Articles
Name | Author | |
---|---|---|
Aviation Maintenance and Covid-19 | Allan Bachan, VP, ICF and Arun Navneethakrishnan, Aviation Solution Adviser, Ramco Systems | View article |
Case Study: Using digital solutions to drive efficiencies at APLUS | Wilfredo E. Regalado, Director Corporate Finance, Strategic Planning and Information Technology, Aviation Partnership Philippines (APLUS) | View article |
Real life essentials in five minute case studies: Recommendations to reduce NFF (No Fault Found) rate | Leandro Correa, Senior Vice President, Seabury Solutions | View article |
Digital processes, e-signatures and ETL/ELB promise better ways of doing business in the post-Covid world | Kirk Strutt, Senior Product Manager, IFS and Dan Dutton, VP, R&D, IFS | View article |
Aircraft IT MRO 2020 survey: COVID-19 and the response of aviation IT developers and vendors | John Hancock, Editor, Aircraft IT MRO | View article |
Real life essentials in five minute case studies: Recommendations to reduce NFF (No Fault Found) rate
Author: Leandro Correa, Senior Vice President, Seabury Solutions
Subscribe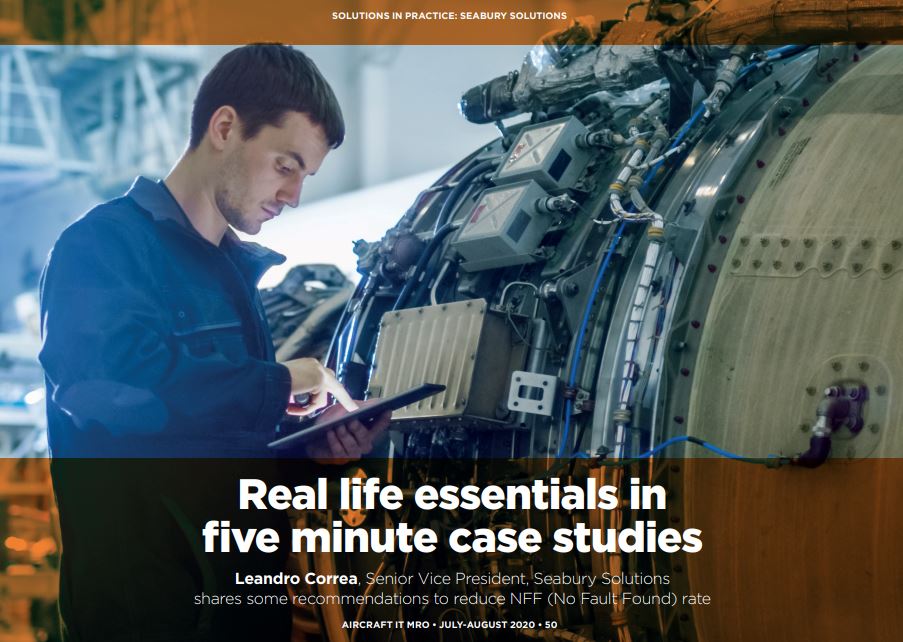
Brian Walsh, Sales & Marketing Executive, Seabury Solutions shares some recommendations to reduce NFF (No Fault Found) rate
The problem of erratic failures in aircraft equipment has long affected operators, who receive questionable components back from shops labeled ‘NFF’. For this reason, operators need to be aware of NFF (No Fault Found) rates. If a maintenance action results in a part removal from an aircraft due to an existing system or component diagnostic fault, but the repair/overhaul process did not validate the fault, this results in the replacement of the part being considered as not technically justified. This condition is called NFF and should be avoided in order to minimize the maintenance cost.
The reliability process allows an airline to explore reliability information for its airplanes and their components, during a specific period. An airline can compare its reliability to the overall fleet reliability, understand the cost of schedule interruptions, analyze solutions, and prioritize service bulletins based on the impact to its fleet. In accordance with this information, there are multiple factors that impact the reliability of components and, consequently, the costs associated with component maintenance.
Data released from some airlines in the Americas have demonstrated high levels of NFF. Around 15% of components, across all workshops, were found to have NFF. Along with that, certain avionics equipment also experienced up to 20% NFF. An operator and client of Seabury Solutions, that used the reliability module within the integrated aircraft maintenance solution, Alkym, established that 12% of the overall NFF are avionics components. These figures will obviously be different from operator to operator, as those who have their own shops (or at least service and test facility) would not be as worried as those who have a component exchange program.
