLog but, at the time of writing, no decision had yet been taken to introduce them in Transavia Netherlands – they have already been introduced in Transavia France so we hope to have more news on this in the near future.
CHALLENGES
We faced, as already stated, a number of challenges, especially with the entry into service process. There was a lot of pressure within the company to be ready by the due date for delivery of our first aircraft in the new A320neo fleet. First of all, we had to upgrade our TRAX environment because we were still working on a very old version of TRAX which was not capable to work with all the modern technology and capabilities that Airbus have put into their new aircraft and especially with the length of the serial numbers. So, we had to upgrade TRAX plus we also, at the same time, migrated from an On-premises solution to the Cloud version which was a very big project in itself. Another challenge that we faced was the availability of end users, technicians, with the entry into service of the new Airbus aircraft and an operation that was very challenging, especially for the technicians, and with not much time available for testing the new application.
USING THE NEW APPS
There was a challenge to implement flight schedules in the right way and we managed that by using our own middle connector to send out the messages in a form that TRAX could accept; it works perfectly now. We made some adjustments on times that we want to see in the app. We did the integrations via our middle connector and we also switched from Movement Control to iFlight from IBS; so that changed the format for scheduled flights. But all the delays are processed within TRAX and notifications are also sent to the iPads. We’re working on the integration with our rostering tool although there were some technical issues not related to Trax. Those are the main integrations that we’re looking at right now for the most efficient way of using those apps.
PROGRESS OF THE PROJECT
The way we approached the project was that we formed a group of 20 test users who were supplied with a test environment and shown around the application to let them get a feeling for it. From the start it didn’t look as if much had changed in the processes but, in the end, it did turn out to be a big change for them. There was also the parallel Cloud migration which included some very strict deadlines and the need to take account of the availability of TRAX’s resources. Notwithstanding those deadlines and constraints, we managed to go-live technically in August 2023. That was to fit in with the availability of resources at TRAX and we had to promote it to Production in August; then, we had an October go-live for the aircraft technicians.
Because August was in the middle of the holiday season, a very busy time for Transavia Netherlands, we extended the pilot change-over to a later time which would be more suitable for the end users to be ready. That meant that we started pilot usage in October 2023 followed by a full go-live in January 2024. For all of those reasons, we had a soft go-live; all the technicians were trained team by team and as each team completed their training, they were able to use the application. Overall, we have received lots of very good support from TRAX in using the new apps and, especially for Production control and TaskControl, they ran sessions on how to use the app; my team of application engineers are very well trained in how to set-up the process and super-users are involved to embed the processes into our organization.
LESSONS LEARNED
Overall, the project itself turned out to be quite a challenge, especially engaging the end users and the aircraft technicians. One lesson that we learned was that we hadn’t set up a process, ahead of the implementation, to ensure that technicians had clarity on how to use the applications. We did a lot of training and a lot of hands-on experience but the initial adoption by end users could have been better; many of our people had a lot of experience as we had been working with TRAX, in one way, for the past 15 years. Now, we were telling technicians that they could use it in another way which would be more efficient and would help them in having the data available. However, at the beginning, people seemed to prefer the old and familiar way of doing things and it was hard to convince them to change to the new way.
At first, there was a very low adoption rate but users are increasing as they see the benefits of the change in their daily work lives. That change management was the hardest struggle we encountered. We measured the adoption rate largely by how the technicians reacted, not by logging in rates but by floor walking. The technicians were complaining that the app didn’t work and so we asked whether they had logged in and, of course, they hadn’t done so. Everybody expects a perfect solution but it doesn’t always work as users might first have expected it to work. We continue to listen to the end users and try to resolve the issues that they report; we stay in contact with them and stay in contact with TRAX to improve the apps because, in the end, we all want a perfect solution for our technicians.
Linked to all of that, the final lesson that we learned was, don’t try to change too much at once. Together with the entry into service of a new aircraft type and the upgrade of the TRAX solution to the Cloud as well as the implementation of the apps, everyone at Transavia Netherlands was faced with a little too much pressure. It would have been sensible to have lifted our foot off the pedal a bit to help people to adapt to the new situation; be aware that we have a new aircraft type and that there are new tools to support those aircraft but allow the time to evolve to the use of the new apps. We started with small processes for QuickTurn, just creating defects, making sure it was searching the defects. And, for Line Control, we started with assigning the flights so that the technician is aware of the flights they are assigned to and the changes in those flights. That will help us in getting rid of all the manual processes that are still in Excel.
BENEFITS
The main benefit is employee experience; helping technicians’ development and making their lives easier will improve the employee experience. Rather than using the system to reduce the number of technicians, our objective is always to use it to reduce the pressure and enable people to work better. Every year we conduct surveys on the pressure experienced by our technicians in order to ensure that it can be reduced and improve safety. Given the shortage of qualified aircraft technicians and engineers on the market, it should make us a more attractive company to work for. It’s very important to listen to our employees but also, if the technicians have the ability to make the right decisions at the aircraft instead of having to return to the office, we can avoid long delays, up to three hours sometimes, which, at Schiphol, can cost €120,000 in compensation costs. If we can prevent one delay, there will already be a benefit.
LOOKING FORWARD
Looking to the future, the implementation of AeroDox went fairly smoothly and didn’t require a major program; we were able to do it with very little disruption. It was a change in the processes but it’s just an eReader app with which we are able to host the Airbus documentation offline. We’re now planning for phase 2 and we have decided on a totally different approach, first setting up the processes upfront. Also, the changes on TaskControl and Production Control are much broader than QuickTurn and Line Control. So, we’re setting up those processes as TRAX designed them and testing with a small group of end-users. Then it will be extended to certain projects, like A-check for one particular aircraft, to get feedback from users and to make some adjustments in the processes. That is the big difference that we have made in the approach for Production Control and TaskControl.
Not for QuickTurn and Line Control but for Production Control and TaskControl, we are setting up the process for electronic signatures at task card level and the next step will be giving a CRS (Certificate for Release to Service) on work packages but that involves a lot of electronic certificates which will require further investigation The first step of Production Control and TaskControl will be an electronic signature approved by our regulators.
We hope soon to make a decision on phase 3 so that we can start implementing with the cockpit and cabin crew for having a seamless flow of aircraft maintenance from reporting to resolving and releasing the aircraft.
That has been our experience at Transavia Netherlands in upgrading our MRO IT solution and moving our processes to Cloud and mobile. I hope that it will be useful information for others planning to embark on a similar project.
Comments (0)
There are currently no comments about this article.
To post a comment, please login or subscribe.