Articles
Name | Author | |
---|---|---|
Smart ideas to improve inventory management | Daniel Stromski, Managing Director, DA Aviation | View article |
IT systems adoption Part 1 | Allan Bachan, VP, Managing Director, MRO Operations, ICF | View article |
Realizing the gains from digital processes at Sabena Technics | François Doré, Deputy Director General Strategy and Innovation, Sabena Technics | View article |
The runway to recovery | Graham Grose, Vice President and Industry Director, IFS | View article |
Smart ideas to improve inventory management
Author: Daniel Stromski, Managing Director, DA Aviation
SubscribeDaniel Stromski, Managing Director, DA Aviation explains how Inventory and Asset Management can be powered by smart automation and AI&ML technologies.
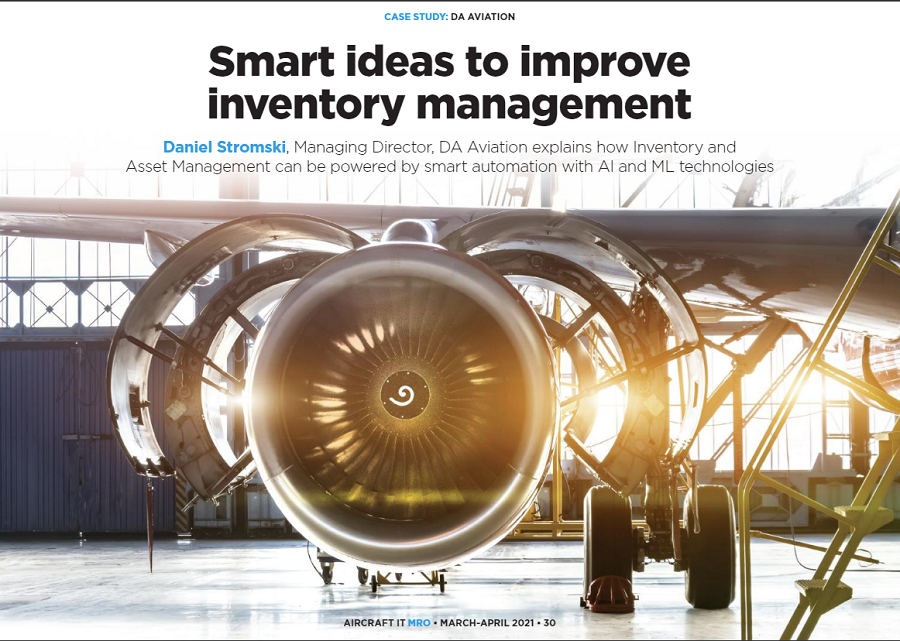
Nobody needs me to tell them that these are very challenging times with a high degree of uncertainty. And, while it’s good to see small signs of recovery appearing, it will require a plan for each organization, and some agility to overcome this unprecedented situation. To quote Yogi Bhajan, “To conquer the unknown you must trust.” But before we go into the core topic of this article, let me share with you a little about DA Aviation.
DA AVIATION
DA Aviation is a boutique consulting firm based in Australia and specializing in aviation inventory and asset management, supply chain and MRO. The firm supports MROs and small fleet operators in the general aviation space but also major commercial airlines. We have also developed a strong partnership with Ramco Systems, a tier 1 maintenance and engineering software provider at the forefront of applying AI (artificial intelligence) and ML (machine learning) capabilities in their solutions.
Services offered by DA Aviation include support with supply chain and MRO processes, examining the entire supply chain and MRO process to improve efficiency and reduce waste through the application of digital technology, artificial intelligence and machine learning capabilities. We also help in the area of asset and inventory management looking at asset and inventory structures to identify under-utilized assets and spare parts and help to turn assets into cash. On the other hand, we also look at ways to increase parts availability without necessarily incurring capital expenditure. The third area covered is digital transformation, where DA Aviation supports with developing digital roadmaps, help with planning and executing digital transformation projects not only by focusing on the solution itself but also, more importantly, by developing a holistic change management strategy so that the client organization can understand the ‘why’, a fundamental key success factor.