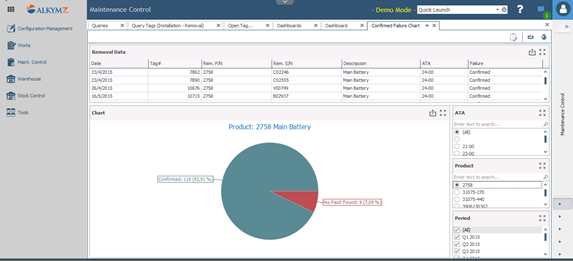
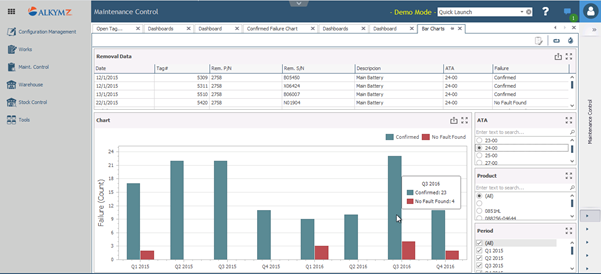
IMPACT OF NFF
The impact of NFF on maintenance costs are not confined to civilian airline operators. According to military data from some Air Forces in South America they had a 20% of unscheduled removals reported as NFF. Wasteful maintenance will cost a great deal of money for valuable resources, e.g. transportation costs of moving removed units to the appropriate workshop or manufacturer – especially for operators not located in USA or Europe-, which also includes the additional time spent on further testing and diagnostics. Other logistical activities also include the costs of processing activities and storage of the removed LRU’s.
A fault that re-occurs often doubles the costs, not to mention producing great frustration for managers, engineers and the operators who rely on a reliable, working and cost-effective product. It is hence widely acknowledged that reducing NFF events has the potential to reduce overall maintenance costs. These costs can be realized in terms of optimization of spare parts, increased logistic efficiencies, reductions in workshop time improved test equipment and personnel training
Another factor is when numerous products exhibit NFF problems (or a single product has a regular occurrence of NFF), the supplier or workshop that performs the repair may receive an unfavorable reputation for unreliability. This can be very costly if the product is warranted and returns are much larger than forecast.
FACTORS CAUSING AN NFF
Today, highly complex aircraft are equipped with more and more electronic sensors, computers, control functions and wires; not all conditions can be replicated on a test bench. Many factors can cause an NFF. Here are just a few examples:
- Inaccurate in-flight or line maintenance diagnosis;
- Multiple component removals to address a single failure;
- Inaccurate or incomplete bench testing at repair shops or by the equipment OEMs;
- Inability to accurately duplicate the circumstance in which a component fails;
- Rogue units – a specific serial number that produces the same fault within a short timeframe when installed on wing.
Effective fault identification by the line mechanic is a prerequisite. Only confirmed failure should be included. NFF is a major issue that results in high administrative burden and wasted expenditure.
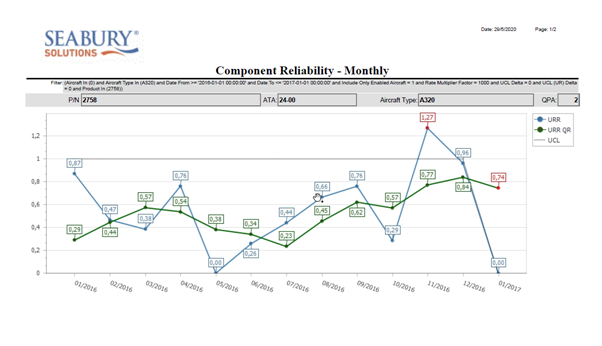
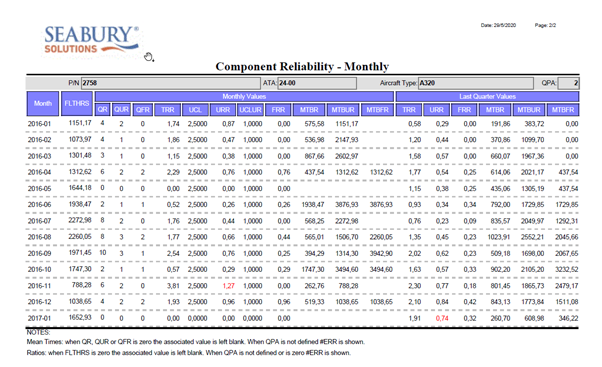
IMPROVING THE NFF RATE
Some recommended practices to improve NFF rate are detailed below:
- Optimize troubleshooting processes: learn from experience and the sharing of best practices with other interested areas to get better results. The best way to avoid high NFF rates is effective troubleshooting, using your own or other airline’s experience in order to optimize certain troubleshooting steps. If component maintenance is outsourced to a service provider, it is important to have a feedback loop with the line or base maintenance provider. Alkym has tools to record and manage the troubleshooting process sharing information between line maintenance, maintenance control and logistics management. Alkym also allows reliability reporting and troubleshooting summary reports that can be shared with other airlines and the OEM.
- Be aware of vendor warranties, component pooling agreements, aircraft leasing contracts, etc. Alkym keeps an online warranty monitoring applied to all avionics components and allows management of different pooling agreements.
