Articles
Name | Author | |
---|---|---|
Meet the IntelligentEngine; taking predictive engine maintenance to the next level | James Elliott, Principal Business Architect, Aerospace & Defence, IFS | View article |
Cargolux & TRAX eMOBILITY Q&A | Stephane Kastler, Director of Maintenance & Production, Cargolux | View article |
Vistair brings it all together at Viva Air | Captain David Restrepo, Flight Standards and Training Manager at Viva Air Colombia | View article |
Right person, right qualifications, right place at Lufthansa Technik | Luca Jelic, Training and Quality specialist at Lufthansa Technik’s Base Maintenance Division | Andres del Pino, CEO, StaffNow | Svetla Stoeva, Former Head of Staff Agency at Lufthansa Technik Base Maintenance | View article |
Meet the IntelligentEngine; taking predictive engine maintenance to the next level
Author: James Elliott, Principal Business Architect, Aerospace & Defence, IFS
SubscribeJames Elliott, Principal Business Architect, Aerospace & Defence, IFS explains the value of linking usage data and engineering forecasts through the digital Blue Data Thread.
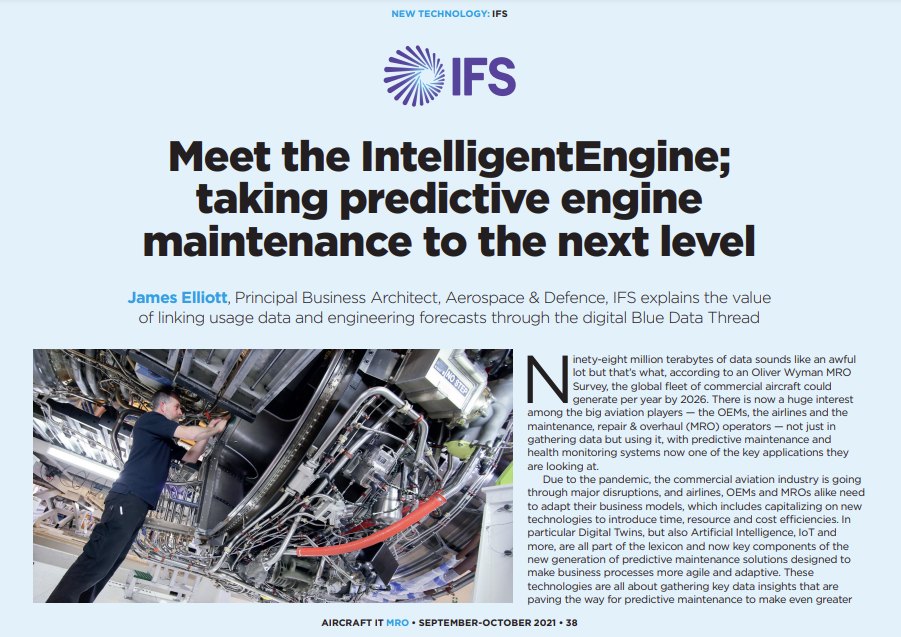
Ninety-eight million terabytes of data sounds like an awful lot but that’s what, according to an Oliver Wyman MRO Survey, the global fleet of commercial aircraft could generate per year by 2026. There is now a huge interest among the big aviation players – the OEMs, the airlines and the maintenance, repair & overhaul (MRO) operators – not just in gathering data but using it, with predictive maintenance and health monitoring systems now one of the key applications they are looking at.
Due to the pandemic, the commercial aviation industry is going through major disruptions, and airlines, OEMs and MROs alike need to adapt their business models, which includes capitalizing on new technologies to introduce time, resource and cost efficiencies. In particular Digital Twins, but also Artificial Intelligence, IoT and more, are all part of the lexicon and now key components of the new generation of predictive maintenance solutions designed to make business processes more agile and adaptive. These technologies are all about gathering key data insights that are paving the way for predictive maintenance to make even greater strides in the coming years. Thanks to these digital developments, the often risk-averse aviation industry has pivoted to trusting predictive maintenance not only to increase performance and reduce costs, but to better manage risk and enhance safety.
FAST-FORWARD TO THE ROLLS-ROYCE DIGITAL BLUE DATA THREAD – MEET THE INTELLIGENTENGINE
Predictive maintenance as a term isn’t new – as far back as the 1990s, the IFS Maintenix team at IFS has worked with the US Navy to crunch through engine health monitoring data to model and predict the failure of engine components. Accelerate to 2020, and today Rolls-Royce is using AI forecasting, supported by IFS, to help airline customers to automatically update predicted maintenance deadlines for every life-limited component inside their engines—a key part of the Rolls-Royce Blue Data Thread strategy, a digital information thread connecting every Rolls-Royce powered aircraft, every airline operation, every maintenance shop and every factory.