Some of the work undertaken by DA Aviation can be seen in figure 1.
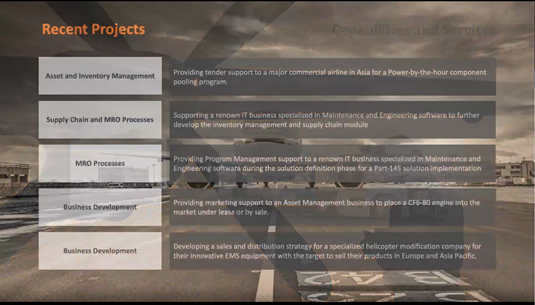
We have provided tender support for a major airline in Asia for a Power-by-the-hour component pooling program; we’re supporting a renowned IT business specialized in maintenance and engineering software to further develop their capability with regards to inventory and supply chain plus, at the time of writing, offering program management support to that IT business in the solution definition phase for a Part M solution implementation; we provide business development support to an asset management business to place a CF6-80 engine into the market through lease or sale. And finally, we support an Australian based specialized helicopter modification company with the strategic sales and distribution channel for their innovative EMS (Emergency Medical Services) equipment to sell into their target market of Europe and Asia Pacific.
TRAVEL DEMAND DRIVES PARTS DEMAND
Jumping into the main topic of this article, readers will already be aware of what is happening with the impact of COVID-19 on aviation but it’s also important to understand the consequences of what has happened and the way forward (figure 2).
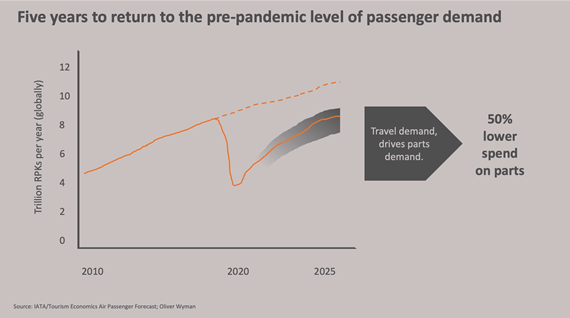
Overall COVID-19 has not only impacted flight operations, moving passengers from A to B, but subsequently it has also driven consequences for how inventory and assets need to be managed in the near future at least, if not for longer since travel demand drives parts demand. So what are the likely scenarios regarding inventory and asset management operations?
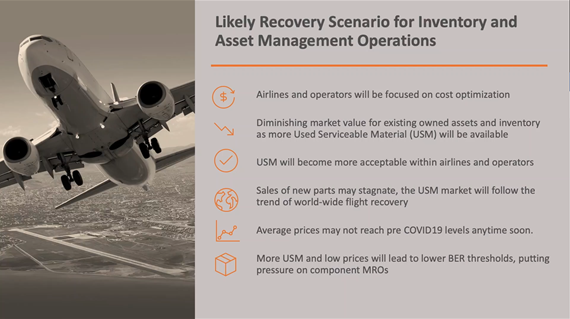
While recovery slowly proceeds it is still the case that airlines must keep a sharp eye on expenditure (figure 3). More usable material will become available due to early retirements of airframes having an impact on market values. Used serviceable material (USM) will become more acceptable to airlines and operators who need to save money. That, in turn, will also have the effect that new part sales will stagnate putting component OEMs under pressure. Due to the number of airframes parked in the desert and potentially not ever returning to service, providing a good stockfeed for USM, average prices might not recover anytime soon. More available used serviceable material and lower market values will lead to lower BER (Beyond Economical Repair) thresholds in the component repair business, eroding the business and business opportunities for component MROs
CHALLENGES FOR MANAGING INVENTORY
There are some quite significant challenges to managing inventory which are slightly different depending whether you are on the supplier side as an MRO or as an ITM (Inventory Technical Management) service provider or parts trader, or whether you’re on the side of an airline or an operator. For the first group, the question is really how to compensate for the reduced return on capital employed (figure 4).