- Ensure accurate and maintainable reporting by line mechanics. The Alkym Mobile tool allows comprehensive reporting by technicians providing effective fault identification.
- Track cost effectiveness. Alkym Dashboards allows users to track and monitor all component costs, identifying costs related to NFF.
- Track high NFF components, issue maintenance tips to avoid re-occurrences. NFF Alerts and automatic notifications are generated from Alkym to heighten the awareness of maintenance and procurement managers about different NFF cases.
- Make use of the On-board Maintenance System (OMS) to reduce NFF. Alkym can interface with different OMS to allow online data collection and analysis.
- Use Maintenance Control for technical support. The Alkym Planning tool and Fleet Monitoring tool provides the required information in a friendly way to deal with NFF cases that could impact on the operation.
- Educate cockpit crew on specific items to better understand what affects components’ life-on-wing, e.g. heavy landing’s impact on landing gear life; high speed taxiing’s impact of wheels and brakes; sharp steering angle’s impact on wheels, etc. Writing up detail defect information in the logbook may help line mechanics to fix problems more efficiently. Alkym is interfaced with several ETL solutions to optimize the recording of defect information by crew.
- Provide feedback to training departments in order for them to revise course content. The Alkym training module allows interaction with other modules to create and manage different training requisitions that could be related to NFF cases.
In the process of troubleshooting an aircraft system problem, certain airframe, engine or avionics components are replaced. However, in some instances, the first component change does not correct the problem.
Some airlines implement a SOS policy (Ship Or Shelf), which is designed to reduce excessive shop costs of components removed for troubleshooting that do not correct the problem and are not physically damaged. A unit determined to be in this category may be classified as serviceable and retained at the maintenance station for future use. The policy consists in placing a removed unit (eligible for SOS policy) in the SOS quarantine and monitoring the aircraft behavior during a few flights:
- If the fault does not re-appear, the unit replacement corrected the problem. The removed unit is then declared unserviceable and shipped for test/repair.
- If the fault re-occurs, the removed unit is declared serviceable pending results of a physical inspection.
Alkym allows the management of SOS policy providing alerts, notifications and creating automatic movements of parts in accordance with the predefined criteria set by the SOS policy.
Predictive maintenance tools can help operators to cut costs and reduce downtime. Airlines can take better advantage of the increasing amount of aircraft operational data available to support decisions and adjust maintenance planning. These tools use real-time access to aircraft data to provide enhanced fault forwarding, troubleshooting, and historical maintenance information. They allow operators to analyze data remotely, anticipate failures and procure spares. However predictive maintenance processes can also result in higher NFF rates, since a higher number of components are introduced into the repair/overhaul cycle based on predictions of impending failure of the component. However, once bench-tested in the shop as part of the repair cycle, the component may not demonstrate failure modes in the bench test procedures as when installed in the dynamic on-wing conditions resulting in an NFF score. The component is returned to the operator’s inventory along with the invoice for repair shop testing of the component.
Alkym is interfaced with On board systems to get real-time access to aircraft data, but then the Reliability module – taking all the available data – allows a smart and integrated analysis that improves the management of NFF considering also NFF costs as an important factor in the predictive maintenance strategy. Another factor is if numerous products exhibit NFF problems (or a single product has a regular occurrence of NFF), the supplier or workshop (that perform the repair) may receive an unfavorable reputation for unreliability. This can be very costly if the product is warranted and returns are much larger than forecast. Alkym allows users to track supplier, record repair reports and rank shops using different ranking criteria including a weight due to the NFF rate.
In conclusion, it is recommended to implement methodologies based on MIS (Maintenance Information System) data to minimize overhaul and repair costs and to monitor for components with the highest NFF rates. The proper use of data provided by an MIS system like Alkym helps operators to minimize NFF rates and pay attention to the NFF fees in the contracts. Reliability analysis requires the synergy between a systematic approach that has clear definitions of the reliability parameters, and a comprehensive collection of analysis techniques and procedures that can be managed using Alkym.
Contributor’s Details
Seabury Solutions
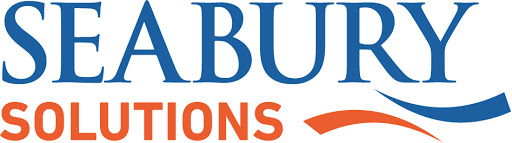
Part of the Seabury Capital, Seabury Solutions is a global aviation software development and consultancy company. The business has built its reputation in the market by delivering world class aviation IT solutions from the smallest operator to the largest airlines across the world. We have built upon our decades of aviation expertise in-house, to leverage this knowledge into a suite of products that enhance the decision making process for airlines, regulators and MROs.
Comments (0)
There are currently no comments about this article.
To post a comment, please login or subscribe.