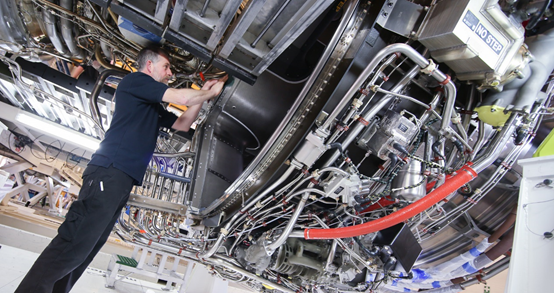
This is all part of the Rolls-Royce vision for the IntelligentEngine which is, “a form of cyber-physical service where the physical engine, the services that surround that digital engine and the Rolls-Royce digital capability are indivisible,” explains Nick Ward, VP Digital Systems, Rolls-Royce “The IntelligentEngine forms a digital twin of a physical engine, with both connected by data. It is contextually aware of its own operating conditions, the environment it’s flying in, the rest of the fleet it is part of and it is consolidating that information to make smart decisions to maximize availability, while minimizing maintenance costs and disruption.”
DATA INSIGHTS FLOW DOWNSTREAM TO AIRLINES AND THEIR PASSENGERS
The benefits of this approach are huge in terms of aircraft availability and engine time on wing, which in turn should translate into fewer delays, an improved moment of service with more satisfied passengers and bottom-line boosts. One of the main causes of aircraft on ground (AOG) delays is unplanned maintenance operations. US Bureau of Transportation statistics show in the last full year of uninterrupted airline operations, 2019, US airlines reported 302 domestic tarmac delays longer than three hours, compared with 202 in 2018 and 193 in 2017.
Rolls-Royce has a fundamental mission that every Rolls-Royce powered aircraft flies on time, every time with an availability as close as possible to 100%. That works for the airlines that own the aircraft, Rolls-Royce as the OEM and passengers themselves. This is where the confluence of predictive maintenance incentives comes together for all parties involved in flying any given route.
“The Blue Data Thread contributes significantly to Rolls-Royce’s strategies to eliminate unplanned failures,” says Nick Ward. “A jet engine is an incredibly complex example of high-engineering but being in-tune with the specific maintenance requirements and performance allows Rolls-Royce to accomplish feats like powering an A330 to fly the equivalence of to the moon and back 50 times between overhauls.”
GOING FROM PHYSICAL TO DIGITAL – MAXIMISING THE POWER OF THE DIGITAL THREAD
Unlike some other OEM predictive maintenance initiatives, the Rolls-Royce Blue Data Thread is a two-way movement of data. The engine supplier is collecting data from multiple sources, such as engine health monitoring and information from airline maintenance management systems, contextual real time engine flying condition and other data sources including MRO data from Rolls-Royce engine facilities.
This is where IFS has provided strategic support on multiple levels. IFS Maintenix has automated the sharing of the data critical for Rolls-Royce to re-life its engine parts, but also took a broader scope to allow airlines and Rolls-Royce to collaborate and share much more information about the work which happens on their engines: for example, which engine parts have been switched or inspected and even if any other aircraft systems have been impacted by engine behavior. The result of this two-way exchange is an even more complete picture of engine performance; a higher resolution digital twin and a way to deliver these digital insights to improve physical part use while in-service.
AIRLINES REALISE MORE BENEFITS THAN THEY BARGAINED FOR – DAY TO DAY IMPROVEMENTS AND SUSTAINABILITY BOOST
Participating airlines were confidently expecting to see certain results from the IntelligentEngine and the Blue Data Thread initiatives in terms of overall engine performance and cost. However, what perhaps wasn’t anticipated was the weaving of new predictive maintenance results non-intrusively into day-to-day processes.
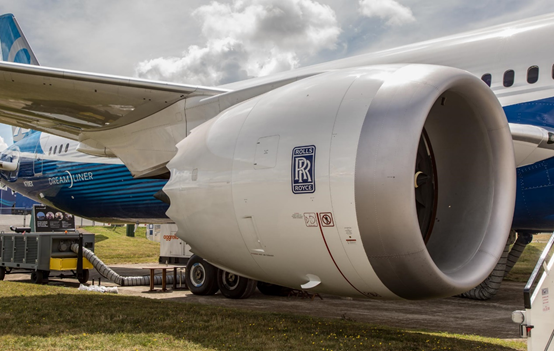
“A Rolls-Royce Trent engine can, on average, fly around the world over 1,000 times between significant engine events. Through multi-variable forecasting, IFS is able to map the data on how an airline expects to fly a particular engine and combine it with Rolls-Royce data on expected part life to provide a very accurate predictive maintenance deadline right down to individual part numbers,” continues Ward.