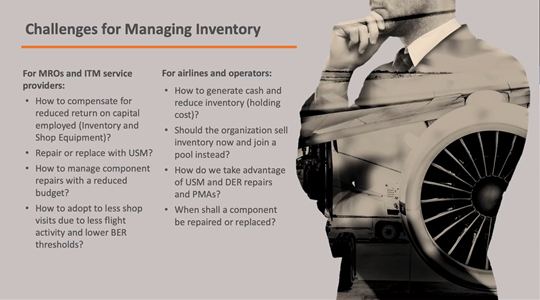
For a component MRO who has just invested a lot of money into a component shop or a test bench or IP agreements with the OEM but who is not getting the return in terms of repairs work due to reduced flight activities, this becomes a serious issue. Pooling providers who have invested in spares at pre-COVID prices are now facing the issue that, with reduced flight hour utilization of customer fleets worldwide, pooling programs will deliver lower returns.
Now, the question also is, should an MRO or a pooling provider repair or replace with used serviceable material and how to manage component repairs with a reduced budget? If a pooling provider is receiving less revenue because the airline is flying less hours than average across the fleet, that also means that a portion of the MRO fee will be reduced which then has an impact on the cost budget managing repairs. Probably more important for component MROs is how to adapt to fewer shop visits in the future because not only is lower flight activity an issue but also the lower BER thresholds because of the availability of used serviceable material in the market. As stated above, the airline or customers will try to save cost wherever possible and therefore tends to want to replace with USM, rather than repair.
From the airlines’ or operators’ perspective, more important than anything else at the moment is how to generate cash and reduce inventory along with the related inventory holding cost. Should the organization sell inventory now and join a pool instead or should they retain inventory now and weather the storm? Also, how can an airline take advantage of USM, DER (Designated Engineering Representatives) repairs and PMAs (Parts Manufacturer Approval)? Especially more conservative airlines might well become more open about it but would still be quite insecure about the application or usage of DERs and PMAs. However, due to cost saving initiatives across the entire organization, airlines may now be considering accepting alternative kinds of repairs. And, as also for the MRO and ITM Service providers, another question is when should a component be repaired or replaced? That decision requires data and it requires information about market values.
INVENTORY AND ASSET STRATEGIES ARE NOW REDEFINED
All these challenges combined could lead to a new strategy on how to manage inventory and assets (figure 5).
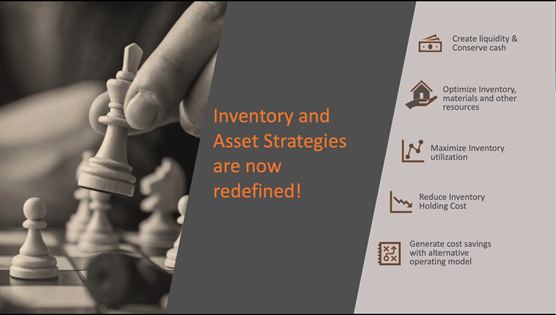
The number one strategic objective today is cash, no question about that; which means creating liquidity or conserving cash. The other strategic objectives aim to optimize inventory; in other words maximize inventory and asset utilization by, for example, getting rid of slow movers. This in return will reduce inventory holding costs. Additionally, and that is where agile and nimble organizations will have an advantage, develop alternative operating models in order to generate further cost savings.
A digital inventory management environment…
All these strategic objectives can be achieved by building a digital inventory management environment. So, what needs to be done? (figure 6).
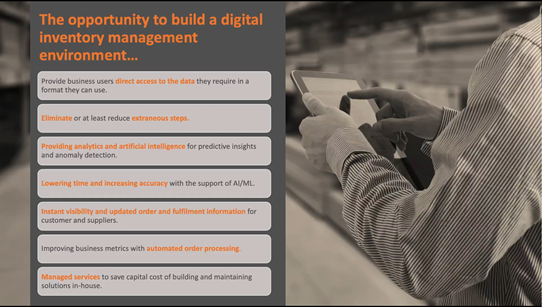
First and foremost, we need to provide business users direct access to the data they require and, more importantly, in a format that they can use. Secondly, eliminate or at least reduce extraneous steps. There is a huge opportunity, at the moment, to review processes, to find out and understand why certain steps are currently in the process map and whether these steps could be eliminated or at least reduced, maybe through the application of digital technology and automation? Systems also need to be providing analytics and artificial intelligence for predictive insights and anomaly detection; that, however, only works if data is available which only happens if the organization is set-up to collect the data, compute the data and make information available. With the support of AI (Artificial Intelligence) and ML (Machine Learning) we should also be reducing time for responses and increasing data accuracy in the process of data collection.
Automated order processing, real-time and instant visibility and updated order and fulfilment information for customers and suppliers will naturally lead to improved business metrics. There are many steps that can be automated nowadays in the processing of any kind of order, whether it’s a repair order, a purchasing order, an exchange or a loan order; there’s no need to shuffle information around by email, through Excel sheets and so on.
Last but not least, we must try to utilize managed services to save capital cost. Many organizations still spend money on their own in-house IT: there are resources available, there are people on the payroll to develop specific in-house IT solutions. That might have been worthwhile a decade ago or more, when the market did not provide services such as maintenance and engineering software: however, I think we can agree that there are organizations in the market, offering solutions which are far superior to whatever in-house solution might potentially be available.
How do we change this?
… to be enabled by technology and processes
First of all (figure 7), organizations need to integrate disconnected applications: too many organizations still work in digital silos with many small applications or so called ‘island solutions’, which do not communicate with each other.
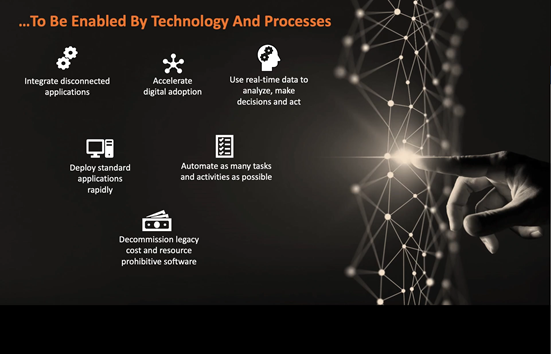
Then, organizations must now accelerate digital adoption: 2020 was the year to absorb the initial Covid-19 shock, 2021 is the time to accelerate, to work on the organization’s digital environment while things are still fairly slow. That will enable the organization to scale up and grow extraordinarily fast once business picks up again. Use real time data to analyze, make decisions and act. If you want an agile and nimble organization, you’ll need real-time data in order to make decisions and in order to act. In addition to that, employ standard off-the-shelf solutions rapidly, and automate as many tasks and activities as possible. Finally, stop flogging a dead horse by removing legacy (in-house developed) software that cannot keep up with the digital development of the market, but costs money and resources to keep it running. But why are those foregoing points so important?
THE FUTURE DIGITAL ECO SYSTEM
The answer is, because our industry is on a journey to build a digital eco system based on the Blockchain technology (figure 8).
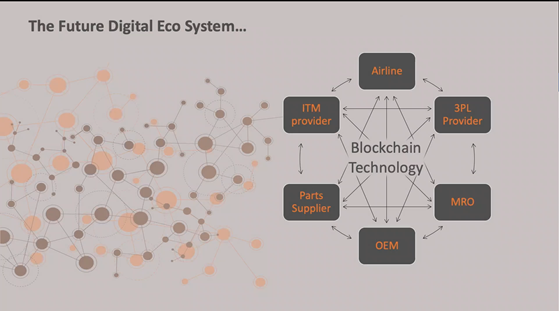
In February 2020, SITA announced the launch of the MRO Blockchain alliance, which had first been proposed in 2019 during a Blockchain conference initiated and organized by HAECO, with the aim of bringing the various stakeholders together and to set a global standard around the use of Blockchain to, for example, trace components and parts, providing full visibility for a component from cradle to grave. This alliance includes leading organizations in the space. Members currently include Bolloré Logistics, Cathy Pacific, HAECO Group, SITA, and Willis Lease Finance Corporation. FlyDocs and Ramco are providing technical support and last, but not least, law firm Clyde & Co. is providing support with all legal aspects regarding smart contracts.