“Previously airlines may have spent weeks trying to piece together updated deadlines, but now accurate maintenance information is presented to airlines on a daily basis and is seamlessly consumed by their maintenance scheduling engine. Initial anecdotal reports show huge progress to extend the lifecycle of engines and components, increasing the time taken to first engine removal by 48 percent.
“When you have this level of monitoring and data exchange, it indicates step change in predictive maintenance. So many engine components and their details are being dynamically monitored that past preventative maintenance approaches are a thing of the past. With this level of tracking, most failures are detected on an individual level before they are likely to occur, well before planned maintenance cycles. Rolls-Royce has extreme faith in its predictive analytics strategy with a goal of zero false predictions and 100% success rate.”
More effective maintenance will also translate into sustainability benefits. As the aviation industry moves towards a greener future, digitalisation and predictive maintenance are important elements for the engineering side of the industry and both IFS and Rolls-Royce have made strong sustainability commitments as part of their long-term business planning. The Blue Data Thread program aligns perfectly with these priorities. By reducing the need for maintenance interventions, part replacements and overhauls, manufacturing use of energy and resources is reduced and the emissions footprint of part and engine logistics is minimized.
GETTING UP AND RUNNING FAST – DATA SHARING A KEY FOCUS AREA
From a technical perspective, airlines can be up and running on the Blue Data Thread through the IFS Maintenix plug-in in a as little as two months. This requires a quick technology installation and is then a case of specifying key modelling information such as engine utilization. It’s the accessibility and sovereignty of data which can bring up potential roadblocks.
Airlines running other maintenance management systems need to make sure they can extract, store and analyze critical data profiles from their supporting software. Some airlines running legacy maintenance software on their aircraft may not be able to provide enough of the data required to feed the Blue Data Thread and a digital twin of their engine. Those airlines that can, may have some data security reservations about certain lines of data, for example details around part leasing and ownership. This is why IFS and Rolls-Royce have designed the ability to give airlines granular controls to manage the level of data lines specific for each airline taking part.
Underpinning the bilateral transfer of data from manufacturer to airline and back again is the need for an interface/dashboard to parse the aggregation of data points. The delta between data and information is the ability to translate raw data into actionable insights and meaningful information.
OPEN THE DOOR TO A PREDICTIVE FUTURE – DATA, DIGITAL TECHNOLOGY AND COLLABORATION
Contributor’s Details
James Elliott
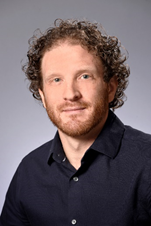
With a wealth of experience spanning the Airline, Defense, OEM, and MRO market verticals, James has worked with aviation organizations on the selection and implementation of next-generation maintenance management IT. He is a noted authority on the impact of technology on maintenance operations as well as the business processes that affect positive change. His work with clients includes the key processes that contribute to the economic management of the maintenance function while respecting operational constraints – both regulatory and commercial.
IFS
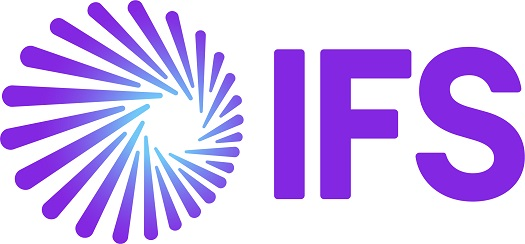
With over 400 Enterprise Asset Management (EAM) or Maintenance Repair & Overhaul (MRO) companies using IFS solutions today, IFS delivers flexible, modular business solutions that manage the entire commercial aviation lifecycle of contracts, projects, MRO, assets and services. IFS offers functionality for contract and project management, risk management, budgeting and forecasting, engineering, material management, sub-contracting, document management, fabrication, service and maintenance management, as well as financials and human resources.
Rolls-Royce
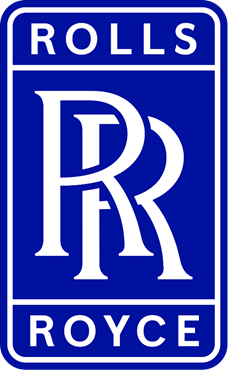
For nearly three decades, the Rolls-Royce family of turbofan aircraft engines have pushed the boundaries of what is possible, as each new model sets new performance benchmarks for civil aviation during more than 100 million flying hours.
Members of the Trent engine family are now in service on the Airbus A330, A340, A350, and A380, as well as the Boeing 777 and 787 Dreamliner.
Comments (0)
There are currently no comments about this article.
To post a comment, please login or subscribe.