By transforming your organization into a digital organization, you will automatically be well prepared to be part of the digital eco-system which will allow market participants to share information in a secure way in the near future.
DIGITAL ADOPTION TO MANAGE ASSETS AND INVENTORY – USE CASES
How can digital adoption help with managing assets and inventory? Here are a few use cases that should help to understand. We’ll look at three cases…
Use case 1 will focus on inventory holding costs;
Use case 2 will focus on reduction of direct maintenance costs; and
Use case 3 will focus on improved fulfilment of service levels.
Use case 1: Reduction of inventory holding costs
In this case, we’re considering how can AI and ML help with float planning and optimization as well as making AI/ML based sourcing recommendations.
Automated Inventory Level Calculation and Float Optimization (figure 9).
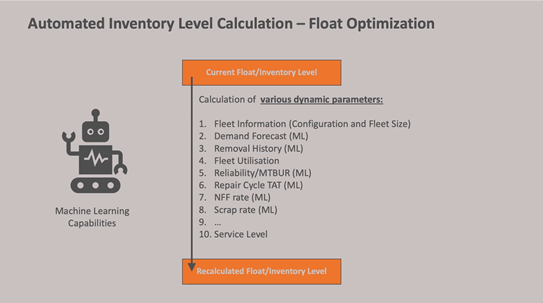
Where can machine learning, automation and artificial intelligence play a role? If we think about how to calculate the float, i.e., the inventory level required in order to sustain the business’s operations, to support flight operations; that’s a major task: there are many parameters to be considered and most of these parameters are dynamic. It is a huge effort to manually calculate the right inventory level for operations and, because it’s so huge, it’s only done sporadically. That is an ideal opportunity for machine learning and automation. While each organization will have their own method, commonly the information in figure 9 is required to calculate the float. However, the challenge is how to calculate various dynamic parameters, such as fleet information, demand forecasting based on maintenance schedules, etc. Many of them can be done using machine learning and artificial intelligence, for example with machine learning helping to collect the information from previous, say, heavy maintenance events. While every maintenance event will have scheduled component changes, there usually are many other parts which might also need to be replaced or need to be ordered during a heavy maintenance event, but which have not been planned for. To aggregate all of the information, all of the data, will help to better prepare for future heavy maintenance events by analyzing those unscheduled or unprepared material requests.
Further parameters such as removal history, historical fleet utilization and MTBUR (mean time between unscheduled removal) need to also be taken into account.
The MTBUR for example can be impacted by many factors; whether by implementing certain service bulletins (SBs), by improved troubleshooting practices, better maintenance activities or better repair schemes due to change of the repair supplier… many things can have an impact on the MTBUR. All of those things are dynamic and are perfect candidates for the application of AI and ML technologies.
Other dynamic parameters where ML can be of help are the repair cycle TAT (turnaround time), NFF (no fault found) and scrap rates; everywhere where there is an ‘ML’ in brackets are potential candidates to apply machine learning capabilities. Finally, as a component pool service provider or as an inventory manager there is obviously a need to define a service level, to support the airline’s operations. This service level will finally determine the required float, i.e. inventory level, to support operations.
In summary, because float calculation is a complex undertaking, there is a risk of incorrect provisioning of spares, which can cost a lot of money. Either because we stock assets which are no longer needed, or we grab into an empty shelf and then rectify that lack of an asset by loaning a part in from the market which is an expensive option. In other words, there is an opportunity to optimize inventory through the application of machine learning capabilities and artificial intelligence technologies.
Use case 2: Reduction of direct maintenance costs
In this case, we’ll look at repair order processing and how AI and ML can be applied to those processes (figure 10)…
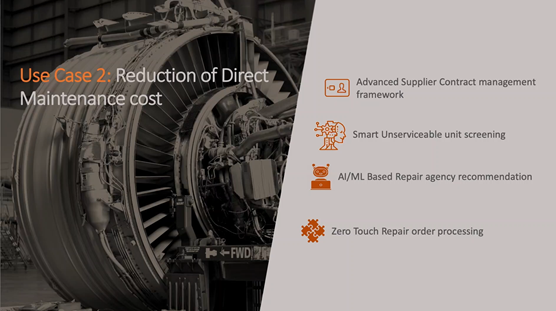
There are four major areas, in which AI and ML can be applied: Advanced Supplier Contract management, Smart unserviceable unit screening, AI/ML based repair agency recommendation and zero touch repair order processing. I would like to focus on the repair order processing.
Automated repair processing
After screening of the unit, the entire process of the repair order is automated (figure 11).
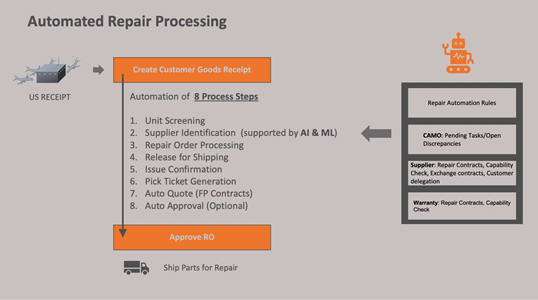
Once all parameters have been set up in the system, the receipt of an unserviceable part will trigger the automated repair order process; the system will pull up all the relevant AMS (Aircraft Maintenance Schedule) tasks and, possibly, ADs (Airworthiness Directives) and SBs (Service Bulletins) which need to be applied or implemented, and feed this information and other defect details into the repair order. Now, if the part can be serviced by multiple repair agencies, the AI algorithm will recommend the repair agency based on either historical data or on other parameters set up in the system (such as overhauls always at supplier A and regular repairs at supplier B). Based on the supplier contract, the quote and the approval process can then be automated or put on hold for getting an actual quote. If the unit is under warranty, the system will also identify that and then the repair order is set up for the respective repair agent who granted the warranty.
This automated process with support of AI and ML could at least eliminate or reduce extraneous steps and human intervention, while providing consistency and swift processing of repair orders.
Use case 3: Improved fulfilment of customer service levels
In this case, AI and ML could help to manage the contract framework more efficiently (figure 12).
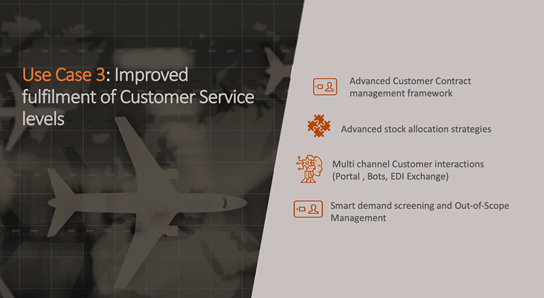
AI and ML could also help to develop and apply advanced stock allocation strategies. There are already solutions in place where customer interactions can be done through multiple channels such as chat bots or advanced EDIs (Electronic Data Interfaces). AI and ML could also support in the areas of demand screening and out-of-scope management: in other words, the system will detect automatically if a certain request is within the contract or outside of the contract and then manage the process accordingly.
Advanced stock allocation
Let’s take a look at the advanced stock allocation strategies (figure 13).
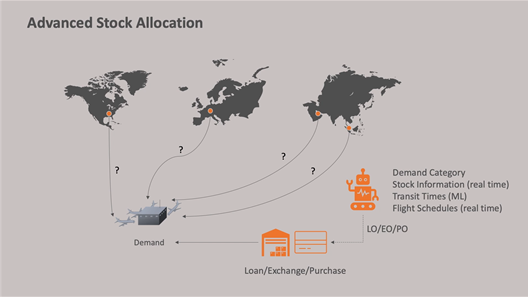
Nowadays, with many pooling suppliers around the world and most of the pool suppliers having multiple stock locations in Europe, North America, the Middle East and Asia, having the correct part in the right amount and in the correct location, becomes a challenge. The component pool customer or airline can have a demand anywhere in the world, but the challenge for pool suppliers, or the airline managing their own inventory, will be to understand and to decide from which stock location the part demand would ideally be satisfied? Having the part available in every location is not feasible and would be very costly and if the part is only available in one location, this question won’t arise anyway: however, it might be necessary to consider splitting the pool (and losing economies of scale) or reviewing where stocks of certain parts are spread around the world. The question is, how to allocate parts across multiple locations in order to fulfil part demands of multiple aircraft in adequate time?
AI and ML could be the answer. In case of a raised part demand, the system would scan the demand category of the customer – is it a critical demand, is it a MEL (minimum equipment list) restricted demand, how much time is there available to fulfil this demand? The AI empowered system will then scan the stock information in real time for all relevant stock locations around the world; with the help of ML capabilities the system will have learned various transit times to move the part from A to B and we might even have EDIs in place to access real time information of available flight schedules. This way the system can propose the optimum solution to deliver the part from a certain stock location to where the part is needed. And, as icing on the cake, if the system comes to the conclusion that there is no stock available and/or the part could not be supplied within the required contract delivery time, risking a service level penalty, the system can be programmed so that it will automatically raise a loan order, an exchange order or a purchase order to a supplier who will fulfil the demand on behalf of the pool provider.
WHO CAN MAKE IT HAPPEN?
Having considered the three use cases, the next question that arises is who can actually do the things that were highlighted in the cases? Ramco Systems is at the forefront in the application of AI and ML powered MRO software. The company has a global presence with customers around the world including MROs, commercial airlines, aircraft operators, helicopter operators, OEMs and defense contractors. The solution offers a wide spread of applications and modules from engineering, CAMO, maintenance, supply chain management, safety compliance and quality, flight operations, employee records, MRO parts sale, manufacturing, and finance and accounting. A fully integrated ERP suite for any aviation or aerospace company and a modular system – it is not necessary to have the whole suite implemented but users can pick and choose from the range of solution modules and Apps to their operation and business model.
That concludes the article which, I hope, has added to readers knowledge of applying the latest technologies in inventory and asset management, what those technologies can achieve and where to find the technologies.
Contributor’s Details
Daniel Stromski
Daniel Stromski began his career as a Logistics Officer in the German Airforce before moving to Lufthansa Technik’s Aircraft Component Division in 2008. During his tenure he was seconded to Lufthansa Technik Shenzhen to set up additional component repair capabilities, developing this facility to a significant Component MRO within LHT’s network. In 2016, Daniel joined HAECO ITM Ltd., a joint-venture company between HAECO and Cathay Pacific Airways. As Executive General Manager he was leading the asset and inventory management business and driving the digital transformation of the organization. In January 2020, Daniel started his own consultancy business in the area of asset and inventory management and application of digital technologies. He holds a Diploma in Industrial Engineering and a Bachelor of Laws.
Ramco Aviation
Ramco Aviation Software is trusted by 24,000+ users to manage 4,000+ aircraft globally. Accessible on cloud and mobile, Ramco Aviation Software continues to innovate with ‘Anywhere Apps’, significantly reducing transaction time both during aircraft-on-ground (AOG) conditions and critical aircraft turnarounds. Ramco is changing the paradigm of enterprise software with Artificial Intelligence and Machine Learning based solutions, powered by cool new features such as digital task cards, offline capability, chatbots, email-based transactions, HUBs and cognitive solutions. With 80+ Aviation organizations onboard, Ramco is the solution of choice for top heli-operators, leading defense and multiple MROs around the world.
DA Aviation Management
DA Aviation Management and Business Consultancy is a consulting firm based in Australia and specialized in aviation inventory and asset management, supply chain and MRO. The firm supports MROs and small fleet operators and major commercial airlines. Capabilities and services include supply chain and MRO processes, examining the supply chain and MRO process with the goal to improve efficiency and reduce waste through the application of digital technology, artificial intelligence and machine learning capabilities.
Comments (0)
There are currently no comments about this article.
To post a comment, please login or subscribe.